Automating in a Brownfield or Greenfield: New vs Existing Buildings
As industries continue to embrace automation to enhance efficiency and competitiveness, businesses face a critical decision …
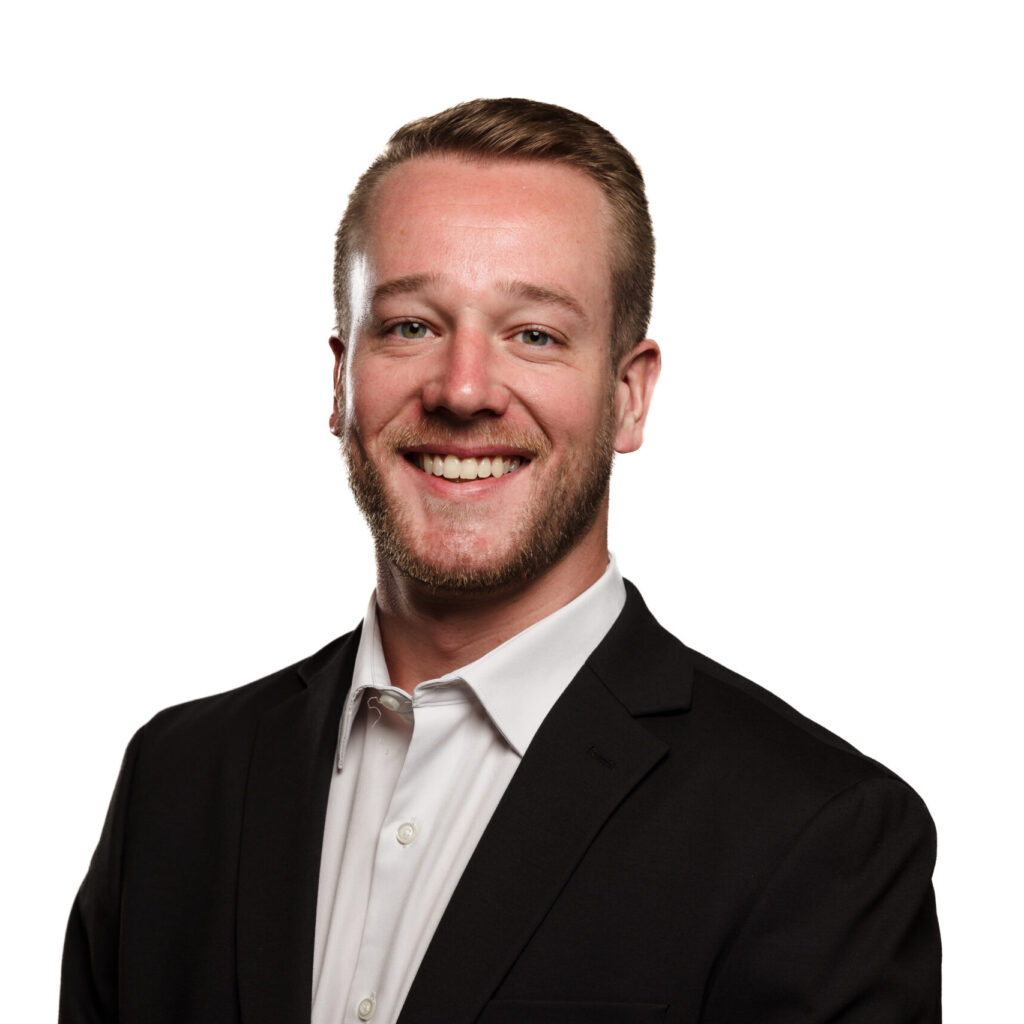
Article by Josh Beckham
Should they integrate automation into existing facilities, known as a “Brownfield”, or build new automated facilities from the ground up, known as a “Greenfield”? Each approach presents its own set of opportunities and challenges, shaped by the unique characteristics of the environments in which they are implemented.
In this article, we will explore the key differences between automating in brownfield and greenfield environments. By examining factors such as cost, flexibility, and implementation challenges, we’ll provide a balanced view of how each option can impact a company’s automation strategy. Whether you’re working within the constraints of an existing facility or starting fresh with a new build, understanding the nuances of these environments is essential for making informed decisions that align with your business goals.
Defining Brownfields and Greenfields
We have grazed the surface on what a brownfield and greenfield facility is above but let’s dive in deeper to get a better understanding.
Brownfield: A brownfield refers to an existing building or facility that is already in use but may need upgrades, retrofitting, or adaptation for new technologies or processes. In the context of automation, a brownfield project involves integrating automation into an existing structure, which often presents challenges related to legacy systems, space constraints, and the need to minimize disruption to ongoing operations.
Greenfield: A greenfield refers to a new building or facility that is constructed from the ground up, with no prior infrastructure or existing systems in place. This allows for the design and implementation of automation technologies without the limitations imposed by existing structures or processes. Greenfield projects offer greater flexibility in planning, layout, and technology integration, as they aren’t constrained by pre-existing conditions.
The Benefits of Brownfield Automation
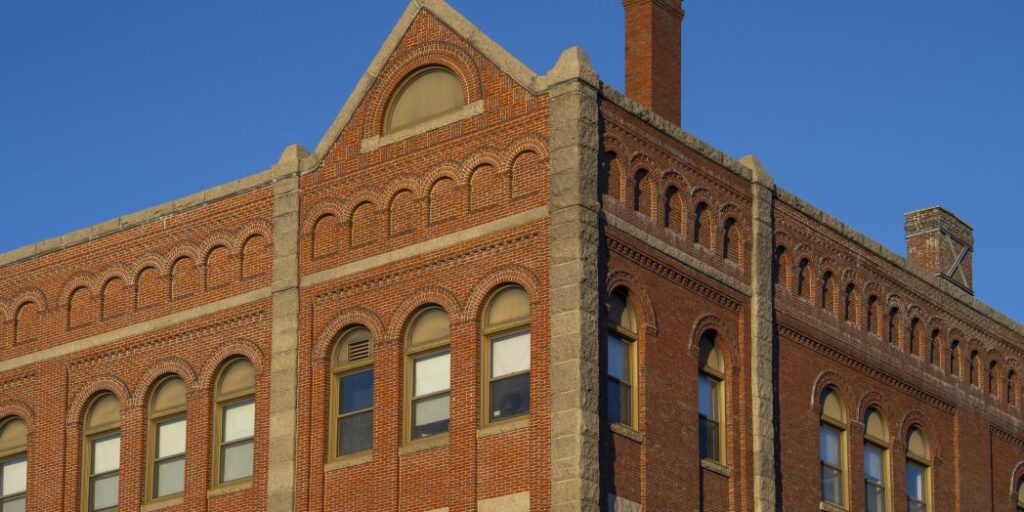
There are many benefits in selecting a brownfield operation including, a more cost-effective utilization of existing space, a reduction in disruption to ongoing operations, maintaining a familiarity with the existing environment, conserving resources, and preserving a valuable location. Below is a more in-depth look at each possible benefit.
Cost-Effective Utilization of Existing Space
One of the primary advantages of automating in a brownfield environment is the ability to utilize an existing facility. This can be a cost-effective option, as it eliminates the need to acquire new land or construct new buildings. By working within the current infrastructure, companies can allocate resources more efficiently, focusing on the necessary upgrades and automation technologies rather than on new construction.
Reduced Disruption to Ongoing Operations
In many cases, brownfield automation projects can be planned and executed in phases, allowing businesses to continue their operations while gradually integrating new technologies. This minimizes downtime and helps maintain productivity, which is especially important for companies that can’t afford extended interruptions in their workflow.
Familiarity with the Existing Environment
Operating within a known environment can simplify the automation process. Employees are already familiar with the layout, processes, and equipment, which can reduce the learning curve associated with new technologies. Additionally, existing data and performance metrics can be leveraged to inform automation decisions, ensuring that upgrades are tailored to the specific needs of the facility.
Sustainability and Resource Conservation
By opting to upgrade and automate an existing facility, companies can contribute to sustainability efforts by conserving resources. Repurposing buildings and equipment reduce the need for new materials and minimizes waste, aligning with broader environmental goals.
Preserving a Valuable Location
In some cases, businesses may be operating in locations that are strategically valuable or hold historical significance. Automating within a brownfield allows companies to preserve these locations while still modernizing their operations. This can be particularly important for industries where proximity to suppliers, customers, or transportation hubs is crucial.
The Benefits of Greenfield Automation
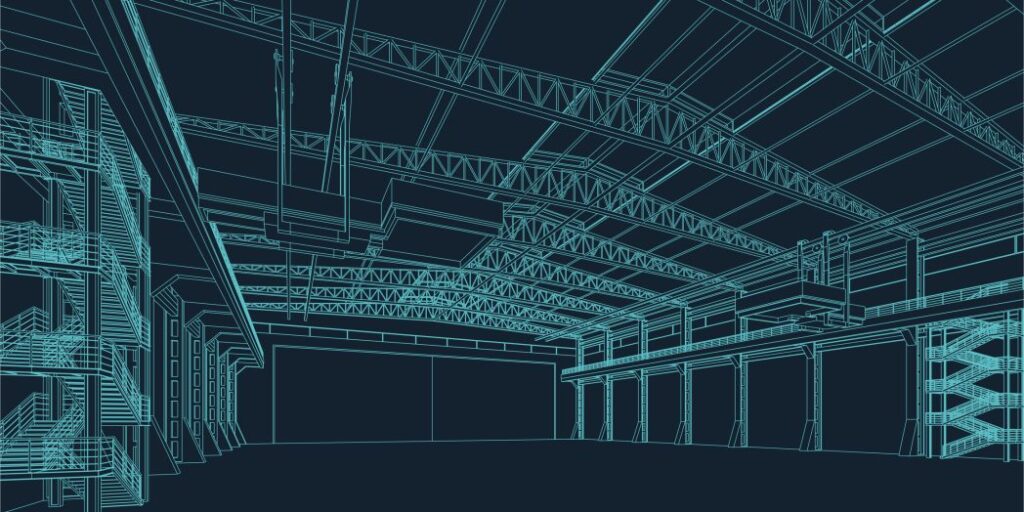
When it comes to automation, starting with a clean slate offers unique advantages. Greenfield projects provide businesses with the opportunity to design and implement systems from the ground up, free from the constraints of existing infrastructure. This approach allows for greater flexibility, innovation, and efficiency, making it an attractive option for companies looking to future-proof their operations.
Optimal Layout and Design
In a greenfield environment, companies can design the facility layout with automation in mind from the outset. This allows for the creation of streamlined workflows, optimized space utilization, and the strategic placement of equipment. By avoiding the limitations of retrofitting, businesses can ensure that their operations are as efficient and effective as possible from day one.
Integration of Advanced Technologies
With no legacy systems to work around, greenfield projects can incorporate the latest automation technologies and innovations without compromise. This not only enhances operational efficiency but also positions the company at the forefront of industry advancements. Whether it’s the integration of IoT devices, AI-driven systems, or advanced robotics, greenfield environments provide the perfect canvas for cutting-edge solutions.
Scalability and Future Expansion
Greenfield projects offer the flexibility to design facilities with future growth in mind. Companies can plan for scalability, ensuring that the infrastructure can accommodate increased production, new product lines, or additional automation technologies as the business evolves. This future-proofing approach minimizes the need for costly upgrades or reconfigurations down the line.
Customized Solutions Tailored to Business Needs
When building a new facility, businesses have the freedom to customize every aspect of the environment to meet their specific needs. This includes everything from the choice of materials and energy sources to the configuration of automation systems. By tailoring the facility to their unique requirements, companies can optimize performance and achieve a higher return on investment.
Enhanced Energy Efficiency and Sustainability
Starting from scratch allows for the incorporation of energy-efficient designs and sustainable practices from the beginning. Greenfield projects can integrate renewable energy sources, energy-efficient equipment, and environmentally friendly building materials, reducing the facility’s carbon footprint and aligning with corporate sustainability goals.
Minimized Operational Disruption
Since greenfield projects involve new construction, they avoid the disruptions associated with retrofitting or upgrading existing facilities. This means that companies can continue their current operations without interference, while the new automated facility is built and prepared for a smooth transition.
Challenges of Brownfield and Greenfield Automation
While both brownfield and greenfield automation projects offer significant benefits, they also come with their own sets of challenges. Understanding these obstacles is crucial for making informed decisions and ensuring successful implementation.
Challenges of Brownfield Automation
- Integration with Legacy Systems
One of the most significant challenges in brownfield automation is integrating new technologies with existing systems. Legacy equipment, software, and processes may not be compatible with modern automation solutions, requiring extensive modifications, custom interfaces, or even complete replacements. This can increase project complexity, costs, and timelines.
- Space Constraints and Layout Limitations
Existing facilities are often not designed with automation in mind, leading to space constraints and layout challenges. Retrofitting automation equipment into an already crowded or poorly configured space can be difficult and may require substantial reorganization or expansion. This could also result in compromises that limit the efficiency or effectiveness of the automation.
- Minimizing Disruption to Operations
Automating an active facility while minimizing disruption to ongoing operations is a delicate balancing act. Phased implementations can help, but there’s always the risk of downtime, reduced productivity, or operational bottlenecks during the transition. Planning around these disruptions requires careful coordination and may still impact overall business performance.
- Unforeseen Complications with Existing Infrastructure
Older buildings or systems may have hidden issues, such as outdated wiring, structural weaknesses, or undocumented modifications, that can complicate automation efforts. These unforeseen complications can lead to unexpected delays and additional costs, making the project more challenging to manage.
Challenges of Greenfield Automation
- Higher Initial Costs and Investment
Greenfield projects typically require a significant upfront investment. The costs of land acquisition, construction, and new equipment can be substantial. While the long-term benefits may justify these expenses, the initial financial outlay can be a barrier, especially for smaller companies or those with limited capital.
- Longer Lead Times for Construction and Implementation
Building a new facility from the ground up takes time, and greenfield projects often have longer lead times compared to brownfield projects. This extended timeline can delay the realization of benefits from automation and may not align with business needs for rapid deployment or expansion.
- Complexity in Planning and Permitting
Greenfield projects involve navigating complex planning and permitting processes, which can vary significantly depending on location and regulatory requirements. Securing the necessary approvals and ensuring compliance with environmental, safety, and zoning regulations can add time and complexity to the project.
- Risk of Over-Engineering or Under-Utilization
When designing a greenfield facility, there’s a risk of over-engineering the space or systems, leading to unnecessary costs and inefficiencies. Conversely, the facility might be under-utilized if the projected growth or production volumes are not realized, resulting in wasted resources and lower returns on investment.
- Uncertainty in Forecasting Future Needs
Greenfield projects require predicting future business needs, which can be challenging in a rapidly changing market. Misjudging future requirements can lead to a facility that is either too large or too small, potentially limiting the flexibility and scalability that greenfield projects are meant to provide.
Conclusion – Weighing the Pros and Cons of Brownfield and Greenfield Automation
When it comes to implementing automation, the decision between brownfield and greenfield environments is far from straightforward. Each approach offers its own unique set of benefits and challenges, shaped by the existing conditions and future goals of the business.
Brownfield automation provides a cost-effective way to modernize operations by leveraging existing infrastructure, minimizing disruption, and preserving strategic locations. However, it comes with the complexities of integrating with legacy systems, navigating space constraints, and dealing with potential unforeseen complications.
On the other hand, greenfield automation allows for a fresh start, offering the flexibility to design an optimal layout, incorporate the latest technologies, and plan for future scalability. Despite these advantages, the higher initial costs, longer timelines, and the risks associated with forecasting future needs can pose significant challenges.
Ultimately, the choice between brownfield and greenfield automation depends on a careful assessment of a company’s specific needs, resources, and long-term objectives. By understanding the trade-offs and opportunities each approach presents, businesses can make informed decisions that best align with their operational strategies and set the stage for sustained success in an increasingly automated world.
If you are interested in adopting automation in a Brownfield or Greenfield space and want to learn more, please reach out to me at josh.beckham@elementlogic.us or on LinkedIn.