Essential Warehouse Automation Technologies
In today’s fast-paced and highly competitive market, warehouses have become the nerve centers of supply chains, responsible for ensuring that goods are stored, processed, and delivered with speed and precision.
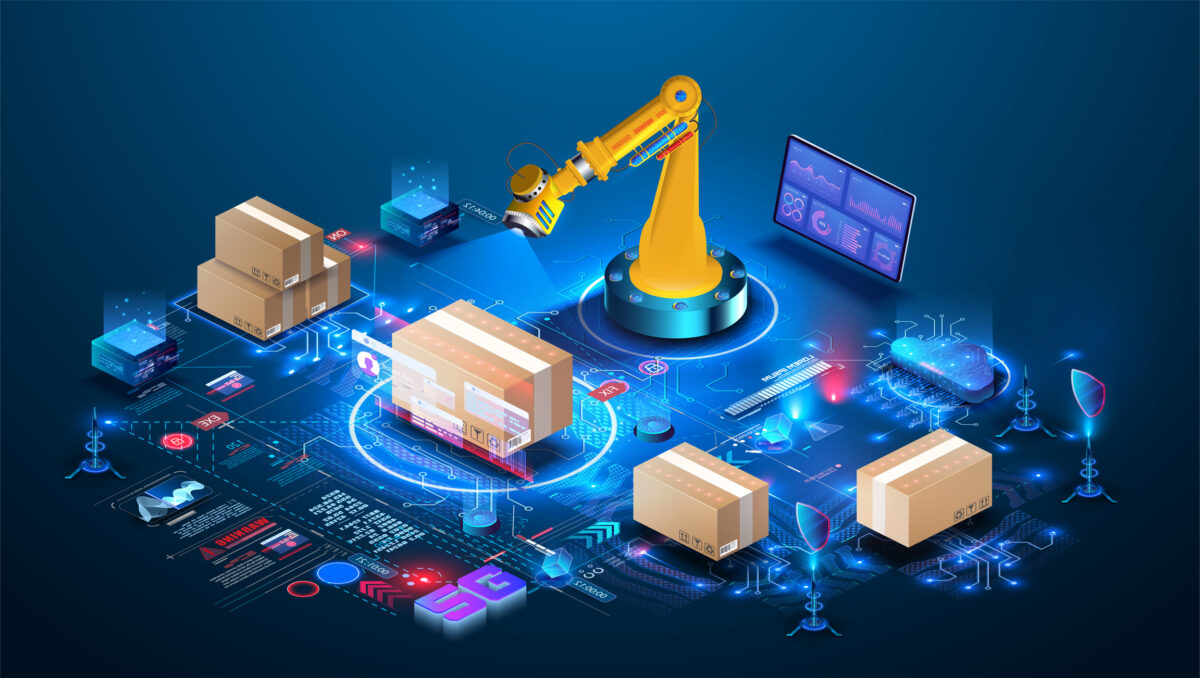
As consumer demands for faster deliveries and higher service levels continue to rise, the pressure on warehouses to operate efficiently has never been greater. This is where warehouse automation steps in, offering a transformative solution that not only meets these demands but also propels businesses toward greater operational excellence.
Warehouse automation refers to the use of technology and automated systems to perform tasks that were traditionally done by manual labor. From the automated movement of goods to sophisticated inventory management systems, these technologies are revolutionizing how warehouses function. The importance of automation in modern warehousing cannot be overstated. By integrating automation, warehouses can significantly enhance efficiency, reduce operational costs, and improve the accuracy of critical processes such as order picking, inventory management, and shipping.
One of the key advantages of warehouse automation is its ability to streamline operations, allowing for faster and more reliable processing of orders. Automated systems reduce the likelihood of human error, ensuring that tasks are completed with consistent accuracy. This not only boosts productivity but also enhances customer satisfaction by minimizing delays and errors in order fulfillment. Additionally, automation helps in optimizing space utilization, reducing the need for large, labor-intensive operations, and enabling warehouses to handle higher volumes of goods within the same footprint.
In essence, warehouse automation is not just a trend—it’s a strategic necessity for businesses aiming to remain competitive in the modern marketplace. By embracing automation, companies can achieve significant cost savings, improve accuracy, and ultimately deliver a better experience for their customers. As we explore the essential warehouse automation technologies in this blog, it becomes clear that the future of warehousing lies in the seamless integration of these advanced systems.
Automated Storage and Retrieval Systems
Automated Storage and Retrieval Systems (ASRS) are highly advanced, computer-controlled systems designed to store and retrieve items with precision, speed, and minimal human intervention. These systems are composed of various components such as storage racks, conveyors, shuttles, cranes, and retrieval devices that work together to automate the movement of goods within a warehouse. ASRS can vary in complexity and size, ranging from simple automated carousels to massive, multi-aisle installations capable of handling thousands of items.
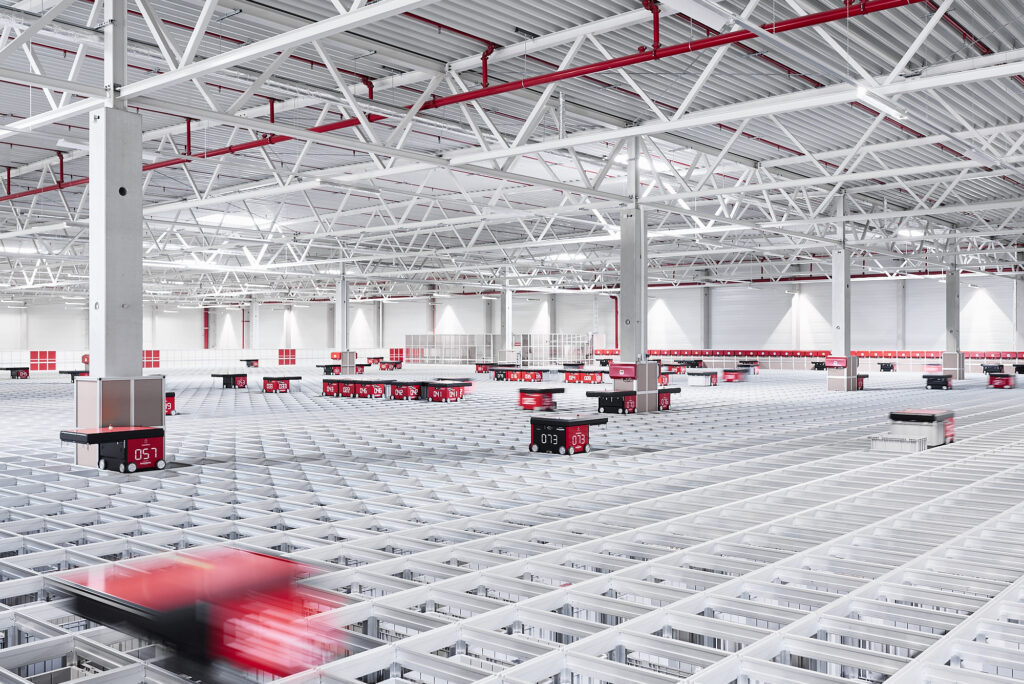
Benefits of ASRS
- Increased Storage Density:
- ASRS systems optimize space utilization by allowing for high-density storage. Goods can be stored in tall, narrow aisles, utilizing vertical space that would otherwise be wasted. This is particularly beneficial in warehouses where space is at a premium.
- Enhanced Speed and Efficiency:
- The automation of storage and retrieval tasks leads to faster processing times. ASRS systems can quickly and accurately retrieve items, reducing the time it takes to fulfill orders. This efficiency is crucial in meeting the demands of just-in-time inventory systems and same-day delivery expectations.
- Reduced Labor Costs:
- By automating tasks that would traditionally require manual labor, ASRS systems help in significantly reducing labor costs. Fewer employees are needed to perform storage and retrieval tasks, and those who are required can focus on more value-added activities.
- Improved Accuracy:
- ASRS systems are highly precise, minimizing the risk of errors in picking and storage. This leads to more accurate inventory management, reducing the likelihood of stock discrepancies and improving overall order accuracy.
- Enhanced Safety:
- The automation of storage and retrieval tasks reduces the need for human interaction in potentially hazardous environments, such as high shelves or narrow aisles, thus improving workplace safety.
Typical Use Cases
ASRS systems are widely used in various industries where the efficient handling of goods is critical. Here are a few common applications:
- Manufacturing:
- In manufacturing environments, ASRS systems are used to store raw materials and components, ensuring they are readily available for production lines. They also help manage the flow of finished goods, optimizing the storage of inventory until it is ready for shipment.
- E-commerce and Retail:
- The rapid growth of e-commerce has led to an increased demand for efficient order fulfillment. ASRS systems enable e-commerce warehouses to handle large volumes of orders with speed and accuracy, ensuring that products are picked, packed, and shipped quickly to meet customer expectations.
- Pharmaceuticals:
- In the pharmaceutical industry, ASRS systems are used to store and manage a wide range of products, from raw materials to finished goods. The precise and controlled environment provided by ASRS is ideal for managing sensitive or perishable items, ensuring compliance with strict industry regulations.
- Cold Storage:
- ASRS systems are particularly beneficial in cold storage environments, where minimizing human exposure to extreme temperatures is important. These systems can efficiently store and retrieve goods in refrigerated or frozen conditions, optimizing the use of space and maintaining product integrity.
In short, Automated Storage and Retrieval Systems are quickly becoming a cornerstone of modern warehouse automation by offering unparalleled efficiency, accuracy, and space optimization. By implementing ASRS, businesses can significantly enhance their storage operations, reduce costs, and improve the overall performance of their supply chains.
Warehouse Management Systems

A Warehouse Management System (WMS) is a sophisticated software solution designed to manage and optimize the day-to-day operations of a warehouse. It serves as the central hub for coordinating various activities such as inventory management, order processing, and shipping.
A WMS provides real-time visibility into inventory levels, tracks the movement of goods, and ensures that orders are fulfilled accurately and efficiently. By integrating with other automation technologies, such as Automated Storage and Retrieval Systems (ASRS), conveyor systems, and robotics, a WMS plays a crucial role in streamlining warehouse operations and enhancing overall efficiency.
The integration of a WMS with warehouse automation technology is a game-changer for modern warehousing. By connecting with automated systems, a WMS can seamlessly coordinate the flow of goods, ensuring that the right products are stored, retrieved, and shipped with minimal human intervention. For example, when an order is received, the WMS can automatically instruct an ASRS to retrieve the necessary items, direct conveyor systems to transport them to the packing area, and update inventory records in real-time. This level of integration not only speeds up the order fulfillment process but also reduces the likelihood of errors, as manual input is minimized.
The Benefits of WMS
The benefits of implementing a WMS are substantial. First and foremost, a WMS enhances accuracy in inventory management by providing real-time data on stock levels and locations. This reduces the risk of stockouts or overstock situations, leading to better inventory control and cost savings.
Additionally, a WMS improves order accuracy by automating key processes such as picking and packing, which minimizes the chance of errors and returns. The system also enables better resource utilization by optimizing labor allocation and equipment usage, resulting in increased productivity. Finally, the data and analytics provided by a WMS allow businesses to make informed decisions, identify areas for improvement, and continuously refine their operations.
Conveyors and Sortation Technologies
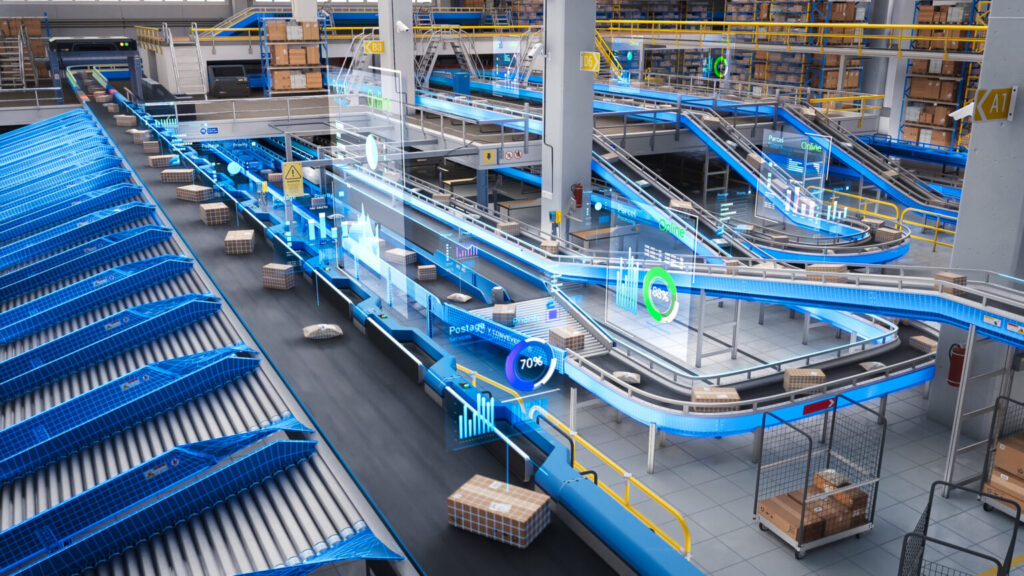
Conveyor systems and sortation technology are fundamental components of warehouse automation, playing a critical role in the efficient movement and organization of goods within a facility. Conveyor belts are mechanical systems that transport items from one point to another along a predetermined path, typically across different stages of the warehouse process.
Sortation systems, on the other hand, are typically more sophisticated technologies that classify and direct items to specific destinations based on predefined criteria such as size, weight, or destination. Together, these systems automate the flow of products through a warehouse, ensuring that goods are accurately and swiftly moved from storage areas to shipping or processing zones.
The Benefits of Conveyors and Sortation
The benefits of conveyor systems and sortation technology are numerous and impactful. Firstly, these systems streamline product movement, eliminating the need for manual handling and reducing the time it takes to transport items across the warehouse. This is particularly beneficial in large facilities where goods must travel significant distances between various operational areas. By automating the transport of products, conveyor systems help to reduce bottlenecks and ensure a smooth flow of goods throughout the facility.
The implementation of these systems significantly reduces handling time. Conveyor systems can move items at a consistent speed, minimizing delays and allowing for continuous operation. Sortation systems further enhance efficiency by automatically directing items to the correct locations, eliminating the need for manual sorting and reducing the risk of errors. This results in faster processing times and quicker order fulfillment, which is essential in meeting customer demands for timely deliveries.
Additionally, conveyor systems and sortation technology contribute to increased throughput—the volume of goods that can be processed within a given time frame. By automating the transport and sorting of items, these systems enable warehouses to handle larger volumes of goods without the need for proportional increases in labor. This is particularly important in high-demand environments such as e-commerce, where the ability to process a large number of orders quickly can be a key competitive advantage.
The integration of conveyor systems and sortation technology with other automation technologies, such as Warehouse Management Systems (WMS) and Automated Storage and Retrieval Systems (ASRS), further amplifies their benefits. A WMS can control and monitor the movement of goods on conveyor belts, ensuring that items are directed to the appropriate areas for storage, picking, or shipping. When integrated with an ASRS, conveyor systems can transport items directly from storage to the sorting area, where they can be automatically classified and routed to the correct destination. This seamless integration reduces manual intervention, increases accuracy, and enhances overall operational efficiency.
Robotics
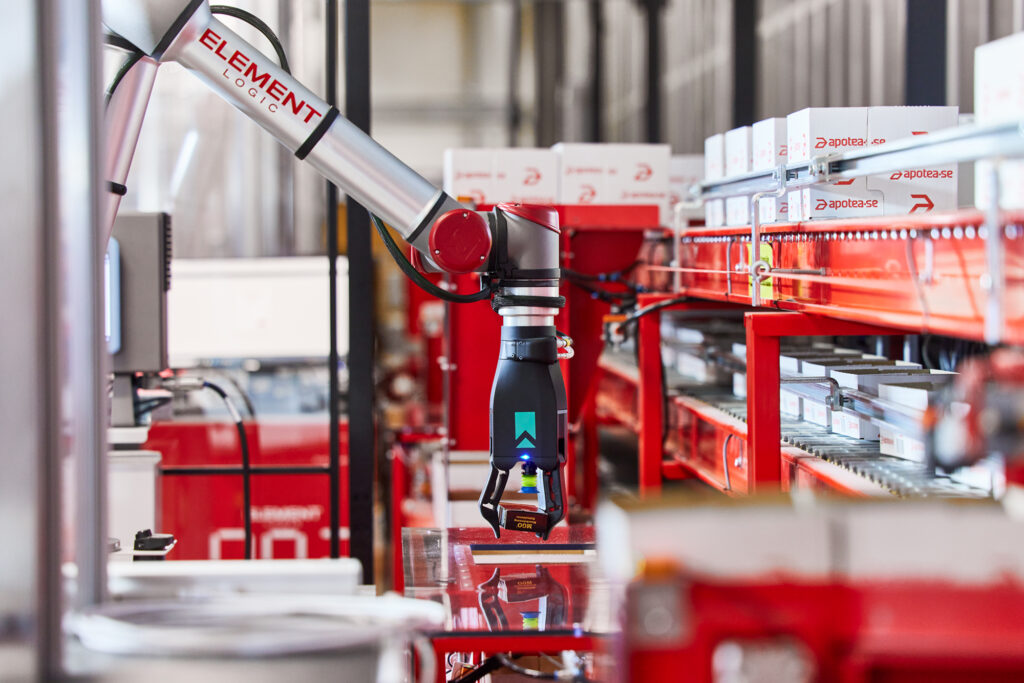
Robotics and collaborative robots, commonly known as cobots, are revolutionizing the landscape of warehouse automation by enhancing productivity, improving safety, and reducing operational costs. Robotics in warehouses encompass a wide range of automated machines designed to perform tasks that were traditionally done by humans. These robots can handle repetitive, physically demanding, or dangerous tasks, allowing human workers to focus on more complex and value-added activities. Cobots, a subset of robotics, are specifically designed to work alongside human employees, complementing their efforts and creating a more efficient and harmonious work environment.
Robotics in Warehousing
In the context of warehousing, robotics can take many forms, from large industrial robots that move pallets and heavy loads to smaller, more agile robots that assist with picking and packing tasks. These robots are typically equipped with advanced sensors, cameras, and artificial intelligence (AI) to navigate the warehouse environment, identify items, and perform their tasks with precision. Robotics can automate various processes, such as material handling, order picking, and inventory management, significantly boosting efficiency and accuracy in warehouse operations.
Cobots
Cobots are a specialized category of robots designed to work near human workers. Unlike traditional industrial robots, which often operate in isolated environments for safety reasons, cobots are built with safety features that allow them to interact directly with humans. These features include sensors and force-limiting technology that enable cobots to detect and respond to human presence, ensuring safe and smooth collaboration.
Cobots are particularly valuable in tasks that require a combination of human dexterity and robotic precision. For example, in order-picking operations, a cobot can work alongside a human picker, fetching items from shelves and delivering them to the packing station. This collaborative approach not only speeds up the process but also reduces the physical strain on workers, as cobots can handle heavy lifting and repetitive movements. Furthermore, cobots can be easily programmed and reprogrammed to perform a variety of tasks, making them highly flexible and adaptable to changing warehouse needs.
Benefits of Robotics and Cobots
The adoption of robotics and cobots in warehouses offers numerous benefits:
- Increased Productivity:
- Robots can operate continuously without the need for breaks, leading to higher throughput and faster order fulfillment. Cobots enhance productivity by allowing humans and robots to work together, maximizing the strengths of both.
- Improved Accuracy:
- Robots are programmed to perform tasks with high precision, reducing the likelihood of errors in picking, packing, and inventory management. This leads to fewer mistakes, returns, and customer complaints.
- Enhanced Safety:
- By taking on physically demanding and hazardous tasks, robots help create a safer work environment for human employees. Cobots further improve safety by working directly with humans in a controlled and safe manner.
- Cost Savings:
- While the initial investment in robotics may be high, the long-term savings from reduced labor costs, improved efficiency, and fewer errors can be substantial. Cobots offer a cost-effective solution due to their flexibility and ease of deployment.
- Scalability:
- Robotics solutions can be scaled to meet the growing demands of a warehouse, allowing businesses to increase their capacity without a corresponding increase in labor costs.
Applications in Warehousing
Robotics and cobots are being utilized in a wide range of warehouse applications. In addition to order picking and material handling, robots are employed in tasks such as sorting, packaging, palletizing, and even quality inspection. Cobots are particularly useful in dynamic environments where human oversight is needed, such as in packing stations or assembly lines.
Robotics and cobots are essential components of modern warehouse automation. By combining the strengths of human workers with the precision and efficiency of robots, warehouses can achieve higher levels of productivity, accuracy, and safety. As these technologies continue to evolve, they will play an increasingly important role in helping businesses stay competitive in the fast-paced world of logistics and supply chain management.
Conclusion
As warehouses face growing pressure to deliver faster, more accurate, and cost-effective services, the adoption of automation technologies has become not just an option, but a necessity. From Automated Storage and Retrieval Systems (AS/RS) that maximize space and efficiency, to Warehouse Management Systems (WMS) that streamline operations and enhance decision-making, to the integration of conveyor systems, sortation technologies, and advanced robotics, these tools are transforming the way warehouses operate. Collaborative robots (cobots) are also playing a pivotal role in bridging the gap between human capabilities and robotic precision, fostering safer and more productive working environments.
The benefits of these essential warehouse automation technologies are clear: they drive productivity, reduce operational costs, improve accuracy, and enable businesses to meet the increasingly complex demands of the modern supply chain. By embracing these technologies, warehouses can not only enhance their current operations but also position themselves for future growth and success. As the industry continues to evolve, those who invest in automation will be better equipped to stay competitive, adapt to changes, and provide exceptional service to their customers. In this rapidly advancing landscape, automation is not just the future of warehousing—it is the key to staying ahead in the present.
Frequently Asked Questions
FAQ 1.) What is the primary benefit of implementing warehouse automation technologies?
The primary benefit of implementing warehouse automation technologies is the significant improvement in operational efficiency. Automation streamlines various processes, such as inventory management, order fulfillment, and material handling, leading to faster processing times, reduced errors, and lower labor costs. Additionally, automation enhances accuracy and consistency in warehouse operations, which translates into better service for customers and higher overall productivity.
FAQ 2.) How do collaborative robots (cobots) differ from traditional industrial robots in a warehouse setting?
Collaborative robots, or cobots, are designed to work alongside human workers, unlike traditional industrial robots that typically operate in isolated environments for safety reasons. Cobots are equipped with advanced sensors and safety features that allow them to detect and respond to human presence, ensuring safe and efficient collaboration. They are also more flexible and easier to program than traditional robots, making them ideal for tasks that require a combination of human dexterity and robotic precision, such as order picking or packing.
FAQ 3.) How do Warehouse Management Systems (WMS) integrate with other automation technologies in a warehouse?
Warehouse Management Systems (WMS) serve as the central hub for managing and coordinating various automation technologies within a warehouse. A WMS can integrate with Automated Storage and Retrieval Systems (AS/RS), conveyor systems, sortation technology, and robotics to streamline the movement of goods and optimize inventory management. For example, a WMS can automatically instruct an AS/RS to retrieve items for an order, direct conveyor belts to transport goods to the packing area, and update inventory records in real-time. This integration enhances efficiency, accuracy, and overall operational performance.