Types of Sortation Systems
Efficient and profitable warehouses limit the use of manual, time-consuming, and error-prone workflows.
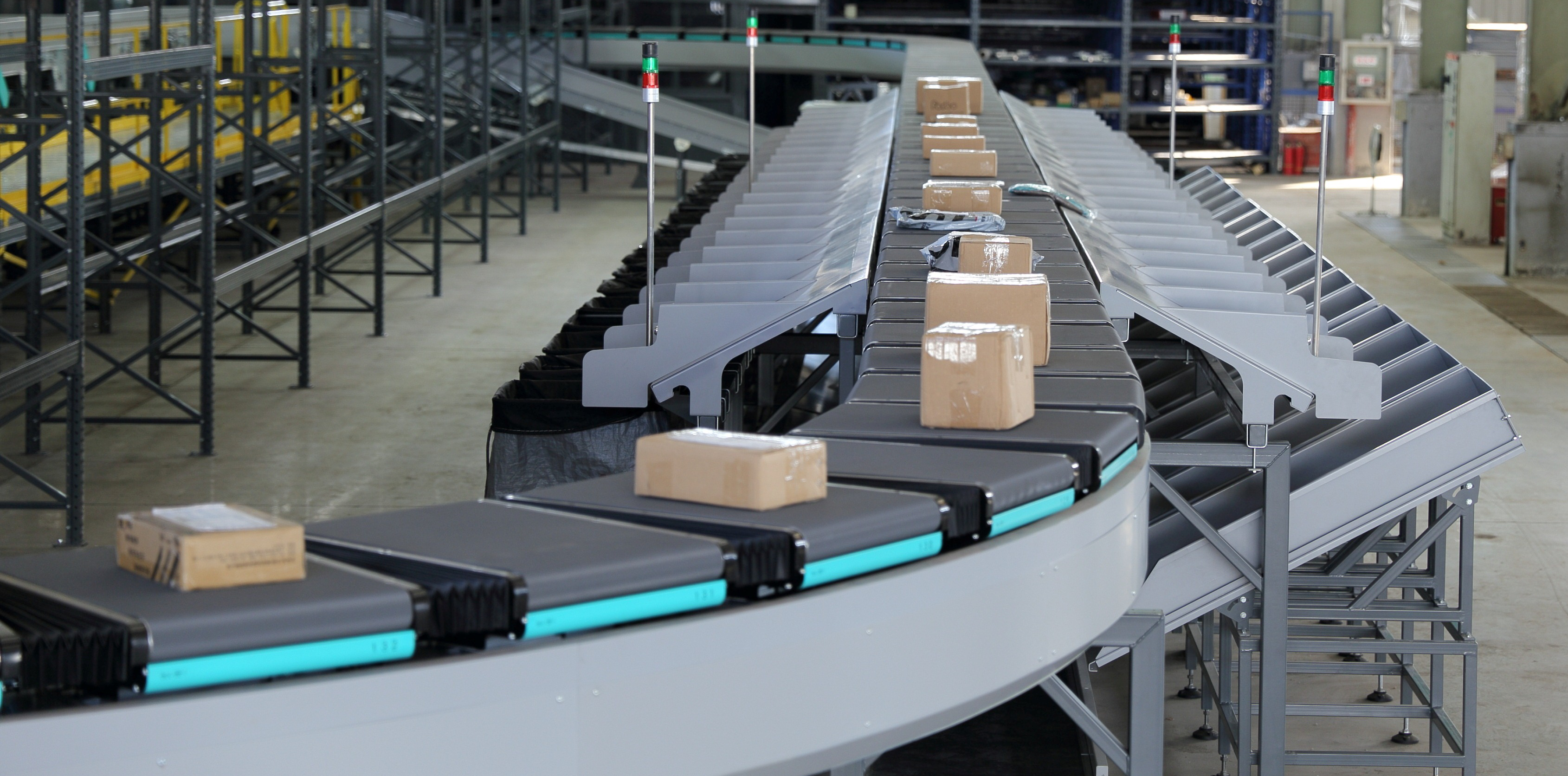
This includes the use of manual sortation processes that weaken warehouse operations by increasing the chance of inaccurate sorting, delayed orders, and upset customers.
The warehouse industry has come a long way from manual sorting, and there are several types of sortation systems that can be used to automate the sortation process. In this blog we will cover the different types of sortation systems, their benefits, and their applications, to help you select the best option for your unique warehouse needs. Let’s get started.
What is a Sortation System?
In warehouse management, a sortation system is a process that uses equipment to automatically identify, process, and divert items to the correct location within the warehouse. Sortation equipment often uses task-specific algorithms and codes to identify what these items are and where they need to go next. While warehouse sortation systems can vary widely based on product size, warehouse layout, and sortation speed, they are all able to automate the sorting process and improve accuracy, increase speed, and reduce costs.
Benefits of Automated Sortation Systems
Sortation systems are an essential part of modernizing your warehouse management, and they bring many top benefits associated with digital transformation. Some benefits include:
- Improving sorting efficiency
- Correcting inventory and order accuracy
- Increasing the speed of order processing
- Improving order fulfillment
- Streamlining warehouse operations
- Minimizing human errors
- Reducing labor costs
- Optimizing floor space
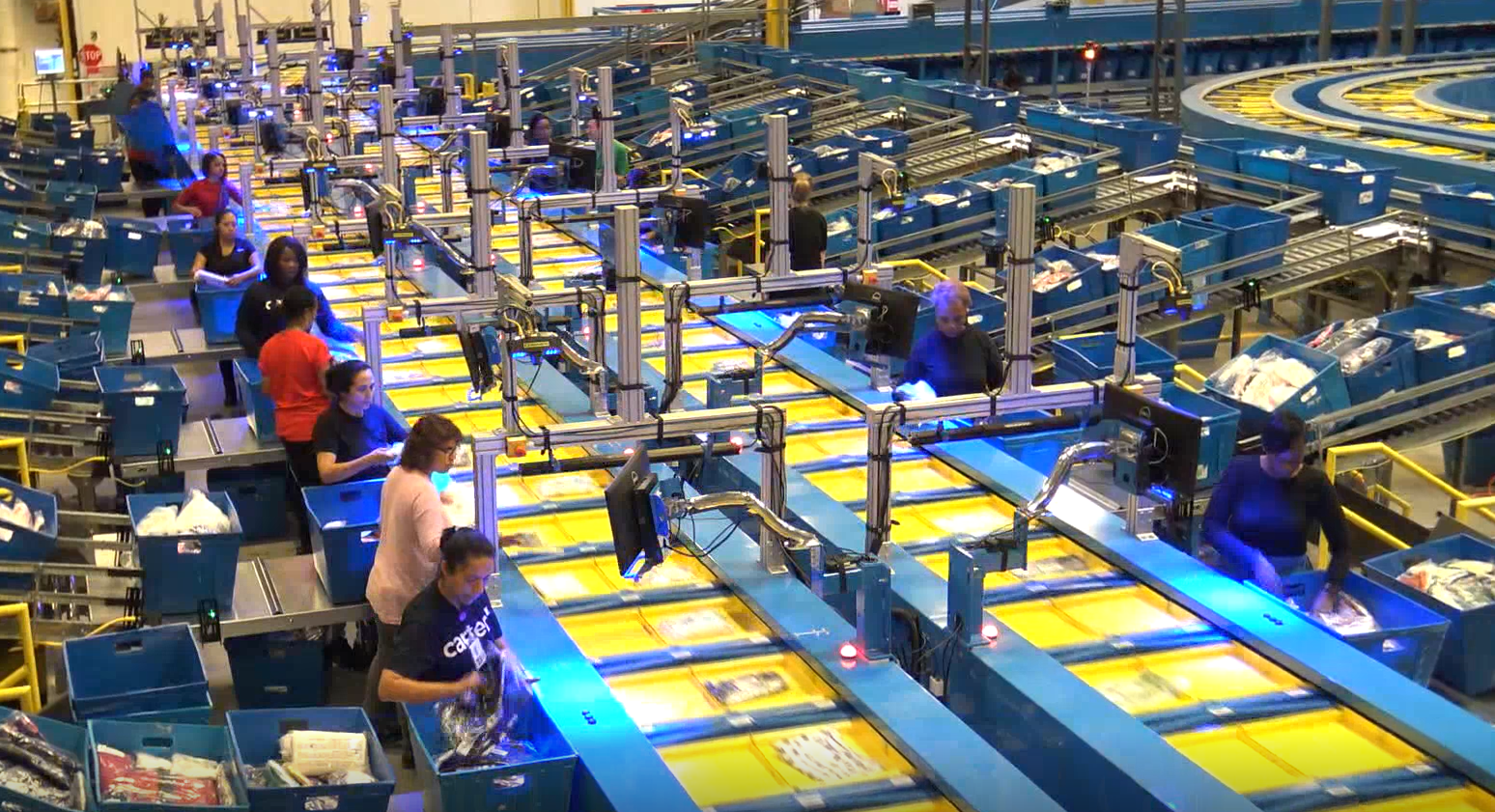
Learn More From our professionals
Sortation System by Application
Sortation systems can be used to help with various aspects of order fulfillment. For instance, there are sortation systems designed to automate receiving, picking and packing, and shipping.
1. Receiving
Leveraging an automated sortation system during the receiving process can help you better process your inventory as it enters the warehouse, increasing visibility into your inventory levels. Sortation systems can help with the following receiving applications.
- Return Processing: Return items can be identified and sent to specific stations designed to handle returns or exchanges based on your company’s protocols. Once the items are processed, the sortation system can automatically divert them to the appropriate station for destruction, put away, or used to fill an open order.
- Putaway: A receiving system can efficiently sort a high volume of product units or cases and transport them to the optimal location for storage.
- Cross Docking: Sortation systems can also be utilized to sort inbound items that are being unloaded and loaded directly into outbound delivery. The accurate intake and speedy reorganization of products increases the efficiency of these outbound deliveries.
When selecting sortation equipment for receiving in your warehouse, consider the number of inbound trailers that need to be unloaded and processed at the same time, as well as the total number of destinations needed for putaway or other processing. Identifying these parameters will help you select the best option for your warehouse.
2. Picking & Packing
Within order fulfillment, picking and packing are the most labor-intensive processes. When picking and packing are done manually, workers have to walk long distances throughout warehouses, manually pick items, bring them to the correct station, and pack them into orders for shipping. Warehouses are large facilities, and walking to and from inventory stations can be time-consuming. Not to mention, manually picking and packing orders is a slow and tedious process that can easily be messed up due to human error.
Sortation systems streamline picking and packing, managing more orders quickly and accurately. There are semi-automatic sortation systems designed to help workers facilitate picking and packing, as well as more advanced options that handle the majority of the picking and packing processes. The type of system you need depends on the size of your workforce, the number and type of packing stations required, as well as the case or palette sizes and weights. We’ll help you identify the best options later in the post.
3. Shipping
Sortation systems are a key driver of shipping efficiency, decreasing order turnaround time and improving customer satisfaction. An advanced sortation system enables orders to skip parcel hubs, which is known as zone skipping. That’s because sortation systems can presort groups of orders in an optimal format. This also allows for lower shipping costs and more orders to be processed within shorter timelines. Sortation systems can be used to presort orders in a variety of ways depending on the item size and weight, the volume of shipping, and the number of pallet build locations or trailers that will be used at the same time.
Now that you understand the applications of sortation equipment, let’s review the types of sortation systems that can be used for different types of inventory.
Case Sorters vs Unit Sorters
The distinction between a unit and a case is important when talking about sortation systems because they generally require different types of equipment. In warehouse management, an inventory unit is the language used to describe the smallest unit of an item. All other inventory measurements can be split into multiple parts, including a case. For example, a case is a box that contains numerous inventory units, and the size of the case can vary based on the unit size and logistics. Likewise, there is a case sorter that is designed to handle cases, and there is a unit sorter designed to manage individual units. The exception to this is when a hybrid model is used that can accommodate both units and cases.
Read on to learn specific examples of case sorters, unit sorters, and hybrid case and unit sorters.
Case Sorters
Case sorters are designed to receive, sort, and transport entire cases, cartons, or totes within a warehouse. Examples of case sorters include the following:
- Pop-Up Sorter: A Pop-Up Sorter consists of wheels or rollers emerging from a conveyor belt which pop up to transfer items to another downstream conveyor. This type of case sorter has medium to high throughput and can handle 40-100 cases per minute. Pop-up Sorters work well for packing applications.
- Shipping Carton Sorter: A Carton Sortation Conveyor is a belt-powered pop-up wheel conveyor with high throughput and can sort up to 100 cartons per minute. It automatically diverts cases to a specific destination and can also divert cartons to shipping doors.
- Pivoting Arm Sorter: A Pivoting Arm Sorter uses a series of paddles that divert and sort cases from a primary conveyor onto a secondary conveyor. It has medium to high throughput and can handle 50-100 cases per minute. A Pivoting Arm Sorter is commonly used for shipping applications.
- Pusher Sorter: A Pusher Sorter uses pneumatic pushers mounted to a conveyor belt. These pushers extend at specific angles to divert a case onto a secondary conveyor. This sorter has the lowest throughput and can process only 10-30 cartons a minute.
Unit Sorters
Unit sorters are designed to handle inventory units of varying sizes and shapes. Examples of unit sorters include the following:
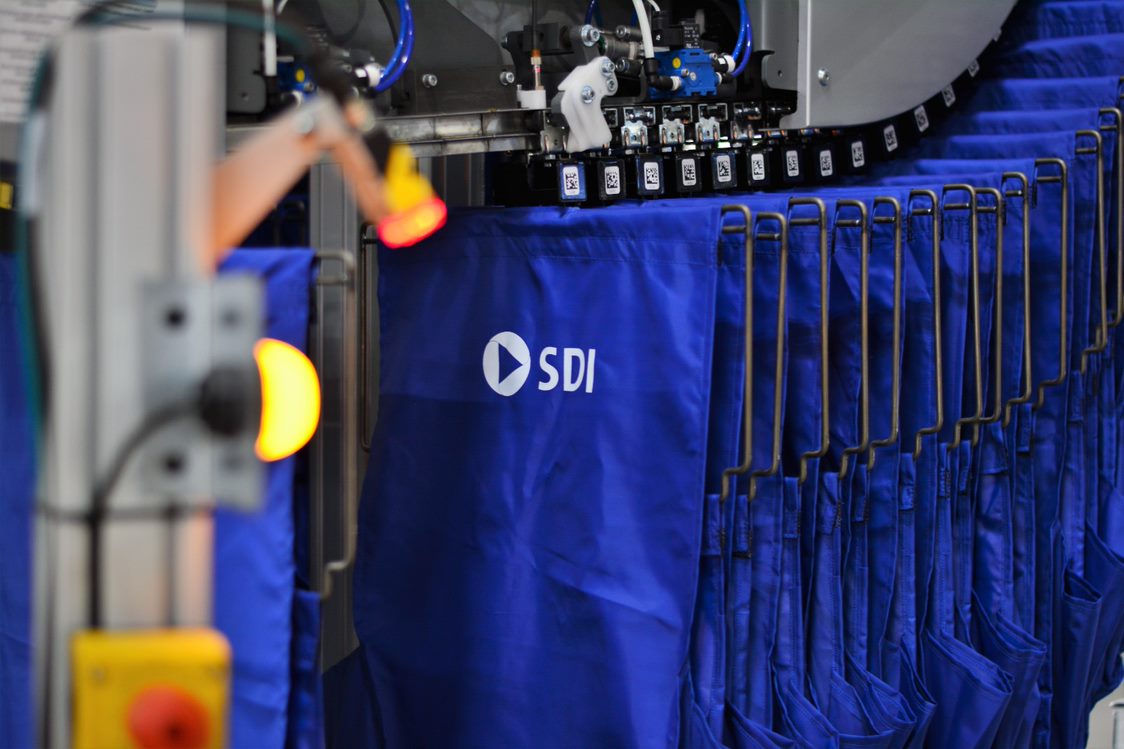
- Pouch Sorter: A JOEY Pouch Sorter uses flexible pouches to transport, sort, accumulate, and buffer an infinite variety of inventory units up to 22 lbs. Any shuttle on which each pouch hangs can be used as a garment hanger instead if needed.

- Bomb Bay-Style Sorter: The Sortrak G4 is an efficient Bomb Bay-Style Sorter with high throughput that can handle 18,720 trays per hour past a single point and make left and right turns. It uses a flexible chainless design made from steel, with numerous available configurations.

- Tilt Tray Sorter: A Tilt Tray Sorter has high throughput and is typically used by high-volume shippers and can be utilized for packing and shipping. The flexible system can handle a broad range of package mixes with multiple in-feed and induction areas. In-motion scales can also be incorporated into the automatic inducts to check parcel weights.
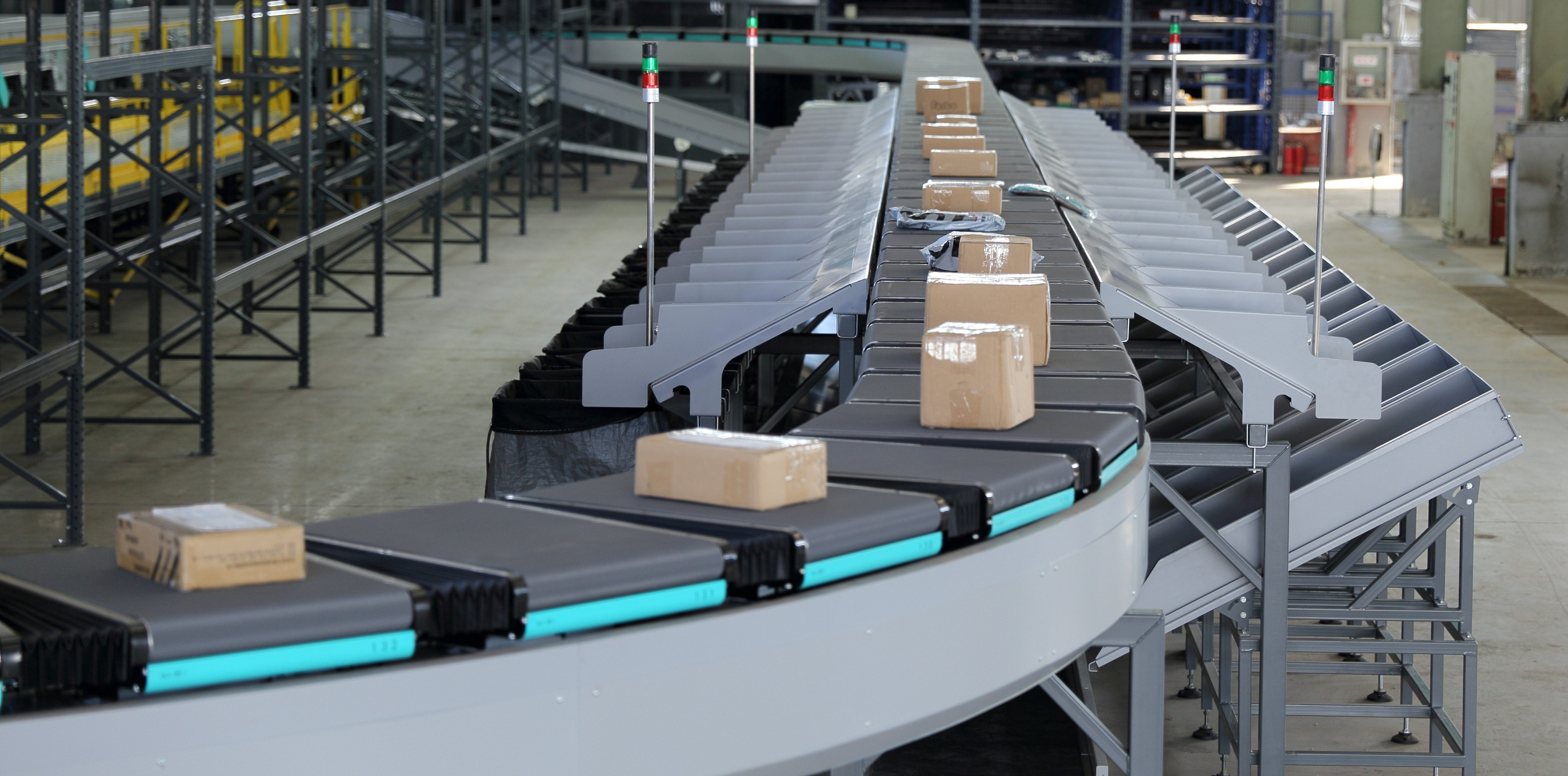
- Crossbelt Sorter: A Crossbelt Sorter also has high throughput and can sort up to 25,000 UPH and can be used for a wide range of items including apparel, parcels, accessories, and more. It uses an infeed system that can be fully automatic or semi-automatic to identify items and scan their measurements. The outfeed system temporarily stores the items and can be directly sorted into outfeeds such as chutes, bag racks, roll cages, and more.
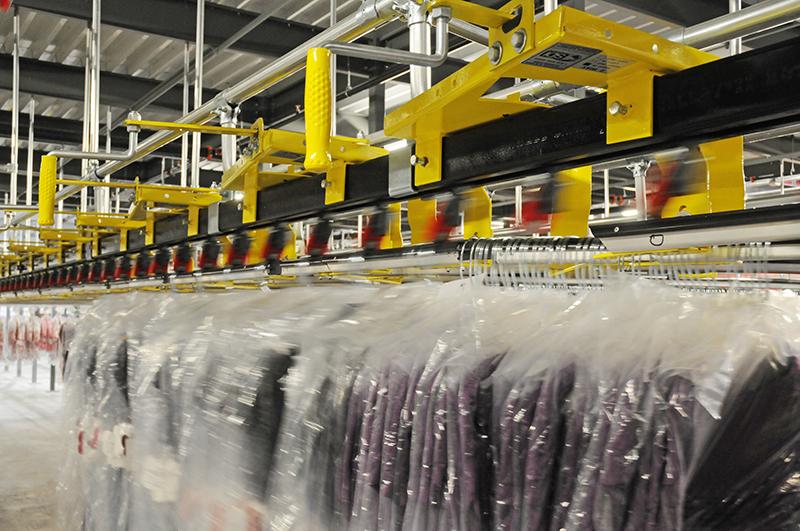
- Garment-on-Hanger (GOH): A Garment-on-Hanger (GOH) Sorter is the industry standard for high-speed unit distribution of hanging garments, and is capable of sorting up to 13,000 units per hour.
Case & Unit Sorter
- Narrow Belt Sorter: A Narrow Belt Sorter can be used for medium-sized items including both cases and inventory units. It has medium to high throughput capacity and can handle up to 120 cases per minute with 90 or 30-degree divert capability.
- Sliding Shoe Sorter: A Sliding Shoe Sorter has the ability to sort a wide variety of load mixes that vary in size, weight, and type, including both cases and units. It has high-speed sortation, handling over 200 cartons per minute.
If you’re still not sure which sortation system is the best match for your warehouse, review the sortations systems table below to help inform your decision.
Sortation Systems Table
Which Sortation System is Right for Your Warehouse?
When selecting the right sortation system for your warehouse, it’s important to consider your needs and parameters. Answering the following questions can help you identify your priorities so you can align them with the sortation systems in the market.
- What is your budget?
- What types of items do you need to sort? Are there any fragile items? Sizes and weight?
- At what speed do the items need to be sorted, what is your throughput?
- What’s your warehouse footprint? ?
- What materials are needed for the product packaging (bags, cartons, envelopes, etc.)?
- What type of application do you need help with (receiving, picking, packing, shipping, etc.)?
Investing in the Right Solution
Element Logic is an industry leader in automating warehouse management. Our expert consultants and systems integrators can help you design, build, integrate, and install a custom sortation system that is right for your warehouse.