Conveyor Maintenance: How to Prolong Your Sortation Systems
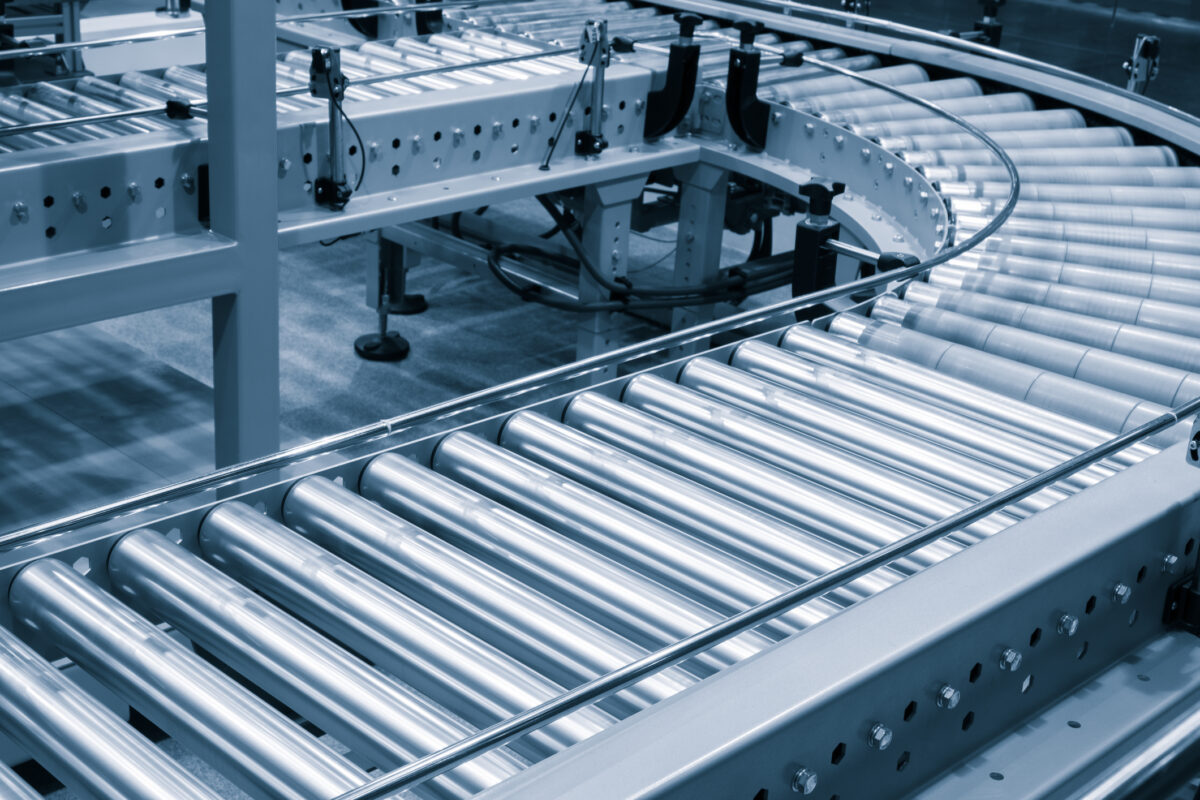
Why Conveyor System Maintenance is Important
Conveyor system maintenance is crucial in the automation industry for multiple reasons. The first of which is to ensure operational efficiency. By regularly conducting maintenance you can ensure your conveyor systems operate at peak efficiency. This includes checking for any signs of wear and tear, aligning belts properly, and addressing any issues that may cause slowdowns or stoppages. A well-maintained conveyor system helps maintain a smooth and continuous flow of materials, preventing disruptions in the production process.
Another large contributing factor to why conveyor system maintenance is important is the reduction of downtime. Unplanned downtime can be costly in terms of lost production time and revenue. Regular conveyor maintenance helps identify and address potential issues before they lead to breakdowns. Preventive maintenance schedules can be established to replace worn components, reducing the likelihood of unexpected failures, and minimizing downtime. Preventive maintenance helps identify issues early on, allowing for planned and budgeted repairs instead of costly emergency interventions.
Well-maintained conveyor systems often operate more efficiently, leading to energy savings. Misaligned belts, worn bearings, or dirty components can increase energy consumption. Regular maintenance helps keep the system in optimal condition, contributing to energy efficiency and cost savings.
Being compliant with quality standards in the automation industry is crucial. Especially in participating industries where product quality is of the utmost importance, conveyor systems play a role in maintaining the integrity of the production process. Regular maintenance ensures that the conveyor system operates within specified tolerances, contributing to the consistent quality of the end products.
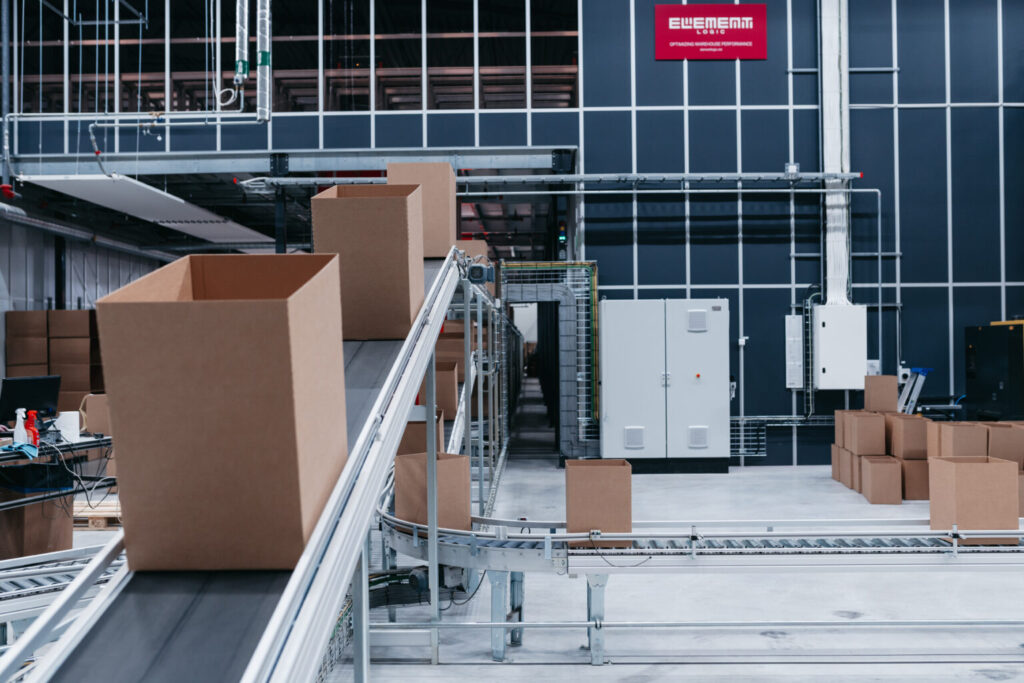
Common Conveyor Belt Issues
In the dynamic landscape of industrial automation, conveyor systems play a pivotal role in material handling and production efficiency. Like any mechanical system however, conveyor belts are susceptible to a range of common issues that, if left unaddressed, can lead to disruptions in operation, decreased efficiency, and increased maintenance costs. Understanding and proactively managing these challenges are essential for maintaining the reliability and longevity of conveyor systems. From misalignment and belt slippage to wear and tear, each issue requires specific attention and preventive measures.
Below you will find an overview in which we delve into the common conveyor belt issues encountered in industrial settings, shedding light on their causes, consequences, and the importance of diligent maintenance practices in mitigating these challenges.
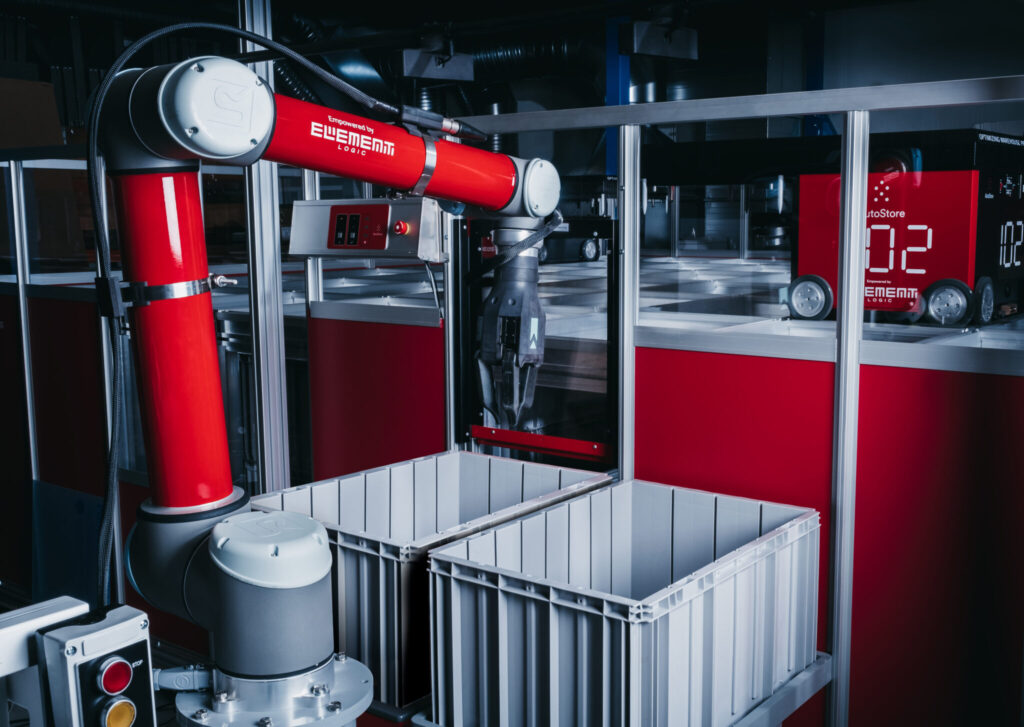
- Misalignment: Misalignment is a common conveyor belt issue where belts may veer off-center. This problem is often caused by uneven loading, incorrect tension, or structural issues with the conveyor frame. Misalignment can lead to increased wear on the belt, reduced efficiency, and potential damage to the conveyor system components.
- Belt Slippage: Belt slippage occurs when the conveyor belt slips on the pulleys, usually due to insufficient friction between the belt and the drive pulley. This issue can result in a decrease in conveying efficiency, material spillage, and even system downtime. Adequate tension and proper maintenance are crucial in preventing and addressing belt slippage.
- Residue Buildup: The accumulation of material residue on conveyor belts and rollers is a common challenge, particularly in industries dealing with sticky or adhesive substances. Residue buildup can lead to increased friction, belt slippage, and misalignment. Regular cleaning and maintenance are essential to prevent these issues and ensure the smooth operation of the conveyor system.
- Belt Wear and Tear: Continuous friction from carrying materials on the belt can cause wear and tear over time. This issue may lead to belt degradation, compromising its structural integrity and necessitating premature replacements. Regular inspection and preventive maintenance are key to identifying and addressing areas of excessive wear before they escalate.
- Belt Jams, Cuts, or Rips: Belt jams, cuts, or rips can occur due to foreign objects getting lodged in the conveyor system or abrupt material handling. These issues can lead to sudden stoppages, increased downtime, and potential damage to the conveyor belt. Proper material handling practices and regular system inspections are crucial in preventing such incidents.
- Motor and Drive Issues: Conveyor systems rely on motors and drives for efficient operation. Issues such as motor malfunctions, drive belt problems, or electrical failures can disrupt the system’s functionality. Regular inspection, timely repairs, and preventive maintenance of motors and drives are vital to prevent unexpected breakdowns.
- Inadequate Lubrication: Insufficient lubrication of moving parts, such as pulleys and bearings, can lead to increased friction, wear, and potential failures. Adequate and regular lubrication is crucial for preventing these issues and ensuring the smooth operation of the conveyor system.
- Temperature Extremes: Extreme temperatures can adversely affect the functioning of conveyor belts. In high temperatures, belts may experience accelerated wear and reduced material handling capabilities, while low temperatures can cause belt stiffness and potential cracking. Adapting the conveyor system to temperature extremes and implementing proper maintenance measures is essential for optimal performance in challenging environmental conditions.
- Uneven Belt Tension: Maintaining consistent tension across the conveyor belt is essential for optimal performance. Uneven tension can result in misalignment, slippage, and increased wear. Regular tension adjustments and monitoring are necessary to prevent these issues and ensure the even distribution of forces throughout the conveyor system.
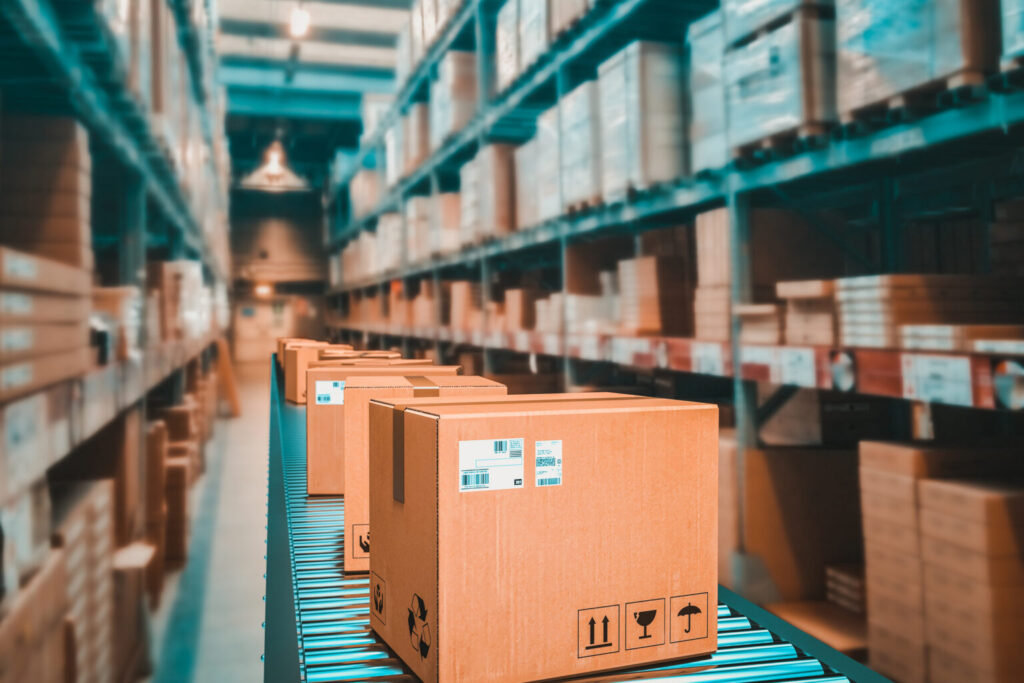
Cleaning Protocols for Your Conveyor Belt
To sustain the harmonious rhythm of production in a distribution center, it is imperative to recognize the pivotal role of cleanliness in ensuring the optimal functionality of conveyor belts. Cleaning protocols for conveyor belts are not merely routine maintenance tasks; they are strategic maneuvers to thwart the accumulation of debris, contaminants, and wear that could disrupt operations.
Cleaning Protocols for Conveyor Belts:
Maintaining a clean conveyor belt is paramount for ensuring optimal performance and preventing issues such as material residue buildup, misalignment, and premature wear.
Begin by thoroughly removing debris and contaminants from the belt surface using appropriate cleaning tools. Regular inspections and cleaning intervals help prevent the accumulation of materials that could lead to increased friction, belt slippage, or tracking problems.
In addition to cleaning the belt, it is crucial to ensure proper belt tension. Adequate tension prevents slippage and misalignment, contributing to the overall efficiency of the conveyor system. Regular tension checks and adjustments should be incorporated into routine maintenance schedules.
Cleaning Sensors and Controllers:
Sensors and controllers are integral components of modern conveyor systems, facilitating automation and precision in material handling.
To maintain their accuracy and functionality, it is imperative to implement a comprehensive cleaning protocol. Remove dust and debris that may accumulate on sensors, as this can compromise their ability to provide accurate readings. Regular cleaning not only ensures reliable data but also prevents false readings that could lead to operational errors.
To ensure optimal connectivity by inspecting and cleaning the controller interfaces. Clean and secure connections contribute to the seamless communication between components, reducing the risk of system malfunctions. Integrating these cleaning protocols into regular maintenance routines enhances the overall reliability and efficiency of conveyor systems, ultimately promoting uninterrupted and precise material handling processes.
Best Practices for Maintaining Your Sortation Systems
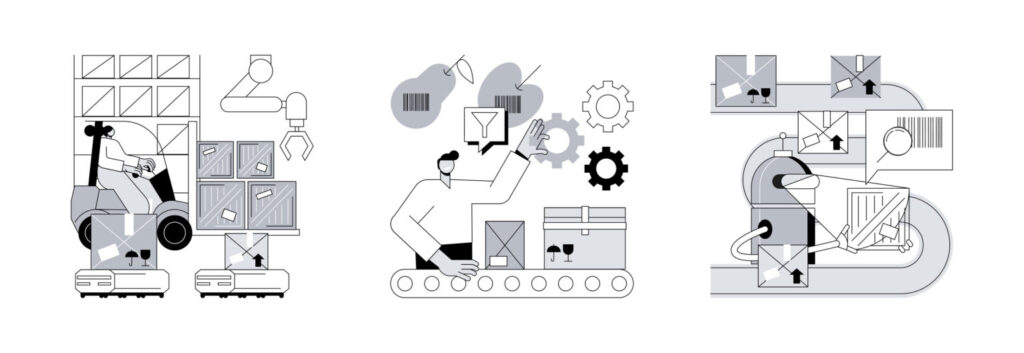
Maintaining an efficient and reliable sortation system is paramount for businesses reliant on streamlined logistics and distribution processes. Adopting best practices in system maintenance ensures a seamless flow of goods, minimizes downtime, and contributes to long-term cost savings. One crucial step in this endeavor is hiring a dedicated maintenance technician well-versed in the intricacies of sortation systems. This skilled professional becomes the frontline defender against potential issues, conducting regular inspections and addressing any emerging problems promptly.
In addition to having a skilled technician on board, implementing preventative maintenance practices is essential. This proactive approach involves identifying and rectifying potential issues before they escalate, ultimately preventing costly system breakdowns. Establishing a well-structured and consistent maintenance schedule is equally vital. Regular inspections, lubrication, and adjustments should be part of this routine to ensure the ongoing optimal performance of the sortation system.
To further fortify the system against unforeseen hiccups, it’s prudent to invest in spare parts and keep them readily available. This strategic measure reduces downtime in the event of component failures, allowing for swift replacements and minimal disruption to operations. Documentation plays a pivotal role in this process. Maintenance staff should have quick access to equipment manuals, walk-through notes, and any relevant documentation that aids in troubleshooting and repairs.
Moreover, considering the complexity of modern sortation systems, hiring an expert in the field can provide invaluable insights and specialized knowledge. This expert can offer guidance on system upgrades, technological advancements, and optimal maintenance strategies tailored to the specific needs of the business.
In essence, the best practices for maintaining sortation systems encompass a holistic approach that combines skilled personnel, preventative measures, consistent scheduling, readily available spare parts, comprehensive documentation, and the expertise of industry professionals. By adhering to these practices, businesses can ensure the longevity, reliability, and continued efficiency of their sortation systems, ultimately contributing to the overall success of their logistics and distribution operations.