Semi-Automated vs Fully-Automated Each Picking Solutions
Robotic each picking is revolutionizing the way warehouses operate. With the rapid pace of technological advancements in the field of robotic each picking, coupled with the growing popularity of good-to-person systems like AutoStore, the dream of achieving fully automated warehouses is closer than ever before.
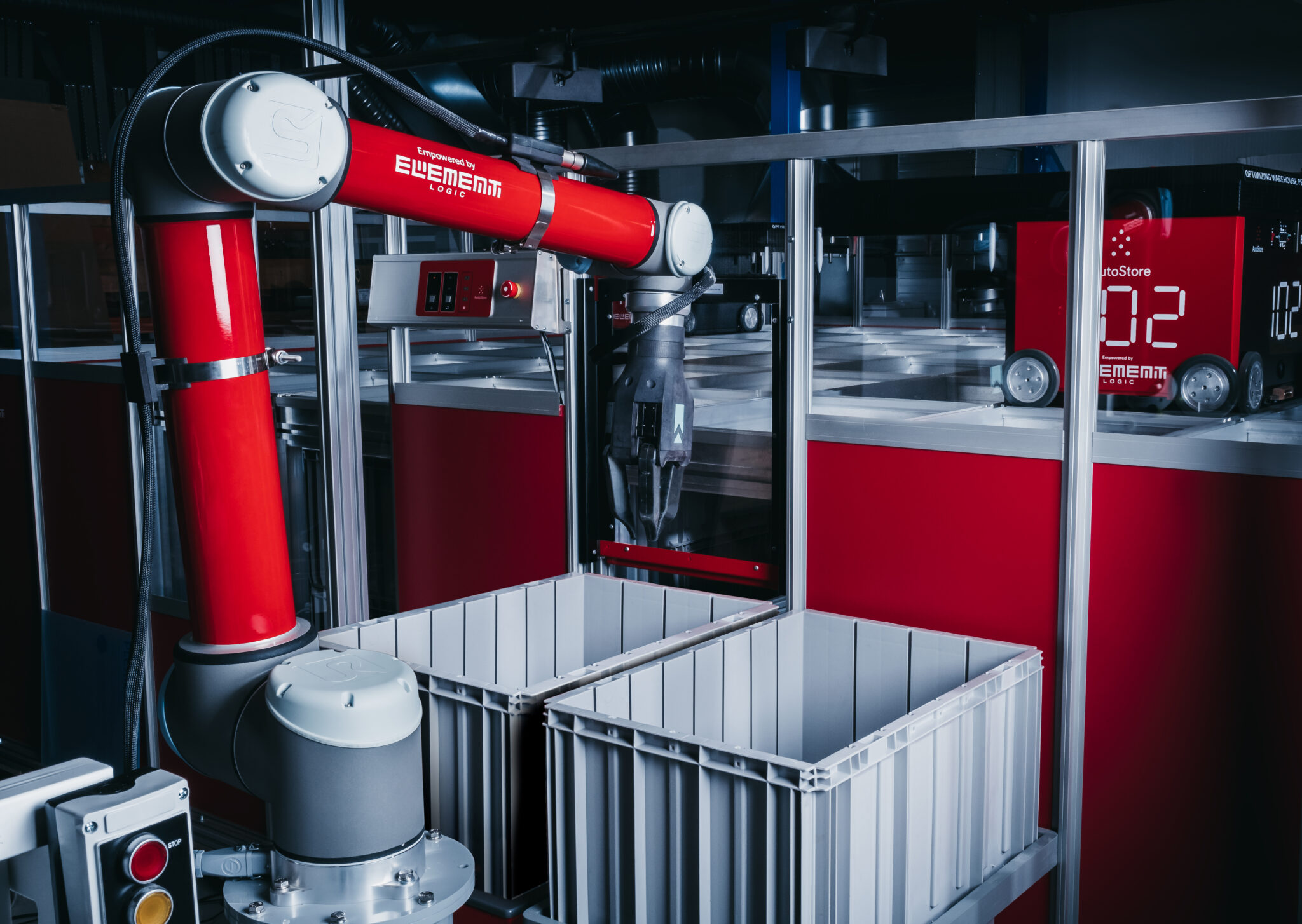
By Aaron Lininger
It is now only a matter of time before this vision becomes a reality soon. Several key players have emerged in the robotic picking space, and each is taking a mostly similar approach to the problem of picking and placing a high assortment of products, with some very important subtle differences. How far your organization wants to go with automation is a key question to understand when laying out the path ahead.
Am I Ready for Robotic Each Picking?
While the idea of simply filling open positions in the warehouse with robots instead of humans sounds like a great idea, it’s just not that simple. The process that you have in place (or plan to put in place) needs to have some very specific attributes to take advantage of the technology currently available. Here’s a quick checklist to help you assess if you are ready:

- Predictable means of presenting needed inventory to a stationary position
- Process that presents destination totes or cartons in the proximity of a 6-axis robot (or a system that adds the 7th axis)
- Automated means of delivering the desired work instruction from the WES to each picking system
- End-effector(s) that can grasp your products (at least a healthy majority of them) and move them securely over a short distance
- Automated means of cycling both the inventory carrier or tote and the destination tote to maintain a continuous flow
- Solution provider that has a trajectory towards picking more items faster
Goods-to-person systems, like AutoStore, alone help you to check a few of the boxes, but selecting an automation provider that is familiar with integrating other warehouse automation technology in combination with robotic picking arms is critical to a successful project.
Robotic Each Picking 101
The introduction of 6-axis robotic picking has led to the introduction of some new ways to articulate the productivity and throughput of an individual workstation. The more traditional method of calculating the productivity of a human manning a particular workstation is a basic equation – how many units an individual picks divided by how much time they spent picking. Any solid warehouse manager in an operation can rattle these types of statistics off the tip of their tongue and the majority of continuous improvement efforts are measured by how much they improve the process units per hour (UPH).
The process UPH includes elements outside of the employee control, including the bin or tote exchange time of a goods-to-person system. Using this traditional method makes it easy for warehouse management to predict the output of a system but taking the # of stations x the ‘per station’ UPH x the hours of operation.
When robotic each picking providers started to enter the market, they believed a new definition of ‘units per hour’ applied to them. Since they are responsible for just the grasping, movement, and placement of items, they felt that measuring this portion of the process exclusively would be the fairest way to represent their technology (doesn’t hurt that it makes the numbers sound better to your typical warehouse leader).
Using this new method, to get an apples-to-apples comparison to the human counterpart, you need to add back in the bin exchange time plus any time that the station is starved of tasks and compare the productivity to understand if you are getting a net gain or loss of system throughput by introducing picking robots.
Throughput of Robotic Picking vs Human Workers

For example, let’s take a goods-to-person station layout similar to the one afforded by the AutoStore system. We have a system that delivers a 4-second bin exchange time, and a process where it takes a human operator 3.5 seconds to pick and place the goods and trigger the cycle to the next bin, and our units picked per bin presentation is 1.
Measuring this the way a robotic each picking company would capture this – the human is picking at a productivity of 1028 UPH (3600/3.5), but the full process yields a productivity of 480 UPH (3600/7.5). Many each picking providers are advertising pick rates > 500 UPH (~7-second pick time), but you need to keep in mind that this is to be compared to the 1028 figure, and not the 480 figure and the net resulting traditional UPH will be 321 UPH.
In all fairness, the robotic system doesn’t need to take breaks and lunches, so the per-shift output doesn’t have as significant of a gap (human station output = 480 x 7.25 = 3,480 units picked per shift vs. robotic station output = 321 x 8.5 = 2,732 units picked per shift). If you intend to staff all picking stations with robots, it’s key to incorporate these figures into your design to account for an adequate number of stations to support the overall throughput requirement.
Semi-Automated vs Fully Automated Robotic Each Picking Solutions
Once you’ve reached the point where you believe you are ready to move forward with robotic each picking, you have some choices to make in terms of how far you want to go with the automation. There are providers out there that can deploy each picking robot in 1-day with no integration and no upfront cost, which can be a very nice offer for a warehouse with immediate staffing challenges and complicated systems that are challenging and expensive to integrate with.
They can achieve no integration by scraping the pick instruction from the HMI present at the station, and combine this with vision systems, a 6-axis robot with a range of end effectors, and an alert system, letting a human operator responsible for manning a bank of stations, when a pick exception has occurred so they can intervene and keep the station processing.
This type of process is often referred to as ‘semi-automated’ because a human operator needs to be present at all times to maintain system flow. This type of system is economically viable, and the upfront capital cost can be bypassed by agreeing to a ‘per pick’ rate that is slightly better than the human per pick cost doing the same process. Alternatively, some automation integrators have partnered with robotic companies to develop ‘fully integrated and fully automated’ picking solutions.
For example, Element Logic has strategically partnered with Righthand Robotics to deploy a WES module called ‘eOperator’, that not only manages the integration component between the AutoStore system and the Righthand Robotics picking system but also is integrated with eManager, the warehouse execution system managing the flow and release of orders through the fulfillment center. Having this integration enables both systems to be aware of when pick exceptions occur, giving the WES system the ability to ‘flag’ orders with known mis-picks for further QC inspection. This functionality is key to having what I consider a ‘fully automated’ each picking solution.

In theory, with this capability, warehousing staff could go home in the evening, allow the robotic systems (AutoStore & eOperator) to continue processing through the night, and come in the next day only to deal with any exceptions. Additionally, these systems are available for purchase, so there is a quantifiable ROI and one that can be reached quite rapidly in circumstances of a 2-3 shift, 7-day operation.
Conclusion
Robotic each picking is a powerful tool that can help warehouses improve efficiency, accuracy, and productivity. With many options to choose from, not only just with each picking robotic companies, but also the larger goods-to-person market of automation solutions, key stakeholders must understand each of the key differentiating features of the technology with both benefit and potentially limit capabilities going forward.
Choosing the right automation provider is critical for optimizing your warehouse operations. To succeed in this endeavor, it’s important to select a provider who is willing to be a genuine partner, with a high degree of transparency, candor, and a willingness to understand your unique challenges and goals. With a provider who possesses these qualities, you can increase your chances of success in your pursuit of optimized warehouse operations.
If you are searching for a provider that is capable of elevating your warehouse operations, we would love to speak with you. Visit the link here to get your journey started!