Types of Conveyor Belts Used in Warehouse Automation
In the world of warehouse automation, conveyor belts play a crucial role in streamlining material handling processes.
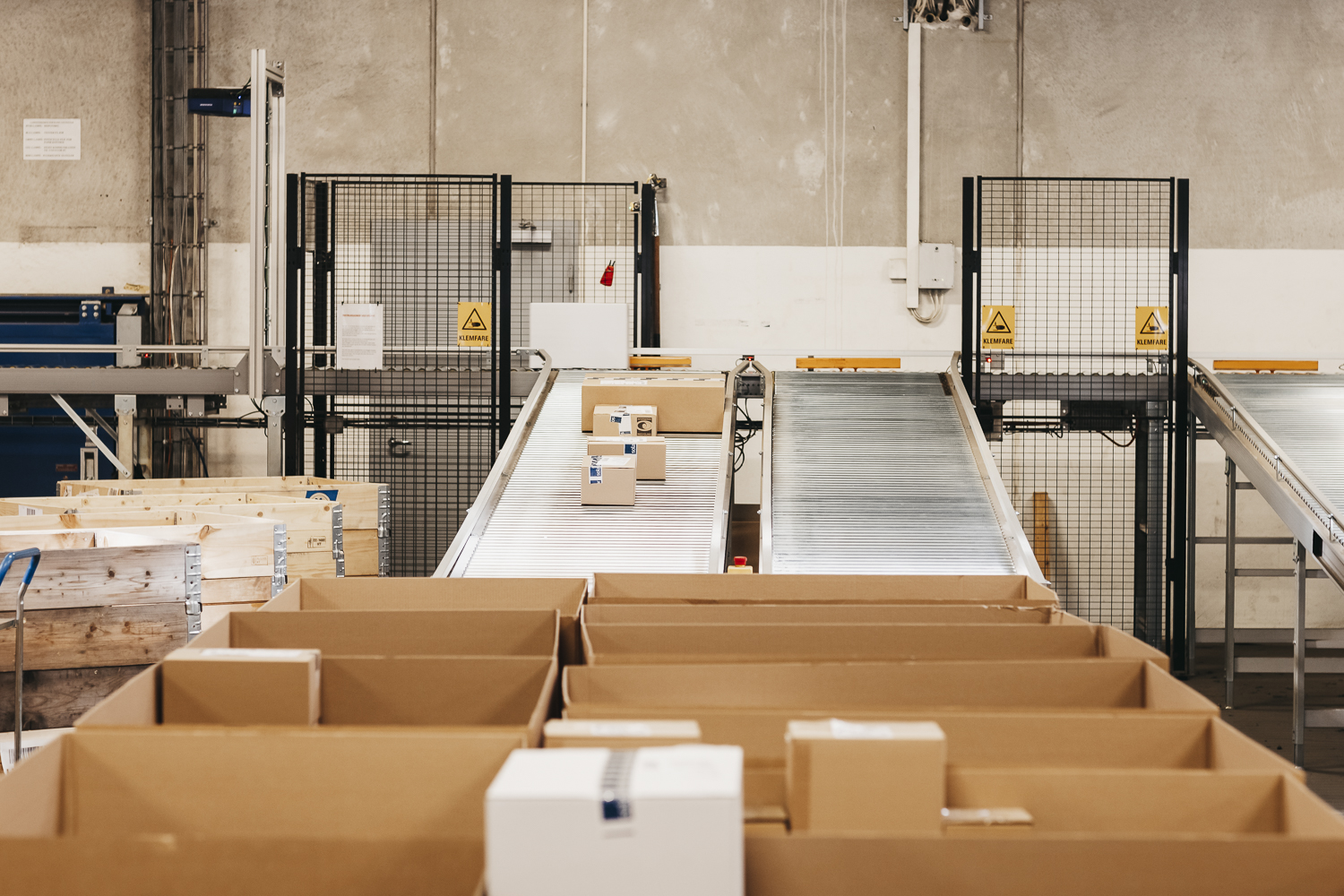
These automated systems, designed to move goods efficiently from one point to another, are integral to modern warehouses, where speed and precision are paramount. Conveyor belts eliminate the need for manual transportation of products, reducing labor costs and minimizing the risk of human error.
Conveyors have become essential for optimizing warehouse operations, especially as businesses aim to meet increasing consumer demands and tight delivery windows. By automating product movement, they ensure that items are transported swiftly and accurately, whether it’s moving products between workstations, feeding materials into automated machinery, or transporting packages to shipping stations.
The use of conveyor belts not only boosts speed and accuracy but also significantly enhances the overall efficiency of a warehouse. With minimal downtime and smooth material flow, businesses can scale operations seamlessly, improve throughput, and deliver faster order fulfillment—all while maintaining high levels of accuracy and reducing operational bottlenecks.
In this blog we will be reviewing the various types of conveyor belts used in warehouse automation, their benefits, and their key uses. Without further hesitation, let’s jump right in!
Modular Belt Conveyors
Modular belt conveyors are made up of a series of interlocking plastic modules that form a continuous belt. These modules are linked together, creating a robust and flexible conveyor surface. Unlike traditional flat belts, modular belts are constructed from individual segments, which allow for easy replacement of damaged sections and customization of the conveyor’s layout. The plastic material used is highly durable, providing excellent resistance to wear and tear in a variety of industrial environments.
Key Uses:
Modular belt conveyors are perfect for applications where flexibility and adaptability are critical. Their design allows them to handle products with irregular surfaces or shapes, making them suitable for industries such as food processing, packaging, and manufacturing. Additionally, these conveyors can navigate curves, inclines, and declines with ease, making them ideal for complex warehouse layouts where straight-line conveyors would be insufficient. They are also well-suited for handling products that need to be cooled, washed, or drained, as the open structure of the modules allows for air or liquid to pass through.
Advantages:
One of the key benefits of modular belt conveyors is their easy customizability. The modular design allows warehouse operators to quickly modify the conveyor’s configuration to meet specific operational requirements. This flexibility is crucial in environments where product sizes or conveyor paths frequently change. Additionally, modular belts are highly durable, with the plastic construction providing resistance to corrosion, chemicals, and high temperatures. Maintenance is also simplified, as damaged sections can be replaced without having to replace the entire belt, reducing downtime and saving on repair costs. Overall, modular belt conveyors offer a highly reliable, low-maintenance solution for versatile material handling needs.
Belt Conveyors
Belt conveyors are one of the most common types of conveyors used in warehouse automation. They consist of a flat, continuous belt, typically made of rubber, fabric, or other flexible materials, that is looped over pulleys. The belt is powered by motors, which drive the movement of materials along the conveyor. This system is known for its simplicity and ease of installation, making it a go-to solution for many warehousing applications.
Key Uses:
Belt conveyors are ideal for general material handling and are widely used to transport products between different points within a warehouse. Whether moving packages from one workstation to another, feeding goods into a sorting machine, or transporting items to a loading dock, belt conveyors provide a straightforward method of handling a variety of goods. They are particularly useful in applications requiring the movement of smaller, lighter items, as well as in environments where consistent, smooth transportation is essential.
Advantages:
The simplicity of belt conveyors makes them a reliable and cost-effective solution for warehouses. They are easy to maintain, with few moving parts, and can handle a range of load capacities, from light to moderate. Additionally, their straightforward design allows for quick installation and easy integration into existing automation systems. For operations looking for a versatile and affordable conveyor solution, belt conveyors offer a dependable option that can enhance the efficiency of material movement across a facility.
Roller Conveyors

Roller conveyors consist of a series of cylindrical rollers that are either powered by motors or rely on gravity to move items along the conveyor path. The rollers are typically arranged in parallel rows, allowing products to glide over them with minimal friction. Depending on the specific application, these conveyors can be designed as motorized, where the rollers are actively driven, or as gravity-fed systems, where the natural slope of the conveyor facilitates movement.
Key Uses:
Roller conveyors are ideal for transporting heavier goods or pallets, making them a popular choice in warehouse environments that handle bulkier items. They are commonly used in carton sorting systems, shipping areas, and pallet handling applications, where durability and the ability to transport high-capacity loads are crucial. Roller conveyors are also effective in applications where items need to be staged or accumulated temporarily before moving to the next phase of processing or shipping.
Advantages:
One of the main advantages of roller conveyors is their scalability for different load capacities. Whether handling light cartons or heavy pallets, roller conveyors can be customized to accommodate varying product weights. This versatility makes them suitable for a wide range of industries, from distribution centers to manufacturing plants. Additionally, roller conveyors are excellent for accumulating products along the line, allowing items to be queued or grouped without disrupting the flow of the operation. This ability to control product movement and accumulation adds flexibility to warehouse processes, especially in high-volume environments.
Incline/Decline Belt Conveyors
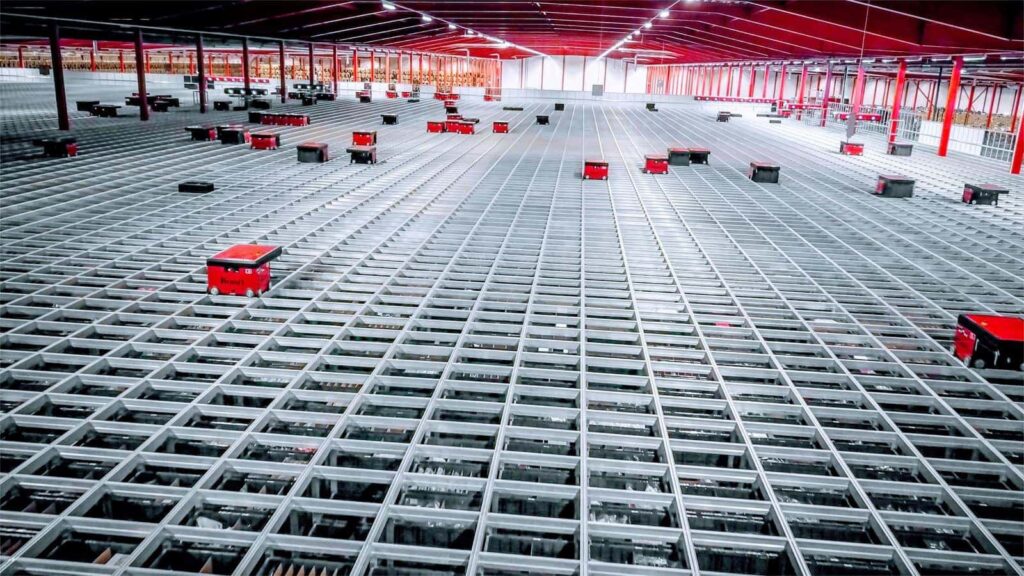
Incline and decline belt conveyors are specialized belts designed to carry products vertically, moving them between different floor levels within a warehouse. These conveyors feature angled belts that can transport items upward or downward along a slope. The belts are often equipped with cleats or textured surfaces to prevent products from sliding as they move along the incline or decline.
Key Uses:
Incline/decline belt conveyors are essential in multi-level warehouses where products need to be transported between floors. They are commonly used in distribution centers, manufacturing plants, and Automated Storage and Retrieval Systems (ASRS), allowing seamless movement of goods between different elevations. Whether moving products to a mezzanine level or bringing items down from an elevated storage area, these conveyors offer a reliable solution for vertical product transportation.
Advantages:
The primary advantage of incline/decline belt conveyors is their ability to save space. Instead of requiring ramps or lifts, these conveyors can transport products smoothly and efficiently at different angles, making them ideal for warehouses with limited floor space. Their ability to handle varying slopes while maintaining product stability ensures a smooth flow of goods, regardless of the incline. This versatility in vertical transportation helps warehouses maximize efficiency and optimize the use of space while maintaining a consistent flow of materials throughout the facility.
Pneumatic Conveyor Systems
Pneumatic conveyor systems use air pressure or vacuum to transport lightweight products through an enclosed pipeline. Instead of relying on belts or rollers, these systems utilize controlled air flow to move materials through tubes or ducts. By either pushing or pulling products through the system, pneumatic conveyors offer a contact-free way of handling goods, which makes them especially suited for transporting delicate or lightweight items.
Key Uses:
Pneumatic conveyor systems are commonly used in environments that handle small or delicate materials, such as powders, grains, and granular products. They are often found in industries like food processing, pharmaceuticals, and chemical manufacturing, where precision and cleanliness are paramount. These systems are particularly useful when transporting materials that need to be kept free from contamination or that require gentle handling to prevent damage.
Advantages:
One of the key advantages of pneumatic conveyor systems is their ability to move products vertically and horizontally over long distances with ease. Whether transporting materials between different floors or across large warehouse spaces, pneumatic conveyors offer flexibility and efficiency in moving products without the need for extensive mechanical parts. Their enclosed nature ensures that the transported materials are protected from external contaminants and remain clean throughout the process. Additionally, pneumatic systems can navigate complex warehouse layouts, including tight spaces, making them a highly adaptable solution for warehouses with specific spatial or material-handling needs.
Magnetic Belt Conveyors
Magnetic belt conveyors are specialized systems that use powerful magnets embedded beneath the belt surface to hold and move ferrous (iron-containing) materials. The magnetic force securely holds metal items against the moving belt, allowing for smooth transportation along the conveyor path. This unique feature makes them highly effective for applications where precise handling and control of metal products are essential.
Key Uses:
Magnetic belt conveyors are particularly useful in environments where metal components are frequently handled, such as in the automotive, manufacturing, and recycling industries. They are commonly employed to transport metal parts, scrap materials, or assemblies, ensuring that these items stay securely in place even when moving at high speeds or across inclines and declines. In recycling operations, these conveyors are ideal for sorting and separating ferrous metals from other materials.
Advantages:
The primary advantage of magnetic belt conveyors is their ability to provide secure handling of metal parts, significantly reducing the risk of product spillage or misalignment during transportation. This ensures a more controlled and efficient flow of materials, especially in environments where metal items need to be moved quickly or precisely positioned. Additionally, the magnetic force allows for smooth and continuous movement, making these conveyors well-suited for automated processes that demand consistent product control. By minimizing product loss and improving handling precision, magnetic belt conveyors enhance overall operational efficiency and safety.
Cleated Belt Conveyors
Cleated belt conveyors feature belts with vertical cleats or ridges that are strategically spaced along the belt’s surface. These cleats are designed to provide additional grip, preventing products from slipping or shifting during transportation. The cleats create partitions on the belt, allowing it to carry items securely, especially when moving products up or down an incline or decline.
Key Uses:
Cleated belt conveyors are ideal for transporting products in environments where there is a risk of slippage, particularly on steep inclines or declines. They are commonly used in industries such as food processing, agriculture, and manufacturing, where items need to be moved uphill or downhill without shifting. Cleated belts are especially effective for carrying loose or irregularly shaped products, such as bulk materials, small parts, or packages, ensuring that they stay securely in place during transit.
Advantages:
The main advantage of cleated belt conveyors is their ability to ensure stable and secure product movement on steep gradients. The vertical cleats provide additional support, preventing products from sliding back or piling up, even when the belt is operating at sharp angles. This stability is crucial for maintaining the efficiency of operations, especially in high-throughput environments where product slippage could lead to delays or damage. Additionally, cleated belt conveyors offer a reliable and efficient solution for transporting materials over longer distances with elevation changes, making them an essential tool for handling challenging warehouse layouts.
Chain Conveyors
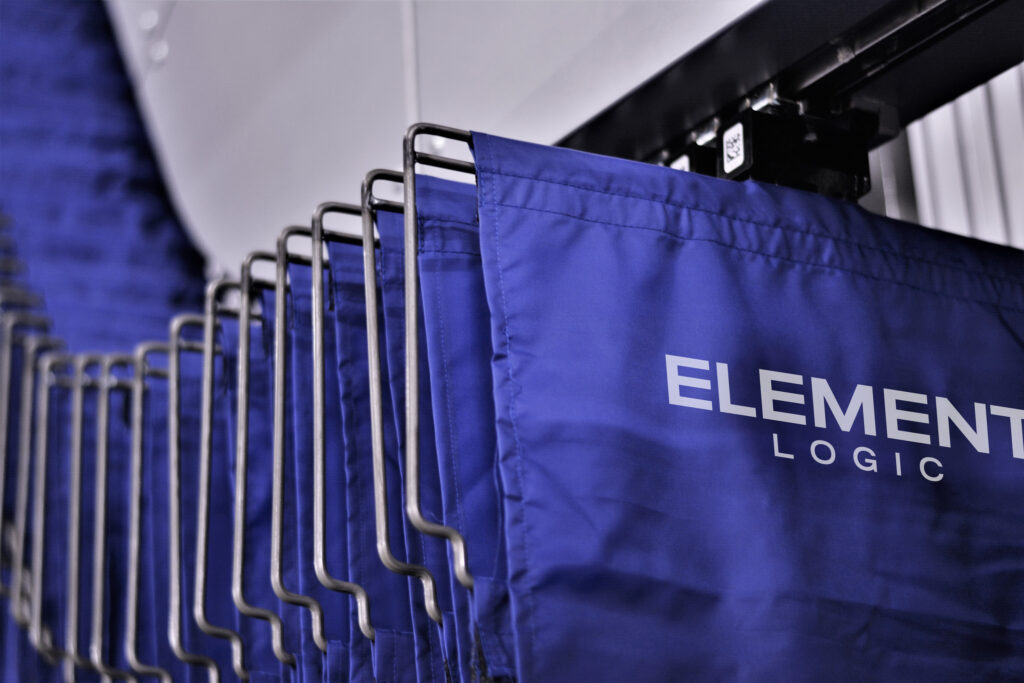
Chain conveyors are composed of a series of interconnected chain links that form a continuous loop, designed to move items along a set path. These chains are powered by motors and are often installed in a rigid framework, which supports the heavy loads they are designed to transport. Chain conveyors are typically made from strong materials like steel, making them well-suited for rugged and heavy-duty operations.
Key Uses:
Chain conveyors are commonly used in industries that handle large, bulky, or heavy items, such as pallets, containers, or machinery parts. They are particularly popular in manufacturing, automotive, and distribution environments where materials need to be moved steadily across production lines or between storage and shipping areas. Chain conveyors are ideal for heavy-duty operations, including transporting large metal parts or equipment and supporting automated systems where high-load capacities are required.
Advantages:
The main advantage of chain conveyors is their high durability and capacity to handle heavy loads with ease. Designed to withstand the wear and tear of industrial environments, chain conveyors are well-suited for transporting high-load items over long distances or through complex systems. Their robust construction ensures longevity, making them an excellent investment for warehouses or manufacturing facilities that require reliable material handling for bulky items. Additionally, their ability to move products of varying sizes and weights, without compromising on speed or precision, enhances their versatility across different industries.
Overhead Conveyor Belts
Overhead conveyor belts are systems mounted above the floor, designed with hooks, carriers, or trolleys to move products along an overhead track. These conveyors allow items to be transported across the warehouse without taking up floor space, as the products are suspended and carried through the system. Overhead conveyors can handle a wide variety of products, including those that are large, bulky, or awkwardly shaped.
Key Uses:
Overhead conveyors are ideal for environments where floor space is limited or must be optimized for other operations. They are commonly used to transport hanging items such as garments in apparel warehouses or large parts in automotive and manufacturing industries. These systems are particularly useful for handling large or irregularly shaped items that might be difficult to move with traditional conveyor belts. By moving items overhead, the warehouse floor remains clear for other critical processes like picking, packing, and equipment operation.
Advantages:
The biggest advantage of overhead conveyor belts is their ability to free up valuable floor space, which is crucial in high-density warehouse environments. By utilizing vertical space, overhead conveyors can significantly improve warehouse efficiency and allow for more productive use of floor areas. Additionally, these conveyors can be easily integrated into complex warehouse layouts, adapting to multiple levels, turns, or inclines, making them a versatile solution for warehouses with tight spaces or intricate designs. This not only improves the flow of goods but also helps optimize storage and operational efficiency.
Conclusion
Conveyor belts play a vital role in modern warehouse automation, offering diverse solutions to meet the unique needs of various industries. From simple belt conveyors to more specialized options like modular, roller, and overhead systems, each type serves a specific purpose, enhancing the efficiency and speed of material handling processes. By choosing the right conveyor system, warehouses can optimize their operations, reduce labor costs, and improve accuracy in product movement.
Selecting the appropriate conveyor belt depends on factors like product type, load capacity, and warehouse layout. Whether it’s transporting light packages with belt conveyors or handling heavy pallets with chain conveyors, these systems provide the versatility, durability, and scalability necessary to meet the evolving demands of today’s fast-paced environments. With the right conveyor technology in place, businesses can enhance productivity, streamline workflows, and ultimately boost their bottom line.