What Are Automated Warehousing Systems?
Automated warehousing systems are technology-driven solutions designed to streamline, optimize, and enhance the efficiency of storage, retrieval, and order fulfillment processes in warehouses.
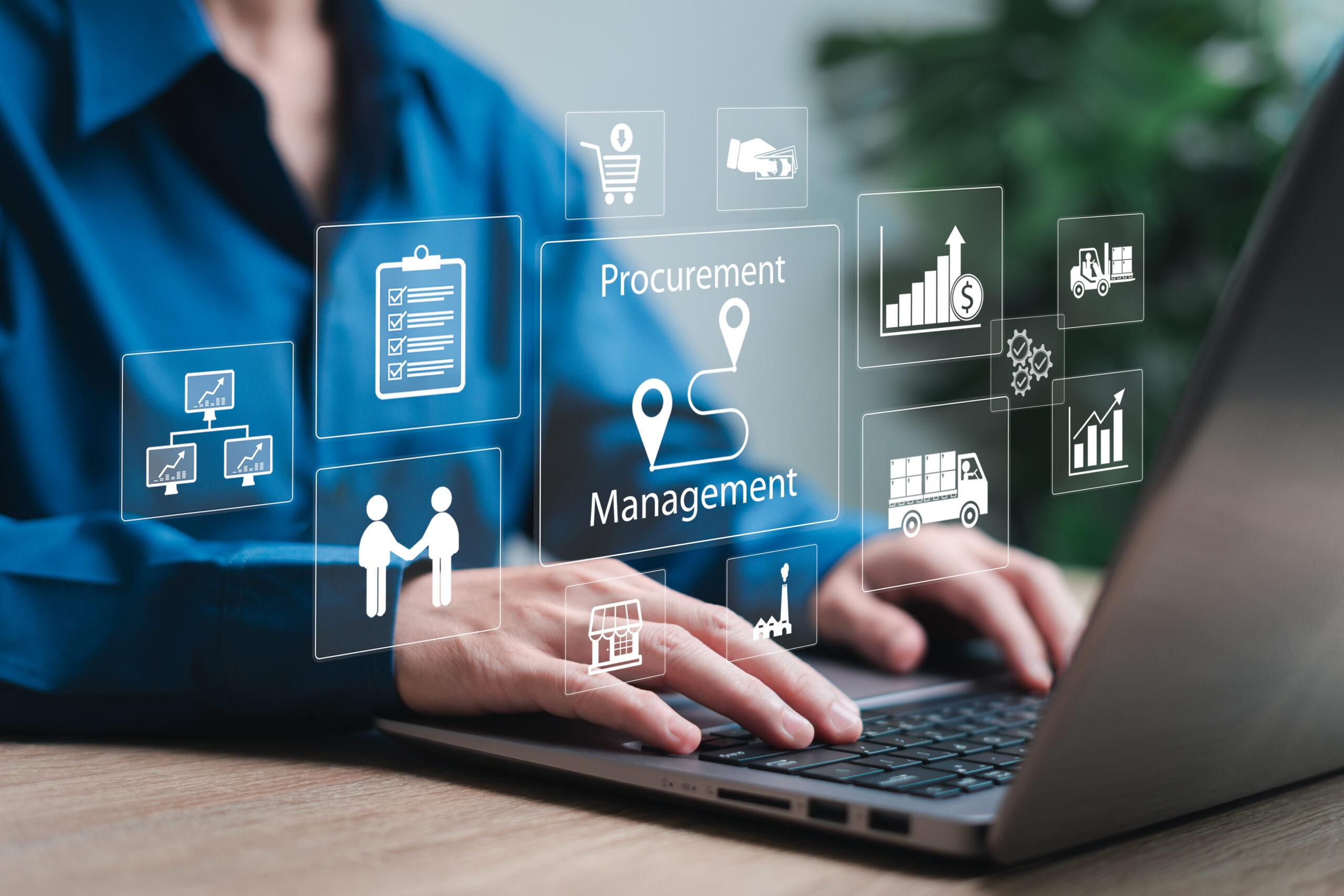
These systems integrate robotics, software, and advanced machinery to handle tasks traditionally performed manually, such as inventory management, picking, and packing. By automating these operations, businesses can significantly reduce errors, minimize labor costs, and improve throughput.
In modern supply chains, the importance of automated warehousing systems cannot be overstated. As consumer demand for faster delivery and accurate order fulfillment grows, these systems provide a critical edge. They enable companies to stay competitive by enhancing operational efficiency, ensuring scalability, and adapting to the dynamic nature of e-commerce and global logistics. Automation not only boosts productivity but also supports sustainability goals through optimized resource utilization and energy-efficient designs.
Types of Warehouse Automation
Warehouse automation can be categorized into basic and advanced technologies, each offering varying levels of efficiency and complexity to suit different operational needs.
Basic Automation Technologies
Basic automation involves tools and processes designed to simplify tasks without extensive robotics or software integration. Examples include conveyor systems, carousels, and sortation equipment. These technologies improve efficiency by reducing manual labor and streamlining repetitive tasks, such as moving goods from one point to another or sorting orders based on destination.
Advanced Automation Technologies
Advanced automation incorporates cutting-edge robotics, sophisticated software, and interconnected systems to create seamless operations. Examples include robotic arms, automated guided vehicles (AGVs), autonomous mobile robots (AMRs), and Artificial Intelligence (AI)-driven solutions. These technologies enable dynamic decision-making, real-time inventory updates, and precision in tasks such as picking, packing, and storage.
Examples of Warehouse Automation Technologies
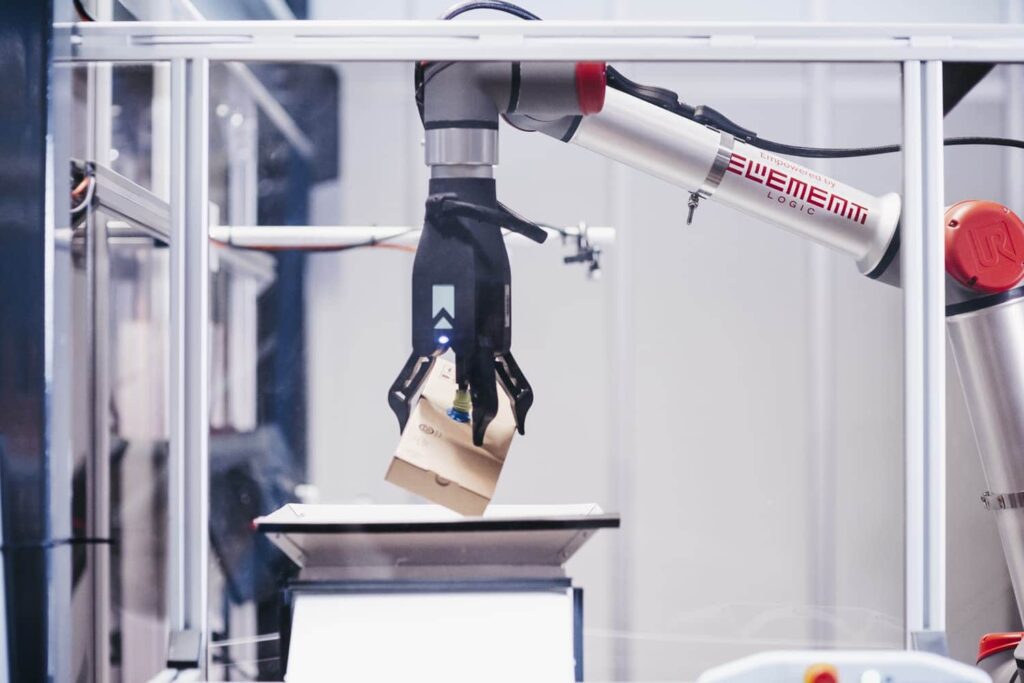
- Robotics
Robotic solutions are at the forefront of warehouse automation, providing speed and precision in handling repetitive and labor-intensive tasks. For instance, robotic picking systems can identify, select, and place items with minimal human intervention, drastically reducing errors and increasing throughput. Collaborative robots, or “cobots,” work alongside human employees, enhancing productivity without replacing the human workforce entirely. - Automated Storage and Retrieval Systems (ASRS)
ASRS are highly efficient systems designed to automatically store and retrieve goods with minimal manual effort. These systems use cranes, shuttles, or lifts to move items within densely packed storage facilities. ASRS optimizes space utilization, reduces retrieval time, and improves inventory accuracy, making it an ideal solution for businesses with high-volume operations or limited warehouse space.
By combining these technologies, warehouses can achieve unparalleled efficiency and adapt to the growing demands of modern supply chains. Would you like to dive deeper into specific technologies or focus on integration strategies?
Key Benefits of Warehouse Automation
Warehouse automation offers transformative advantages that streamline operations and drive business growth. Below are two of the most impactful benefits:
Increased Productivity and Reduced Operational Costs
Automated systems enable faster and more efficient handling of tasks such as picking, packing, sorting, and storage. By reducing reliance on manual labor, companies can significantly increase throughput and meet the demands of rapid order fulfillment. For example, robotic picking systems can work around the clock with consistent accuracy, dramatically improving productivity.
Additionally, automation reduces operational costs by minimizing errors, cutting down labor expenses, and optimizing energy usage. Advanced systems like ASRS also maximize storage space, lowering the need for costly warehouse expansions. Over time, these cost savings contribute to a strong return on investment, making automation a financially sustainable solution.
Enhancing Worker Safety and Reducing Errors
Warehouse environments can be physically demanding and hazardous, with risks of injuries from repetitive tasks, heavy lifting, or operating machinery. Automation alleviates these challenges by handling dangerous or strenuous tasks, ensuring a safer workplace for employees. AGVs, for example, transport heavy loads with precision, reducing the risk of accidents.
Automation also drastically reduces human errors in processes like inventory management and order fulfillment. Technologies such as barcode scanners, sensors, and AI-powered systems provide real-time tracking and verification, ensuring that items are accurately identified, stored, and shipped. This level of precision enhances customer satisfaction and builds trust in supply chain reliability.
These benefits underscore why businesses are increasingly turning to automation to remain competitive in today’s fast-paced logistics landscape.
Top Warehouse Automation Technologies in 2025
As warehouse operations evolve, automation technologies are becoming increasingly advanced, revolutionizing the logistics industry. Here are some of the standout technologies shaping warehouses in 2025:
Robotics, Drones, and Automated Picking Systems
Robots and drones are leading the charge in warehouse automation.
- Robotic Systems: Robots, including collaborative robots (cobots) and autonomous mobile robots, are widely used for picking, packing, and transporting goods. These robots operate efficiently in high-density storage areas, reducing the need for manual intervention and improving speed.
- Drones: Inventory management drones are becoming indispensable, especially in large-scale warehouses. They perform aerial scans to count stock, track inventory, and locate items with remarkable accuracy and speed.
- Automated Picking Systems: Advanced picking systems combine robotics and AI to identify and retrieve items from storage locations with unmatched precision. These systems integrate seamlessly with other automation technologies, enabling faster order fulfillment.
Software Solutions: Warehouse Management Systems and Cloud-Based Platforms
Software plays a critical role in orchestrating automated warehouse operations.
- Warehouse Management Systems (WMS): WMS software provides a centralized platform for managing and optimizing warehouse activities. It tracks inventory, guides picking and packing, and ensures accurate order fulfillment. Integrated with automation hardware, WMS enhances overall efficiency and minimizes downtime.
- Cloud-Based Platforms: Cloud-based systems allow real-time data sharing across multiple locations, enabling better decision-making and streamlined operations. These platforms support scalability and remote management, making them ideal for businesses looking to grow or manage geographically dispersed operations.
Together, these technologies create a cohesive, future-ready ecosystem that addresses the demands of modern supply chains. As businesses invest in these advancements, the efficiency, safety, and adaptability of warehouses continue to reach unprecedented levels.
Automated warehousing systems are transforming logistics across industries, with leading companies leveraging these solutions to enhance efficiency, accuracy, and scalability. Below are a few real-world examples showcasing the impact of automation:
Case Studies: Leading Companies Using Automated Solutions
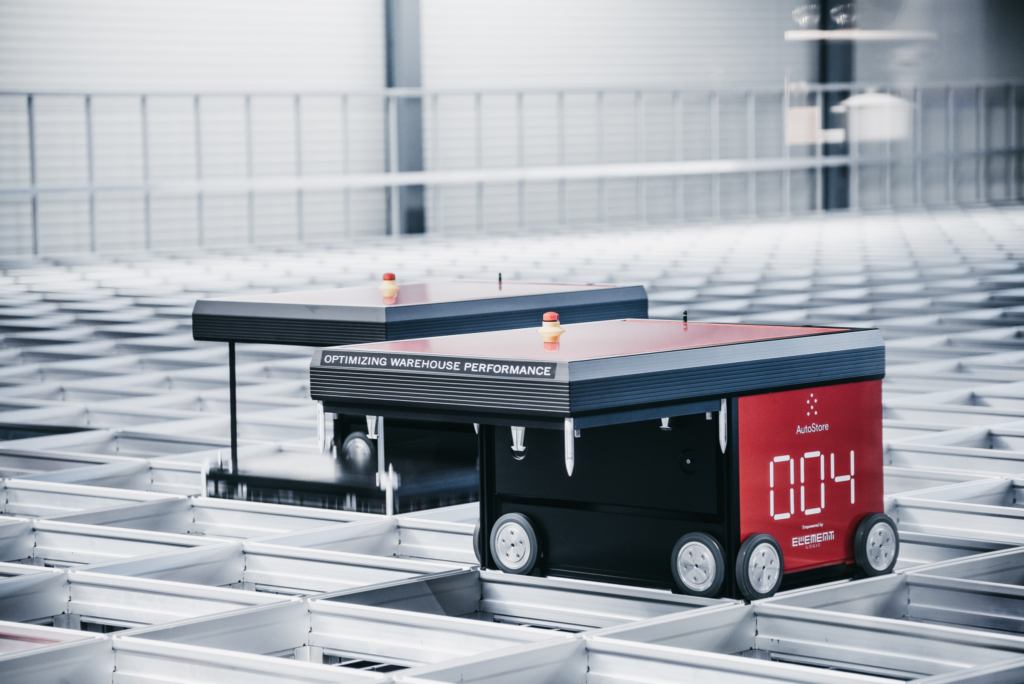
Real-World Examples of Automated Warehousing Systems
Automated warehousing systems are transforming logistics across industries, with leading companies leveraging these solutions to enhance efficiency, accuracy, and scalability. Below are a few real-world examples showcasing the impact of automation:
- Element Logic and AutoStore
Element Logic leverages the AutoStore system to offer cutting-edge solutions for small and medium-sized warehouses. AutoStore’s modular design and robotics-driven approach optimize space usage while improving throughput. This technology has been particularly impactful for e-commerce businesses seeking efficient and scalable solutions. - Zara: Fast Fashion Supply Chain
Zara employs automated storage and retrieval systems in its distribution centers to support its fast-fashion business model. These systems allow the company to maintain tight control over inventory and ensure rapid restocking across its retail network. With automation, Zara can process and distribute new collections to stores in record time, keeping up with ever-changing fashion trends. - Amazon: Robotic Fulfillment Centers
Amazon is a pioneer in warehouse automation, with over 500,000 robotic drive units operating in its fulfillment centers globally. These robots, combined with sophisticated algorithms, streamline picking, sorting, and packing processes, enabling the company to handle millions of orders daily. By integrating robotics with advanced software, Amazon has reduced order processing times while maximizing storage capacity. - Walmart: Drone Inventory Management
Walmart has adopted drone technology for inventory management in its large-scale warehouses. These drones perform aerial scans, updating stock levels in real time and reducing the need for manual checks. This approach not only saves time but also enhances inventory accuracy, supporting Walmart’s vast retail network. - Ocado: Grocery Warehouse Automation
Ocado uses a highly automated system where robots move seamlessly across grids to retrieve and deliver items to human packers. Their proprietary technology enables rapid and accurate order fulfillment, setting a benchmark for efficiency in the grocery industry.
These examples highlight how automation is reshaping warehouse operations, enabling companies to stay competitive in fast-paced markets.
How to Choose the Right Automation Solution for Your Warehouse
Selecting the ideal automation solution for your warehouse requires careful consideration of your operational needs, budget constraints, and the available technologies. Here’s a guide to help you make an informed decision:
Evaluating Needs and Budget Considerations
- Assess Current Operations: Begin by analyzing your warehouse’s workflow, identifying bottlenecks, and understanding areas where automation can drive the most impact. For instance, if order picking is slow and error-prone, consider automated picking systems.
- Define Objectives: Clearly outline your goals, whether they are reducing costs, increasing throughput, enhancing accuracy, or improving safety. Align these objectives with your business strategy and growth plans.
- Set a Realistic Budget: Automation solutions range from basic to advanced, with costs varying accordingly. Determine your budget and weigh the return on investment (ROI) against the upfront and ongoing expenses. Factor in costs for installation, training, and maintenance.
Challenges in Implementing Warehouse Automation
While warehouse automation offers significant benefits, its implementation comes with challenges that businesses must address for successful integration. Below are some common issues and strategies to overcome them…
Common Issues in Warehouse Automation
- High Initial Costs
Challenge: The upfront investment for automation technologies, including hardware, software, and infrastructure changes, can be substantial. This is a common concern, especially for small-to-medium-sized businesses.
Solution: Conduct a detailed ROI analysis to justify the costs and explore modular or phased implementation. Starting with a scalable solution like AutoStore can spread costs over time. - Integration with Existing Systems
Challenge: Merging new automation technologies with legacy systems can be complex, leading to delays and potential disruptions.
Solution: Invest in middleware or APIs that facilitate seamless integration between new and existing systems. Collaborate with experienced vendors to ensure compatibility. - Workforce Resistance
Challenge: Employees may resist automation due to concerns about job security and unfamiliarity with new technologies.
Solution: Emphasize upskilling and training programs to help employees adapt to new roles that involve supervising or maintaining automated systems. Communicate the benefits of automation, such as improved safety and efficiency, to gain their buy-in. - Customization Requirements
Challenge: Off-the-shelf automation solutions may not fully address unique operational needs, requiring customization that can extend timelines and costs.
Solution: Work with solution providers to design systems tailored to your specific requirements or choose modular systems that offer flexibility without extensive customization. - Downtime During Implementation
Challenge: Transitioning to automated systems can temporarily disrupt operations, affecting productivity and customer service.
Solution: Implement automation in phases to maintain operational continuity. Schedule installations during off-peak periods and conduct rigorous testing before full deployment. - Maintenance and Technical Support
Challenge: Automated systems require ongoing maintenance and access to skilled technical support, which can be resource intensive.
Solution: Partner with vendors offering robust support services and consider proactive maintenance solutions like eLogiq’s uptime management, which predicts and prevents issues before they arise.
By identifying and addressing these challenges early in the planning process, businesses can minimize risks and maximize the benefits of warehouse automation.
Future Trends in Warehouse Automation
Warehouse automation continues to evolve, driven by advancements in technology and the increasing demands of modern supply chains. The future of warehousing is set to become more connected, efficient, and intelligent, with emerging technologies playing a central role in shaping operations.
Artificial intelligence and machine learning (ML) will revolutionize decision-making in warehouses by enabling predictive analytics, optimizing workflows, and improving inventory accuracy. AI-powered systems can predict demand fluctuations and adjust inventory levels accordingly, reducing the risk of stockouts and overstocking.
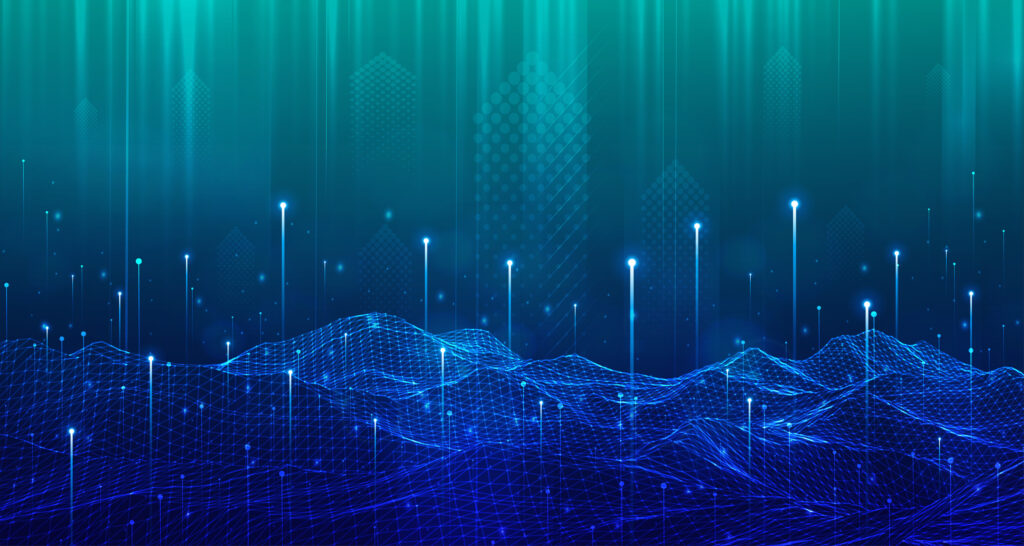
The Internet of Things (IoT) will further enhance warehouse connectivity by creating a real-time digital ecosystem where sensors and smart devices monitor equipment performance, track inventory, and ensure environmental compliance, such as temperature control for perishable goods.
Meanwhile, the implementation of 5G networks will enable faster and more reliable communication between automated systems, facilitating real-time data exchange between robots, drones, and software for improved synchronization and operational efficiency. Collaborative robots (cobots) will become increasingly common, working alongside human workers to handle repetitive or labor-intensive tasks with enhanced AI-driven safety features.
Blockchain technology will bring greater traceability and security to warehouse operations, allowing businesses to verify product authenticity, track movement, and improve transparency in multi-party transactions.
Looking ahead, hyper-automated warehouses will integrate advanced robotics, AI, IoT, and cloud-based systems into a seamless operation, minimizing manual intervention and maximizing efficiency. Sustainability will also become a key focus, with energy-efficient robots, renewable energy sources, and sustainable packaging solutions playing a critical role in reducing waste and carbon footprints.
The rise of micro-fulfillment centers, strategically located to meet the demand for same-day and next-day delivery, will rely on compact, high-density storage systems to optimize space efficiency. Beyond warehouse walls, autonomous vehicles, including drones for last-mile delivery and self-driving trucks for inter-warehouse transportation, will transform supply chain logistics.
By embracing these trends, businesses can position themselves at the forefront of innovation, ensuring they are prepared to meet the challenges of tomorrow’s logistics landscape.