
Continental’s Story in Guadalajara, Mexico
Continental, a global technology leader in automotive manufacturing and mobility solutions, took a significant step in advancing its warehouse operations by implementing AutoStore at its Periférico Plant in Guadalajara, Mexico.
(Read Press Release).
This state-of-the-art automated storage and retrieval system (ASRS) marks a new chapter in Continental’s pursuit of operational excellence and digital transformation.
Designed to optimize space utilization, enhance order accuracy, and improve productivity, the AutoStore system is a testament to Continental’s commitment to innovation and efficiency in its supply chain processes. With a focus on intelligent automation, the Guadalajara plant aims to set a new benchmark for streamlined operations in the automotive industry.
Continental Video Case Study
Challenge
Continental’s Periférico Plant faced a critical challenge: limited floor space that constrained its ability to efficiently manage inventory and meet increasing demand. As the company continued to grow and diversify its product offerings, it became evident that traditional warehousing methods were no longer sufficient.
“We started in 2001 in Guadalajara, Mexico. With 23 years of experience here at the plant, we are looking for an increase in quality of life for our employees.”
Sergio Márquez, Plant & Location Manager at Continental
The need for a scalable solution that could maximize storage capacity without requiring additional floor space became a top priority. Continental sought a system that could adapt to their evolving needs while ensuring seamless operations and high productivity.
Solution
To address these challenges, Continental turned to Element Logic. AutoStore, an ASRS known for its unique approach to warehouse efficiency and organization, has a modular design which allowed Continental to maximize storage capacity by utilizing vertical space. This effectively overcame the plant’s floor space limitations. The system’s high-speed robots efficiently retrieve items from a dense grid of bins, ensuring quick access to inventory while reducing strainful manual labor.
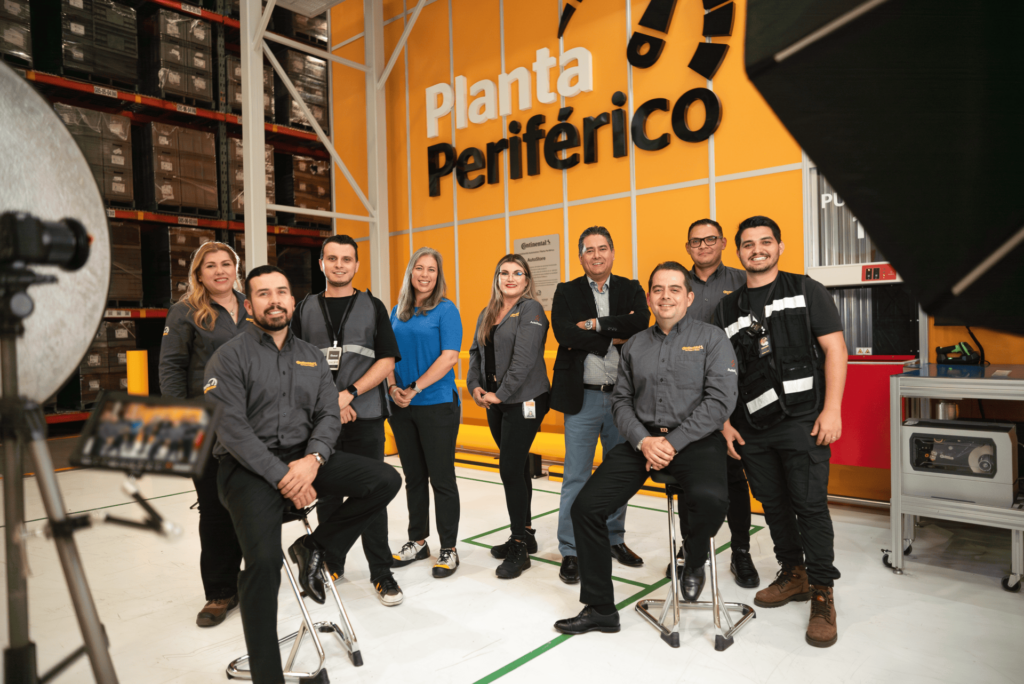
From left to right: Fernanda Morales Witrago, Communications Specialist at Continental; César Rodriguez Valadez, Advanced SCM Project Manager at Continental; Santiago Corona, Videographer; María Elena Ladrón de Guevara, Director of Marketing – Americas at Element Logic, María Luz del Alba Pérez, Head of Plant Communication & Executive Assistant at Continental, Sergio Márquez, Plant & Location Manager at Continental; José Luis Quezada, Head of Plant SCM at Continental; Salvador Nuñez, Material Flow Manager at Continental; and Santiago Corona, Videographer.
“The transfer times we had before AutoStore were much longer than they are today. We could not be happier with the performance. We have increased delivery of materials, both internal and external, by 67%”
Salvador Nuñez, Material Flow Manager at Continental
By implementing AutoStore, Continental was able to streamline its operations with an automated solution that enhanced inventory management, improved order accuracy, and increased overall productivity. The flexibility and scalability of AutoStore also meant that the system could be easily adapted to meet future growth, providing a long-term solution to Continental’s evolving warehousing needs.
Impact
The implementation of AutoStore has had a transformative impact on Continental’s Periférico Plant, driving both operational and employee-centric improvements. By optimizing storage capacity and automating repetitive tasks, the system has enabled Continental to handle larger volumes of inventory and meet customer demand more effectively. Order processing is now faster and more accurate, reducing errors and improving customer satisfaction.
“… we have greatly increased our security levels- which is a very important issue for Continental”
José Luis Quezada, Head of Plant SCM at Continental
“Continental has seen quite a few improvements.” José Luis Quezada, Head of Plant SCM at Continental said. “Once we implemented AutoStore, we began optimizing our resources as well as optimizing the workforce we have here. Additionally, we have greatly increased our security levels- which is a very important issue for Continental”
For employees, the shift to automated processes has significantly enhanced their quality of life. Tasks that were previously labor-intensive and physically demanding have been replaced by automated systems, reducing the risk of injuries and allowing staff to focus on more value-added activities. This has created a safer and more engaging work environment, fostering higher employee morale and job satisfaction.
Overall, AutoStore has equipped Continental with a future-proof solution that supports the company’s growth ambitions. The Guadalajara plant is now better positioned to scale operations, adapt to market changes, and continue delivering high-quality products efficiently and accurately. The successful integration of AutoStore underscores Continental’s commitment to innovation and operational excellence in a highly competitive industry.
Results
“Continental was looking for a highly efficient solution in a limited amount of space that would allow them to protect their products from debris.” Cristian Ahumada, Director of Operations – LatAM at Element Logic said. “Furthermore, they wanted a solution that had high processing rates. For all these reasons, AutoStore was the ideal solution for them.”
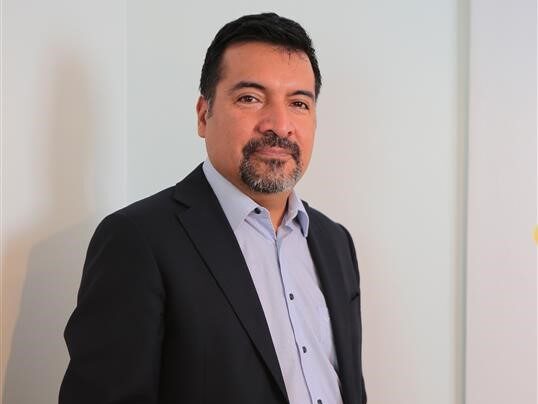
… AutoStore was the ideal solution for them.
Cristian Ahumada, Director of Operations – LatAM at Element Logic
Element Logic’s successful implementation of AutoStore at Continental’s Periférico Plant has delivered impressive results. The system has significantly increased space optimization, allowing Continental to make the most of its available warehouse area. Speed and efficiency have also improved, enabling faster order processing and reducing lead times. Additionally, the AutoStore system has proven to be highly reliable, ensuring consistent performance with minimal downtime. Its flexibility and scalability ensure that the system can adapt to future business needs, providing Continental with a robust and sustainable solution for long-term success.