Warehouse Safety Tips: Best Practices to Follow
A well-functioning warehouse is a harmonious symphony of coordinated movements, streamlined processes, and efficient workflows.
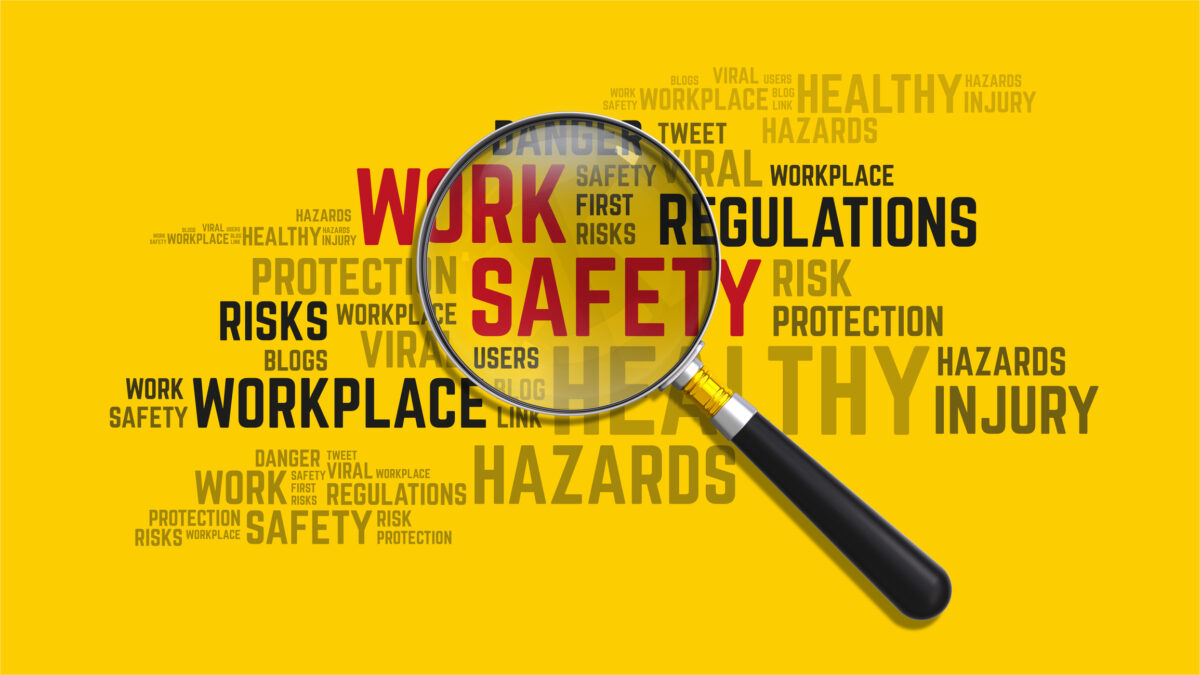
However, the primary concern should always be the safety of those who contribute to so-called orchestra. Warehouse safety isn’t merely a regulatory obligation; it is the linchpin that holds the entire operation together.
Ignoring safety measures within the warehouse isn’t just a gamble; it’s a perilous risk that can have far-reaching consequences. The repercussions of neglecting safety extend beyond the immediate impact of injuries or accidents. They seep into company productivity, erode employee morale, and can lead to significant financial losses. In an environment where heavy machinery, elevated storage, and tight deadlines come together, safety isn’t an option—it’s imperative.
In this blog, we will delve into the crucial elements of warehouse safety including OSHA Safety, some common warehouse injuries, warehouse safety tips, and a warehouse safety checklist. Join us on this exploration of warehouse safety, where we aim to empower businesses and individuals with the knowledge and practices necessary to uphold the highest standards of safety within their warehouses.
What is warehouse safety?
The simple definition of warehouse safety is the act of implementing measures to prevent accidents, injuries, and hazards within a storage facility. This includes adherence to strict protocols, guidelines, and regulations to ensure the well-being of workers and the protection of goods. A comprehensive approach to warehouse safety not only safeguards personnel but also enhances operational efficiency and minimizes the risk of damage to inventory.
OSHA Safety: An Overview
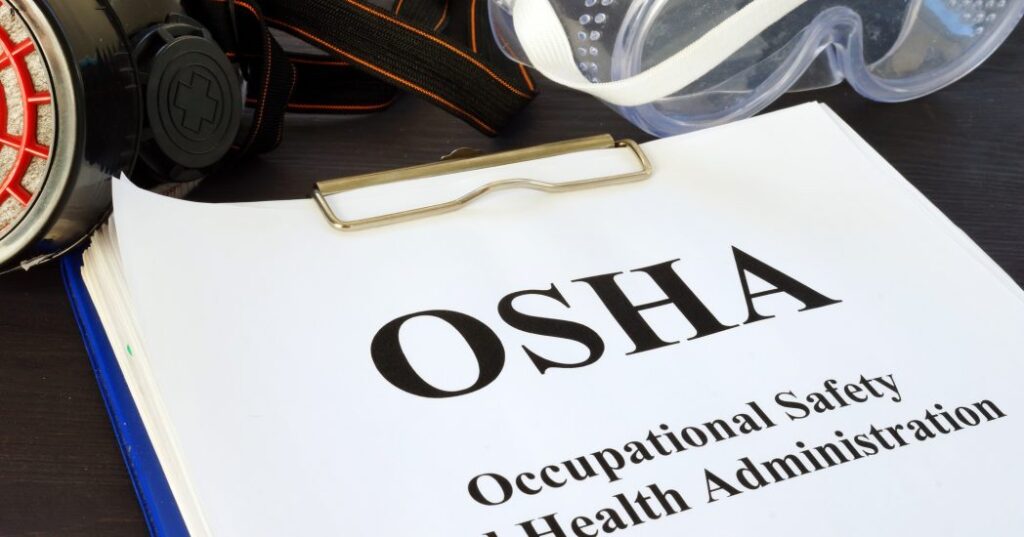
The Occupational Safety and Health Administration, or OSHA, is a federal agency within the United States Department of Labor. Established in 1971, OSHA’s primary purpose is to ensure safe and healthy working conditions for employees across various industries. OSHA sets and enforces standards to protect workers from hazards and advocates for the reduction of workplace injuries, illnesses, and fatalities.
OSHA within the warehousing industry plays a crucial role in regulating safety standards. The agency develops and enforces guidelines that address a wide range of workplace hazards, including those specific to storage and distribution facilities. OSHA standards cover aspects such as material handling, forklift operation, machine guarding, electrical safety, ergonomics, and the handling of hazardous materials.
Additionally, employers are required to comply with OSHA standards, which often involve implementing safety programs, providing training to employees, maintaining records of workplace injuries and illnesses, and undergoing periodic inspections. OSHA may conduct inspections and investigations to ensure that workplaces adhere to these standards, and non-compliance may result in penalties and fines.
By promoting a culture of safety and establishing regulations tailored to specific industries, OSHA contributes to creating healthier and safer work environments, ultimately reducing the risk of accidents, and improving the overall well-being of workers.
10 Common Warehouse Injuries
- Slips, Trips, Falls:
- Causes: Wet or slippery floors, uneven surfaces, poor lighting, and cluttered walkways.
- Prevention: Regular cleanings, proper signage for wet floors, adequate lighting, and employee training on safe walking practices.
- Forklift Accidents:
- Causes: Improper operation, lack of training, inadequate maintenance, and pedestrian-traffic interaction.
- Prevention: Comprehensive forklift training, clear pedestrian walkways, routine equipment maintenance, and implementation of safety protocols.
- Material Handling Injuries:
- Causes: Incorrect lifting techniques, overexertion, repetitive motion, and use of improper equipment.
- Prevention: Employee training on proper lifting methods, use of ergonomic equipment, and rotation of tasks to reduce repetitive strain.
- Struck by Falling Objects:
- Causes: Poorly stacked inventory, inadequate shelving, and improper use of storage equipment.
- Prevention: Proper stacking and storage procedures, securing loads, and regular inspections of storage systems.
- Electrical Shocks:
- Causes: Faulty equipment, damaged wiring, and unsafe use of electrical devices.
- Prevention: Regular equipment maintenance, electrical inspections, and employee training on electrical safety.
- Cuts or Lacerations:
- Causes: Improper use of tools, lack of personal protective equipment (PPE), and inadequate training.
- Prevention: Provision of appropriate PPE, training on tool safety, and regular tool inspections.
- Fire Incidents:
- Causes: Electrical faults, flammable materials, and poor storage of combustible items.
- Prevention: Adequate fire prevention measures, fire extinguisher training, and proper storage of flammable materials.
- Chemical Exposures:
- Causes: Improper handling or storage of chemicals, and lack of protective gear.
- Prevention: Proper labeling and storage of chemicals, use of appropriate PPE, and employee training on chemical safety.
- Eye Injuries:
- Causes: Flying debris, chemical splashes, and inadequate eye protection.
- Prevention: Provision of suitable eye protection, training on eye safety, and implementation of safety measures in areas with potential eye hazards.
- Respiratory Issues:
- Causes: Exposure to dust, fumes, or harmful gases without proper respiratory protection.
- Prevention: Use of respiratory protection when required, ventilation systems, and employee training on respiratory hazards.
Warehouse Safety Tips
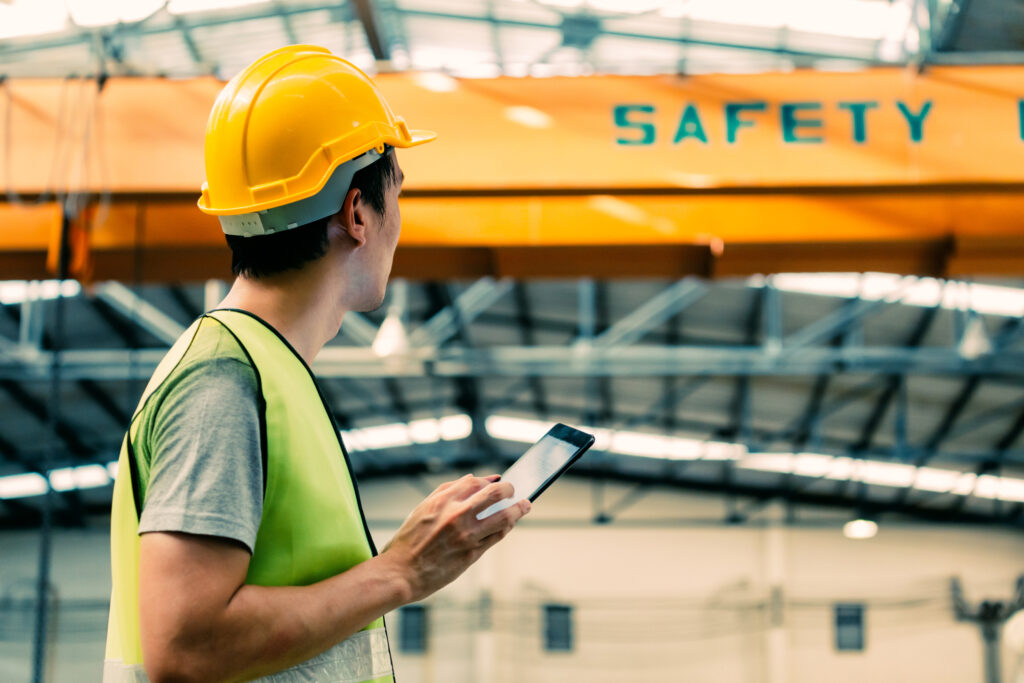
Implementing warehouse safety tips requires a collaborative effort between management and staff to create a culture that prioritizes safety, reduces risks, and ensures the well-being of everyone in the workplace. Regular training, communication, and a commitment to continuous improvement are key elements of a successful safety program. Below is a brief glance at some measures you should consider incorporating to maximize the safety of your warehouse employees and product.
- Employee Training: Conduct regular safety training for all warehouse staff to ensure they are aware of proper procedures, equipment usage, and emergency protocols.
- Proper Material Handling: Train employees in correct lifting techniques to prevent injuries and encourage the use of equipment like pallet jacks or forklifts for heavy loads.
- Equipment Safety for Warehouse Equipment: Establish strict safety protocols for equipment use, including forklifts, conveyor systems, and other machinery. Ensure routine maintenance and operator training.
- Fall Protection: Install guardrails, safety nets, or personal fall arrest systems in elevated areas as well as emphasizing the use of fall protection equipment for employees working at heights.
- Optimize Warehouse Layout: Make sure to design the warehouse layout to prioritize safety, with considerations for efficient traffic flow, clear visibility, and ergonomic workspaces.
Warehouse Safety Checklist
A warehouse safety checklist is a comprehensive document designed to systematically assess and ensure the adherence to safety protocols and practices within a warehouse or storage facility. It serves as a tool for warehouse managers, supervisors, and safety officers to routinely inspect and evaluate the safety conditions, equipment, and processes within the warehouse environment.
One of the things to add to your safety checklist is to review your safety storage practices. This includes verifying that materials are organized and stored securely, making sure that proper stacking and shelving techniques are being followed, and routinely checking for any damaged or improperly stored inventory.
Additionally, you will need to implement proper material handling techniques. You can do so by assessing whether employees are using correct lifting and carrying techniques, confirming the use of appropriate equipment for heavy or awkward loads, and ensuring that your workstations are ergonomically sound.
Our final tip for your warehouse safety checklist is to have regular inspections and maintenance. By confirming the schedule and completion of routine equipment inspections, checking the signs of wear and tear on machinery, shelving, and equipment, as well as assessing the overall cleanliness and orderliness, you will dramatically increase your chances of catching a safety issue before it becomes an issue.
Final thoughts on warehouse safety
In the dynamic landscape of modern warehouses, prioritizing safety is not just a regulatory requirement but a commitment to the well-being of your team and the efficiency of your operations. A comprehensive approach to warehouse safety involves a combination of employee training, adherence to best practices, and the integration of cutting-edge technologies.
In this pursuit of safety excellence, Element Logic stands as a pioneering partner. With a focus on innovative solutions and a proven track record in warehouse automation, Element Logic brings a unique blend of expertise to elevate your safety standards. Our AutoStore system is not just about efficiency and productivity; it’s about creating a safer, smarter warehouse environment.
Take the next step toward a safer and more efficient warehouse environment. Contact Element Logic today to explore how their state-of-the-art solutions can revolutionize your warehouse safety standards. Together, let’s build a future where safety and efficiency coexist seamlessly in the heart of your operations. Your team deserves it, and your success depends on it.