Types of Automated Storage and Retrieval Systems (ASRS)
With several different purposes, types, and price points of warehouse management systems, it can be difficult to understand which option is best for your particular needs.
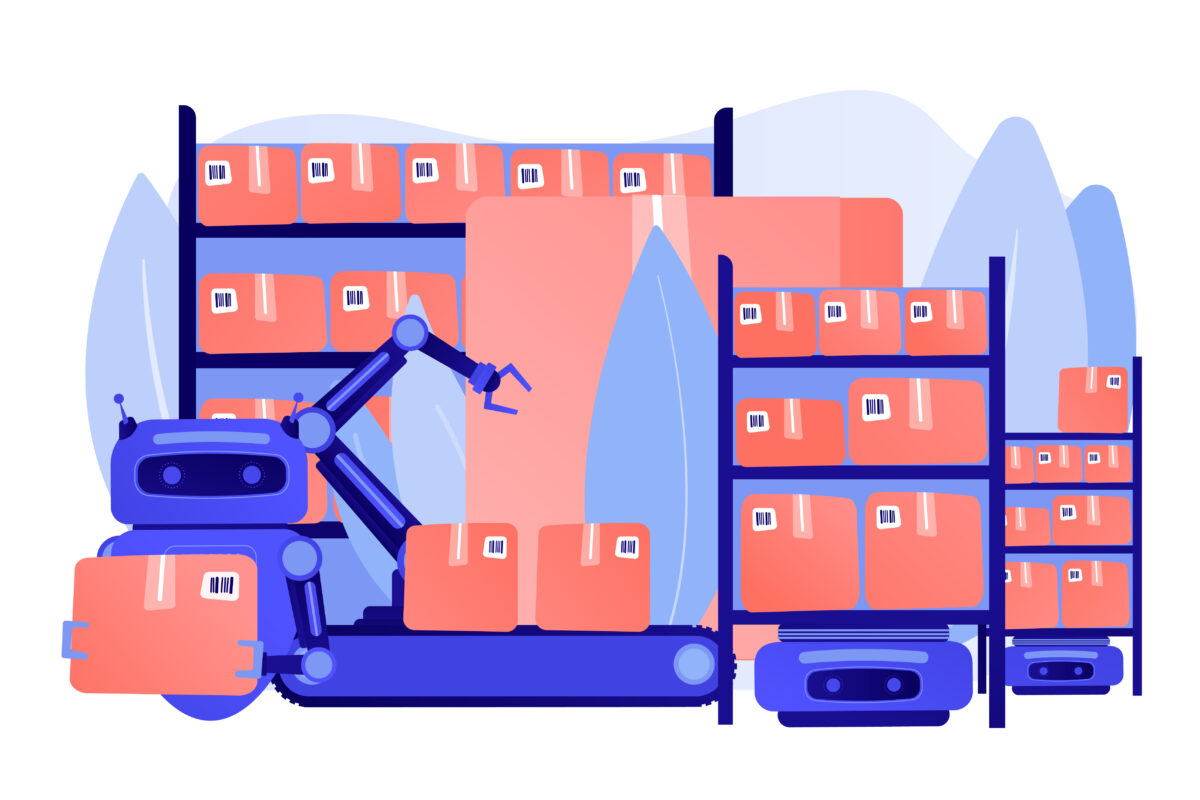
Investing in the right solution is an important financial decision, helping you better serve your customers and maximize profits. In this blog, we’ll cover the basics of an automated storage and retrieval system, its benefits, and review the different types available on the market.
What is an ASRS?
An automated storage and retrieval system (ASRS) is a material handling system used to streamline goods-to-person workflows in a warehouse or distribution center (DC). The system is composed of hardware, software, and controls that automatically store, retrieve, and manage inventory. An ASRS is commonly used in industries such as eCommerce, B2B wholesale, retail, logistics, and more.
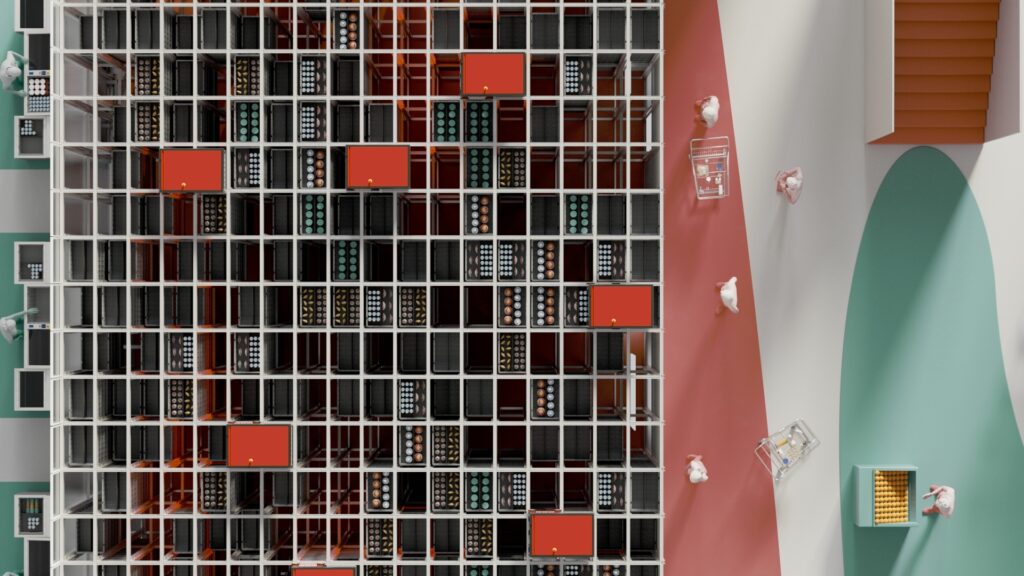
Benefits of an ASRS system
Using an ASRS system helps companies embrace digital transformation, bringing several benefits related to the modernization of warehouse management.
Increase Efficiency
Manual order fulfillment methods involve time-consuming picking, and packing, sorting, and inventory management. Warehouse workers must pick and replenish in parallel, slowing down order fulfillment and opening up the risk of errors. By automating aspects of order fulfillment, an ASRS system reduces the risk of inventory and order errors while increasing the speed with which orders can be processed and delivered to customers. Further, using an ASRS system enables companies to reduce labor costs all while improving efficiency.
Optimize Space
Warehouses are typically expensive to rent, and therefore space is extremely valuable. When manual workflows are being utilized, workers must be able to walk the floor aisles and access inventory as necessary. With an ASRS system, inventory can be stored in vertical spaces that were previously inaccessible. In addition, aisles and floor space are not necessarily used for pedestrian traffic, freeing up space for additional inventory or equipment. This optimizes your warehouse space, maximizing your real estate investment.
Warehouses are typically expensive to rent, and therefore space is extremely valuable. When manual workflows are being utilized, workers must be able to walk the floor aisles and access inventory as necessary. With an ASRS system, inventory can be stored in vertical spaces that were previously inaccessible. In addition, aisles and floor space are not necessarily used for pedestrian traffic, freeing up space for additional inventory or equipment. This optimizes your warehouse space, maximizing your real estate investment.
Improve Inventory Management
Maintaining accurate and up-to-date inventory is critical to satisfying customers and turning profits. However, when warehouse workers are responsible for manually updating inventory records several times a day, there’s a high risk of inaccuracies and low visibility into real-time inventory data. By using an ASRS system, businesses can digitally review inventory in real time, and instead of relying on manual entries, inventory numbers get updated automatically. This reduces the risk of errors as well as accidentally understocking or overstocking.

Advance Safety
Warehouses can be dangerous for employees, especially new ones. For instance, 37% of workplace injuries happen during the first year of an employee’s job, with 27% resulting from overexertion, 22% due to slips, trips, and falls, 14% from being struck by an object, and 6% from being caught in between objects. Minimizing these types of activities can help improve workplace safety. Likewise, using an ASRS system reduces the need for workers to handle heavy or hazardous materials, while also limiting their exposure to slipping on the warehouse floor, being struck by falling inventory, or getting stuck between objects.
Enhance Cost Savings
Through a waterfall effect, businesses get a better return on investment (ROI) by increasing efficiency, optimizing storage space, reducing labor costs, improving inventory management, and enhancing safety. Instead of wasting money on redundant, time-consuming, error-prone, and potentially dangerous tasks, companies can satisfy customers and turn profits.
Embrace Sustainability
As large facilities, warehouses can consume significant amounts of energy and resources. Utilizing an ASRS system helps reduce this footprint. The technology does not require lighting, the machines are energy efficient, and the inventory is stackable and accurate.
To learn more about the benefits of an ASRS system, read our blog post on The Benefits of Automating Your Warehouse with AutoStore.
Types of Automated Storage and Retrieval Systems
Now that you understand the benefits of using an ASRS system, let’s dive into the different types of systems available.
Vertical Lift Module (VLM)
A Vertical Lift Model is composed of vertically arranged trays accessed by an automated lift. Moving up and down, the lift automatically retrieves the correct inventory items. The VLM can be customized to store different-sized items, from small parts to larger items like tools and machinery.
Automated Guided Vehicle (AGV)
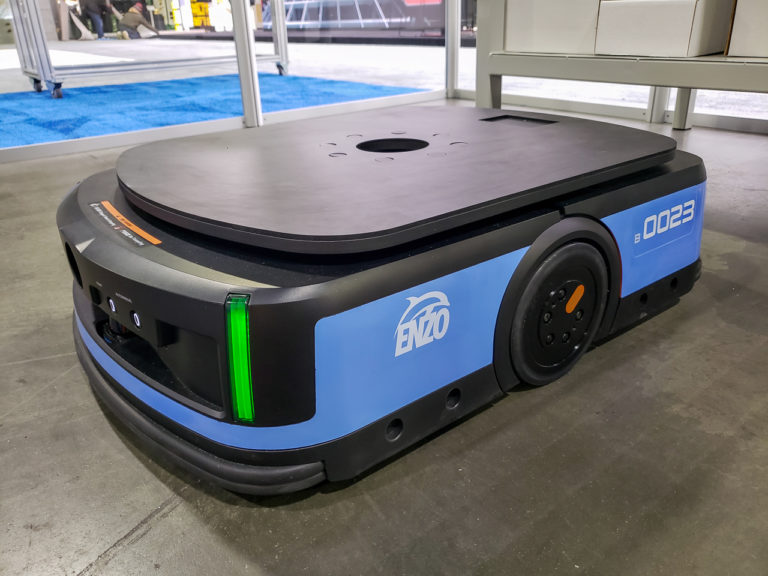
Automated guided vehicles are robots that travel across the warehouse floor. The AGV exclusively follows a fixed path on the floor to transport inventory items to and from the designated locations. They are unable to travel outside of these identified paths on the warehouse floor.
Horizontal Carousel
A horizontal carousel is a series of circular shelves that rotate horizontally on a track. Typically, the shelves are divided into compartments that are customized to hold a variety of items. This system is high-speed and excels at picking small inventory items.
Vertical Carousel
Similar to a horizontal carousel, a vertical carousel has rotating shelves, but they rotate vertically up and down on a track. This is a great option when high-density storage is required due to limited floor space.
Mini-Load ASRS
A mini-load ASRS is ideal for small-to-medium-sized items. This system uses cranes that automatically move along a track installed in the warehouse to retrieve and store items in inventory bins.
Autonomous Mobile Robots (AMR)
Autonomous mobile robots are similar to AGV, but they do not need pre-defined paths. Instead, AMR is intelligent enough to move independently throughout the warehouse, retrieving and transporting inventory items as needed.
Robotic Cube Storage ASRS
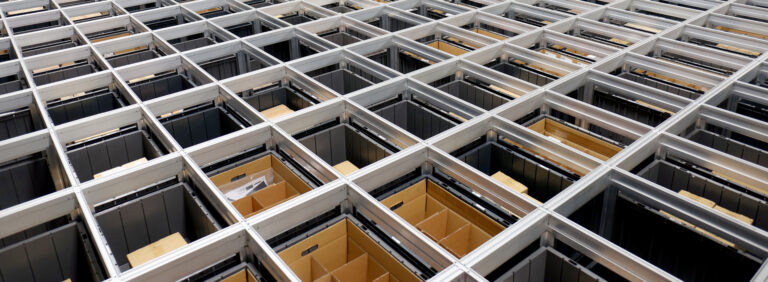
Robotic cube storage is the most advanced type of ASRS. It is a system that uses robots to glide atop a custom grid, with inventory cubes stacked along the edges. The robots sort and retrieve inventory cubes and deliver them to specific ports for order picking. When the robots are not in use they charge themselves for future tasks. The AutoStore ASRS system is the best cube storage solution, with proven success in strengthening supply chain management and maximizing ROI.
Key Takeaways
With a variety of ASRS systems on the market, businesses have several options to best service their customers and meet their needs. SDI Element Logic helps companies optimize their warehouse management and scale with customers’ demands. With the growth of e-commerce and other fulfillment applications, automated storage and retrieval systems will continue to become important in securing a competitive edge.
Explore the advanced AutoStore automated storage and retrieval system.