The Importance of Conveyor Belts in Warehouses
In today’s fast-paced logistics landscape, warehouse automation is more critical than ever, serving as the backbone of efficient and scalable operations.
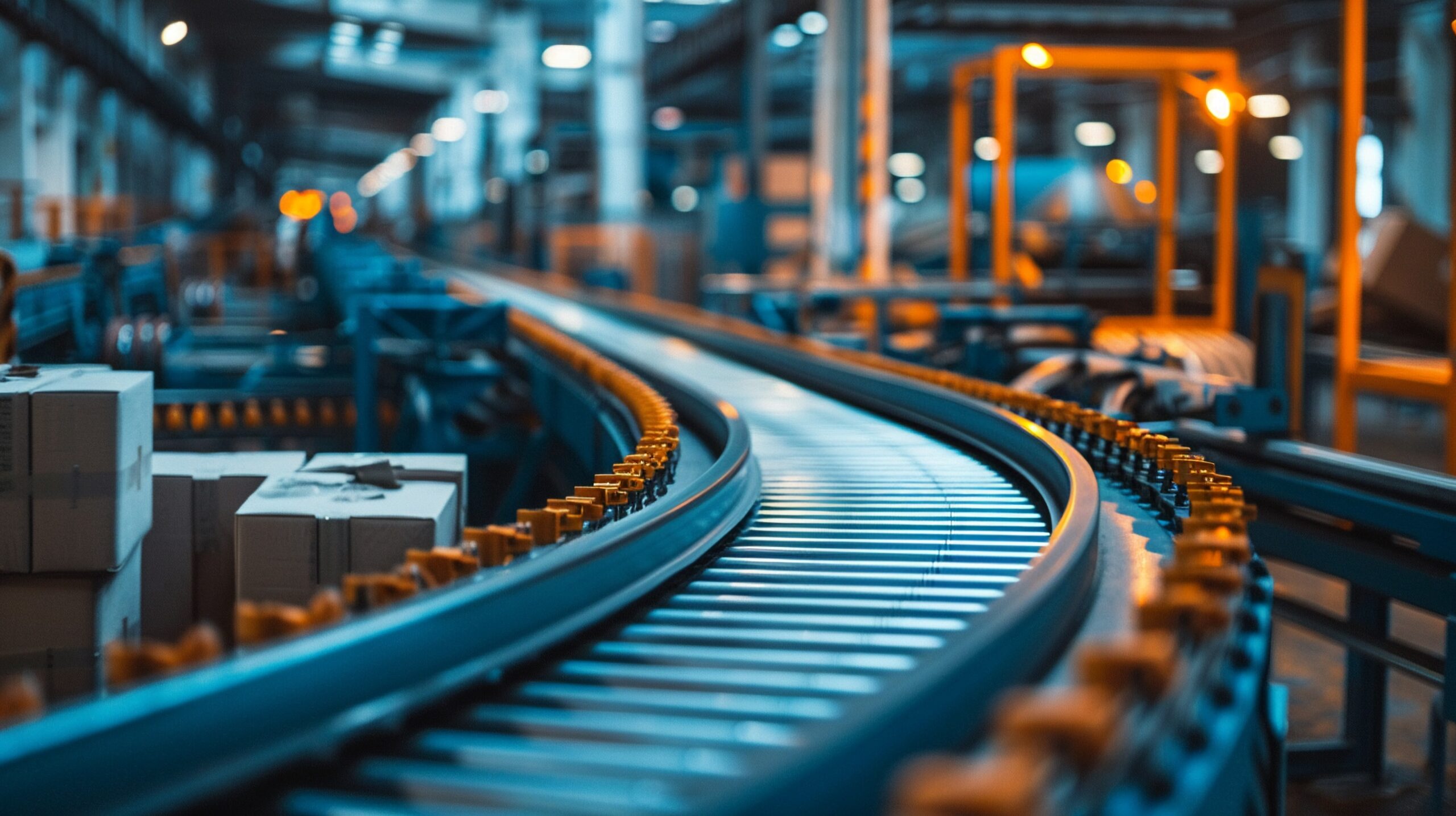
Among the many tools transforming warehouse workflows, conveyor belts stand out as foundational components, revolutionizing the way products move through fulfillment centers. As e-commerce and global supply chains grow, so does the need for systems that can handle a high volume of goods with speed and accuracy. This demand has propelled the evolution of conveyor technology, with new, versatile designs and capabilities emerging to keep up with modern logistics requirements.
Conveyor belts are no longer just simple transportation mechanisms; they are integral to achieving seamless warehousing operations. They facilitate the rapid, consistent movement of goods across various points in the warehouse, from receiving to dispatch. By reducing the need for manual handling, conveyor belts streamline the entire process, making it easier to maintain order accuracy and meet high customer expectations.
In modern warehousing, conveyor systems are vital for enhancing productivity, accelerating order fulfillment, and reducing operational costs. Their ability to integrate with other automation technologies, such as warehouse management systems (WMS) and robotic sortation, further cements their role in today’s automated warehouses. As an essential part of any competitive operation, conveyor belts not only cut costs but also improve overall warehouse efficiency, allowing companies to achieve more with fewer resources.
Types of Conveyor Belts Used in Warehouses
Efficient warehouse operations require a variety of conveyor belt types, each suited to different tasks and handling needs. Choosing the right conveyor system is essential for ensuring smooth material flow, maximizing space, and maintaining high productivity.
1.) Belt Conveyors
- Description and Common Applications:
Belt conveyors are among the most versatile and widely used conveyor types. Comprised of a continuous loop of material stretched over pulleys, these conveyors use friction to move items along the belt, making them ideal for handling goods in bulk or as individual packages. They come in various widths and lengths to accommodate different product sizes. - Suitable for Moving a Variety of Items:
These conveyors are suitable for transporting items across long distances within a warehouse, particularly for products that require a gentle touch. From lightweight packages to bulk goods, belt conveyors offer an efficient way to handle goods of varied shapes and sizes, ensuring steady, reliable movement across warehouse zones.
2.) Roller Conveyors
- Types: Gravity vs. Powered
Roller conveyors are made up of a series of rollers placed closely together, enabling the smooth movement of heavy or bulky items.
Gravity Roller Conveyors rely on gravity and are ideal for moving goods down slight inclines, reducing energy costs.
Powered Roller Conveyors use motors to move the rollers, providing consistent and controlled movement, even on flat surfaces.
- Usage in Heavy-Duty Item Movement:
Due to their durability, roller conveyors are often used for transporting heavier items, such as large packages or pallets. Their modular design makes them easy to integrate into various parts of a warehouse, especially in areas where manual handling is impractical due to item weight or volume.
- 3.) Pop-Up Wheel Sorters and Sliding Shoe Sorters
- Ideal for Automated Sortation and Redirection
Both pop-up wheel sorters and sliding shoe sorters are designed to divert items along different paths, making them valuable for sortation applications.
Pop-Up Wheel Sorters have wheels that emerge from the conveyor’s surface to redirect items at high speed, ideal for lightweight goods.
Sliding Shoe Sorters use sliding “shoes” to push items gently along a specified path, handling delicate items more safely and reducing risk of damage. - These systems are crucial in warehouses with high throughput needs, as they facilitate rapid sorting and accurate order fulfillment by directing goods to their designated areas with minimal manual intervention.
4.) Narrow Belt Sorters
- Description and Role in Item Segregation and Space Efficiency
Narrow belt sorters use several small belts running parallel to each other to carry items, with diverts that redirect specific items to different destinations. Due to their compact design, narrow belt sorters are particularly well-suited for warehouses with space constraints, as they allow efficient use of limited floor space. - Applications in Warehouse Sorting and E-commerce Fulfillment
Narrow belt sorters excel in order segregation, particularly in e-commerce operations where a high volume of diverse items must be sorted quickly and accurately. Their ability to direct products precisely into different chutes or bins makes them invaluable for warehouses needing precise, space-efficient sorting.
Key Benefits of Conveyor Belts in Warehousing Operations
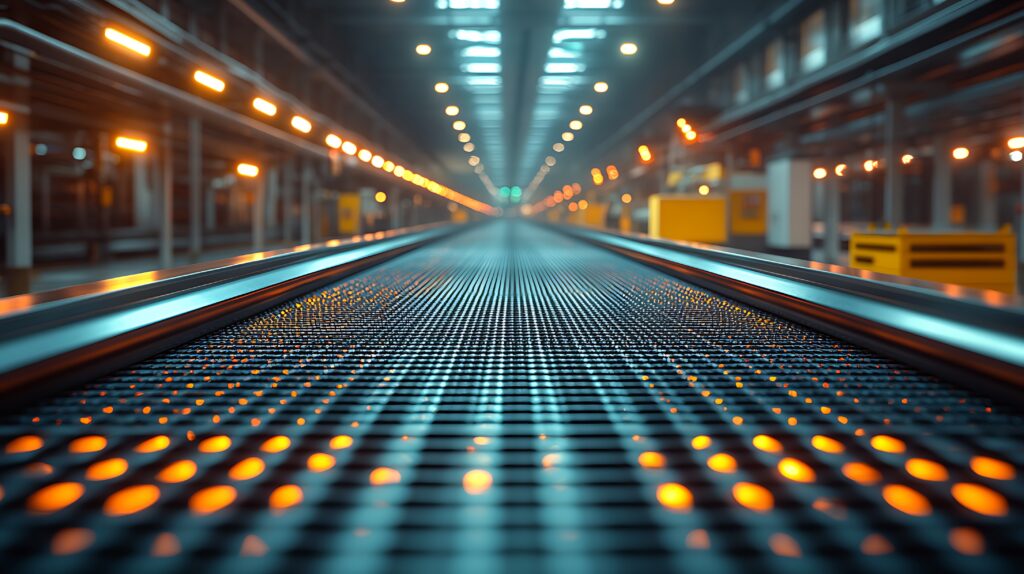
Conveyor belts bring substantial benefits to warehousing operations, significantly boosting productivity, safety, and accuracy. One of the primary advantages is increased efficiency and throughput; conveyor systems streamline the movement of goods across warehouse zones, accelerating order processing and reducing the need for manual handling. This automation minimizes bottlenecks, allowing goods to flow continuously and reach their destinations faster, which is especially valuable in high-demand environments where speed is essential for meeting customer expectations.
In addition to enhancing efficiency, conveyor belts also contribute to lower labor costs and a safer work environment. By automating the transportation of goods, conveyors reduce the dependency on manual labor, cutting down operational costs over time. They also mitigate workplace injuries, as employees no longer need to lift and carry heavy or awkwardly shaped items, reducing the ergonomic strain that can lead to repetitive stress injuries or accidents. This benefit is essential for maintaining a safe and sustainable workforce in warehouses that handle high volumes of goods.
Conveyor belts further improve warehouse operations by enhancing inventory and order accuracy. Through systematic and controlled transportation of items, conveyors reduce the likelihood of errors that can occur with manual handling, such as misplacing or mishandling products. This level of precision ensures that products are correctly transported to their designated locations, supporting accurate inventory tracking and reliable order fulfillment. Accuracy is particularly important in large-scale warehouses or e-commerce fulfillment centers, where errors can result in costly returns or customer dissatisfaction.
Another significant benefit of conveyor belts is their flexibility for integration with WMS. Conveyors can sync with WMS software, which optimizes workflows by enabling real-time tracking and automation of processes. This integration allows conveyors to direct goods efficiently through various warehouse stages based on data-driven insights, making operations smoother and more responsive to demand fluctuations. Overall, conveyor belts play a vital role in creating a more efficient, accurate, and safe warehouse environment while providing the adaptability needed for continuous improvement in modern logistics.
How Conveyor Belts Improve Operational Scalability
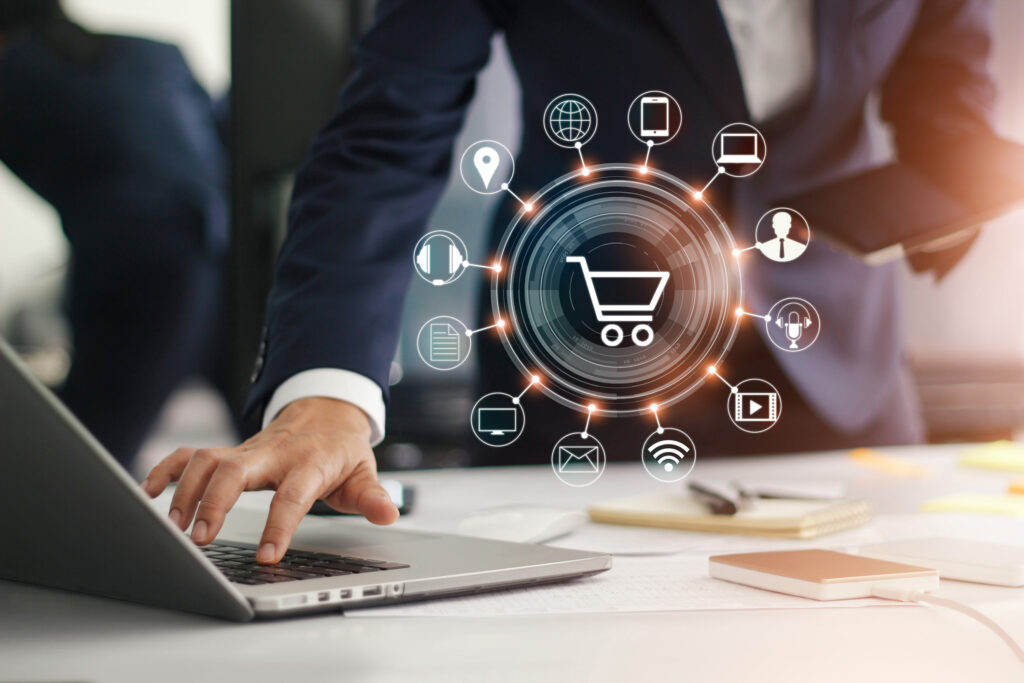
Conveyor belts are instrumental in enhancing the scalability of warehouse operations, allowing facilities to efficiently manage fluctuations in demand and easily adapt to future growth. One of the key ways conveyor belts support scalability is through their adaptability to demand fluctuations. In peak seasons, such as holidays or promotional events, the ability to increase throughput is crucial. Conveyor systems provide a scalable solution, enabling warehouses to handle higher volumes without compromising processing speed or accuracy. Their continuous, automated movement streamlines the flow of goods, helping facilities keep up with demand surges while reducing the risk of bottlenecks.
Another major factor that makes conveyor belts scalable is their modularity and customization. Modern conveyor systems are often designed as modular units, allowing warehouses to expand or adjust the conveyor layout as needed. This modularity means warehouses can introduce new sections or reconfigure existing ones without major operational disruptions or costly renovations. As a result, facilities can easily adapt to layout changes, expansion plans, or shifts in product lines, making conveyor systems a cost-effective and flexible choice for evolving warehousing needs.
Conveyor belts also improve scalability by seamlessly integrating with other automation technologies, including sortation systems, robotic arms, and automated storage and retrieval systems (ASRS). These integrations allow warehouses to create a cohesive and synchronized automated workflow, from picking and sorting to packing and dispatch. For example, conveyor belts can work in tandem with robotic sorters to automatically direct products to specific packing areas based on order requirements.
Additionally, integration with ASRS enables efficient storage and retrieval, maximizing space utilization while keeping goods accessible. This compatibility with advanced automation technologies ensures that conveyor belts can scale alongside other automated solutions, supporting long-term growth while optimizing overall warehouse performance. Through these flexible, adaptable, and integrative features, conveyor belts play a pivotal role in helping warehouses meet expanding operational demands.
Challenges and Considerations for Conveyor Belt Installation
Installing conveyor belts in a warehouse involves several challenges and considerations, particularly around cost, space requirements, and maintenance. The initial investment can be substantial, and while the long-term benefits often justify the expense, it’s crucial to weigh the return on investment (ROI) against the upfront cost. Conveyor systems can reduce labor costs, increase efficiency, and improve accuracy, but the financial commitment for purchasing, installing, and configuring the system can be high. Businesses should assess factors like potential throughput increases and labor savings over time to understand how quickly the investment may pay off. For many warehouses, the ROI proves worthwhile, but careful cost analysis is essential to confirm this.
Space requirements and layout design are also critical considerations. Conveyor systems require adequate space and a thoughtful layout that integrates smoothly into the existing workflow. Effective planning is essential to ensure that the conveyor belts do not obstruct other operations and that they facilitate a seamless flow of goods throughout the facility. The layout should be strategically designed to avoid bottlenecks and ensure the system is placed where it can contribute the most to operational efficiency. Additionally, warehouses with limited space must carefully consider whether the added benefit of conveyors outweighs any loss of floor space, as the conveyor layout will directly impact storage and movement capabilities.
Maintenance and minimizing downtime are other essential considerations in conveyor belt installation. Since conveyor belts are in constant use, regular maintenance is crucial to keep the system running smoothly and prevent unplanned stoppages. Maintenance includes routine inspections, part replacements, and ensuring the conveyor components remain in good working condition. Without regular upkeep, conveyor belts can experience breakdowns, leading to costly disruptions that impact overall productivity. By implementing a preventive maintenance program and investing in high-quality components, warehouses can minimize downtime and extend the lifespan of their conveyor systems, ensuring they remain reliable and continue to deliver the intended productivity gains over the long term.
Future Trends in Conveyor Belt Technology
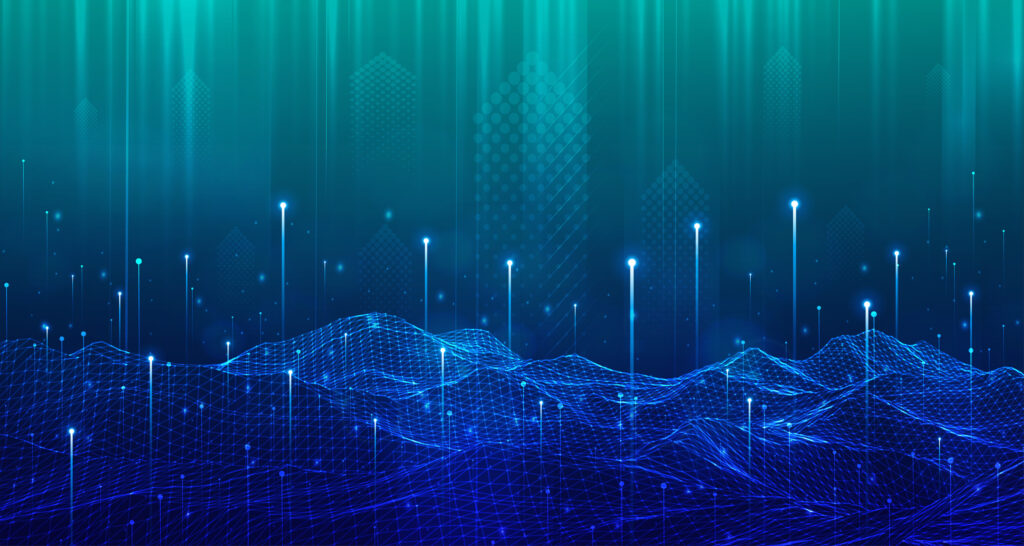
The future of conveyor belt technology is set to be shaped by advancements in AI, smart materials, and the Internet of Things (IoT), each promising to make conveyor systems more efficient, sustainable, and intelligent. One of the most transformative trends is the integration of AI and machine learning into conveyor operations. By leveraging AI, conveyor systems can enable predictive maintenance, identifying potential issues before they cause disruptions. AI-driven analytics can monitor wear and tear on components, predict when parts will need replacement, and even optimize the speed and routing of items to maximize overall throughput. This intelligence not only minimizes downtime but also improves the system’s adaptability to fluctuating demands, enhancing operational efficiency and longevity.
Sustainability is also becoming a priority in conveyor technology, with growing interest in smart and eco-friendly materials. Future conveyor belts are expected to be constructed with recyclable, durable, and low-impact materials to reduce environmental footprint. Alongside these materials, energy-efficient motors and components are being incorporated to minimize power consumption. These sustainable advancements help warehouses reduce operational costs while supporting eco-friendly initiatives. As environmental regulations become stricter, investing in green conveyor technology allows businesses to stay compliant and align with global sustainability goals, making warehouses both more efficient and environmentally responsible.
IoT-enabled conveyor systems represent another major trend that enhances real-time monitoring and data-driven optimization. With IoT sensors embedded throughout the system, warehouses can track conveyor performance in real-time, collecting data on aspects like belt speed, load weight, and energy consumption.
This data is invaluable for making immediate adjustments, detecting issues early, and continuously optimizing conveyor performance. IoT integration also allows for remote management, providing insights that can be accessed anytime, anywhere. By harnessing the power of IoT, conveyor systems can become increasingly autonomous, supporting a warehouse environment that is more connected, responsive, and optimized for peak performance. Together, these advancements in AI, sustainable materials, and IoT-enabled systems are redefining conveyor belt technology, paving the way for smarter, greener, and more resilient warehouse operations.
Conclusion
In conclusion, conveyor belts are essential to modern warehouse operations, bringing remarkable improvements in efficiency, scalability, and cost-effectiveness. Their role in automating the movement of goods not only enhances throughput but also reduces labor demands and minimizes errors, helping warehouses meet today’s high customer expectations. As industry evolves, the flexibility and modularity of conveyor systems allow facilities to scale with demand, while seamless integration with other automation technologies ensures a cohesive and efficient workflow.
Looking to the future, advancements in AI, sustainable materials, and IoT integration are setting new standards for conveyor belt technology. These innovations promise smarter, more eco-friendly systems that can self-monitor, optimize, and adapt to operational needs in real time. For warehouses seeking to remain competitive and resilient, investing in advanced conveyor solutions is a strategic move that prepares them for ongoing growth and change in a dynamic logistics landscape. Embracing these technologies allows warehouses to not only streamline operations but also build a sustainable foundation for the future of fulfillment.
Frequently Asked Questions
FAQ 1. How do conveyor belts help reduce costs in warehouse operations?
Conveyor belts help reduce costs by automating the movement of goods within a warehouse, which minimizes the need for manual labor and reduces associated labor costs. They also improve accuracy in item handling, decreasing errors that can lead to costly returns or lost inventory. Additionally, conveyor belts enhance operational efficiency, enabling higher throughput and faster order processing, which lowers overall operational expenses and improves ROI.
FAQ 2. What types of conveyor belts are most commonly used in warehouses?
The most common types of conveyor belts in warehouses include belt conveyors, roller conveyors, pop-up wheel sorters, sliding shoe sorters, and narrow belt sorters. Each type is suited to different operational needs: belt conveyors are versatile and handle various items, roller conveyors are ideal for heavy-duty items, and sorters like pop-up wheel and sliding shoe are perfect for directing items to specific areas. Narrow belt sorters are often used in space-constrained areas, making them popular in e-commerce and fulfillment operations.
FAQ 3. How can conveyor belts integrate with other automation technologies?
Modern conveyor belts are highly compatible with other automation technologies, such as warehouse management systems (WMS), robotic arms, and automated storage and retrieval systems (ASRS). Integration with WMS enables data-driven routing and efficient item tracking. Conveyor systems can work alongside robotic arms for automated picking and packing, and they integrate seamlessly with ASRS to facilitate smooth movement between storage and retrieval points. This compatibility creates a cohesive, automated workflow that optimizes warehouse operations.