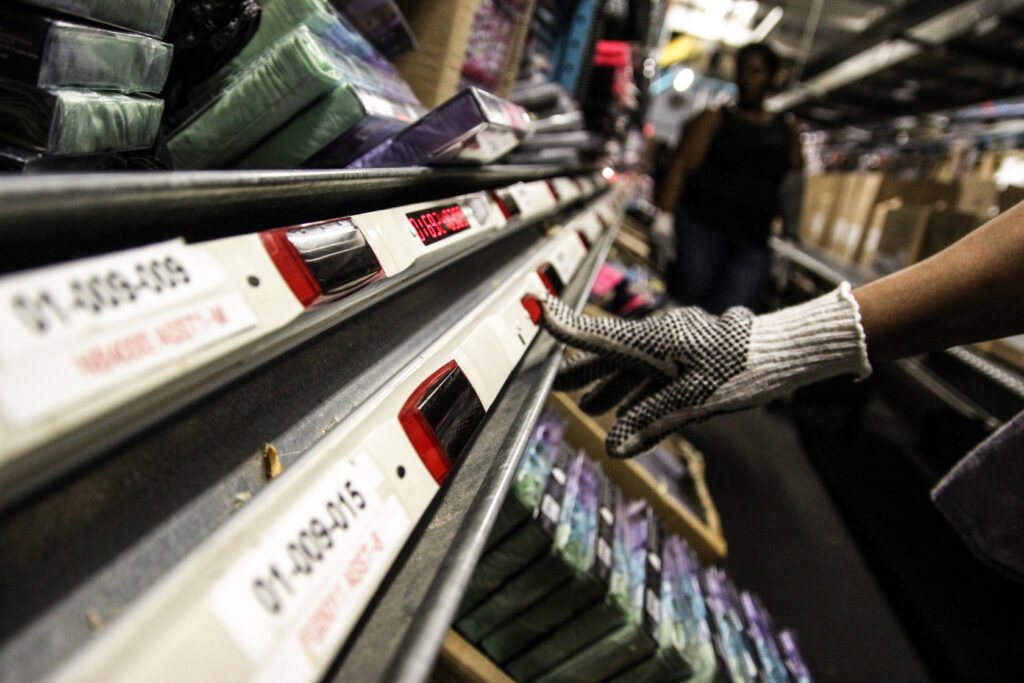
Saramax: A Put To Light Case Study
Key Highlights
The ELEMENT LOGIC Solution for Saramax
CONSULTANCY APPROACH: As part of Element Logic’s consulting approach, we analyzed the SKU and order details and provided location mapping for the existing and new pick modules–balancing the work evenly between pick zones and providing new SKU order details.
AUTOMATED SOLUTION: Implemented a Put-to-Light (PTL) system and MDR spiral incline conveyors.
ENHANCED OPERATION: The solution increased operational efficiency, performance, visibility and has added capacity and control.
THE CHALLENGE
Saramax Apparel had started to outgrow the capacity of its Pick-to-Light (PTL) tower and old conveyor system, which had earned Saramax the 2012 Walmart (DSDC) Supplier Award of Excellence. Its SKU quantity and volumes were increasing, which made the current system unsuitable for higher volume due to its poor conveyor path to shipping and lack of pick locations.
The rest of the warehouse was filled with high bay VNA racking and the shipping staging space was at a premium. Walmart told Saramax that the only way in which they were to have any confidence in the numbers being met was if they used a more sophisticated system.
Saramax needed a new multi-zoned picking system with minimal impact to the current warehouse layout while reusing most of the existing shipping conveyor system. Additionally, the new system had to be expandable at a mezzanine level and the conveyor layout pre-engineered for the future. It would require pick and pass capability between picking zones as well as a fast-track conveyor to the auditing area and shipping carousel loop, and it had to be installed without taking down the existing operation in a very aggressive schedule.
“The single biggest challenge was keeping the footprint small,” Steve Lind, VP of Distribution, said. “We needed something like Disneyland to fit into the size of a playground.”
As part of the consultancy approach, ELEMENT LOGIC analyzed the future SKUs and case data and created several system layouts that would fit within the available space, considering short distances for conveyor elevation changes, egress concerns and maintaining pallet storage location.
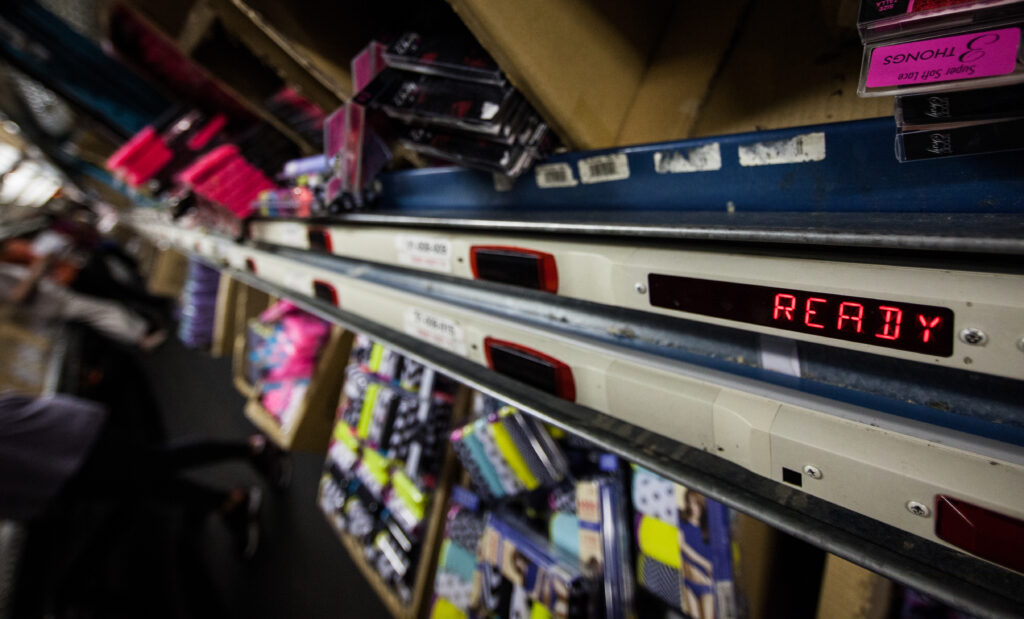
THE SOLUTION
Element Logic provided Saramax with a new 36-bay, 28ft-tall, picking module, which was pre-engineered for a second level to allow for easy future expansion. Consisting of 648 locations, the first floor has central takeaway conveyors and overhead empty-carton-removal integrated with the existing trash compactor system.
Due to short distances for elevation changes and complex paths between pick modules, the latest energy-efficient MDR spiral incline conveyors were utilized. These conveyors provide carton accumulation every 24’- 60’’, including inclines—maximizing peak rates and minimizing carton flow backup.
Element Logic consulting services analyzed the SKU and order details and provided new SKU to location mapping for the existing and new pick modules to balance workload evenly between pick zones. Keeping the highest movers on the first floor provided the easiest replenishment option.
” We increased productivity by about 500%, Lind added.
We could not have predicted that it would go as well as it did! “
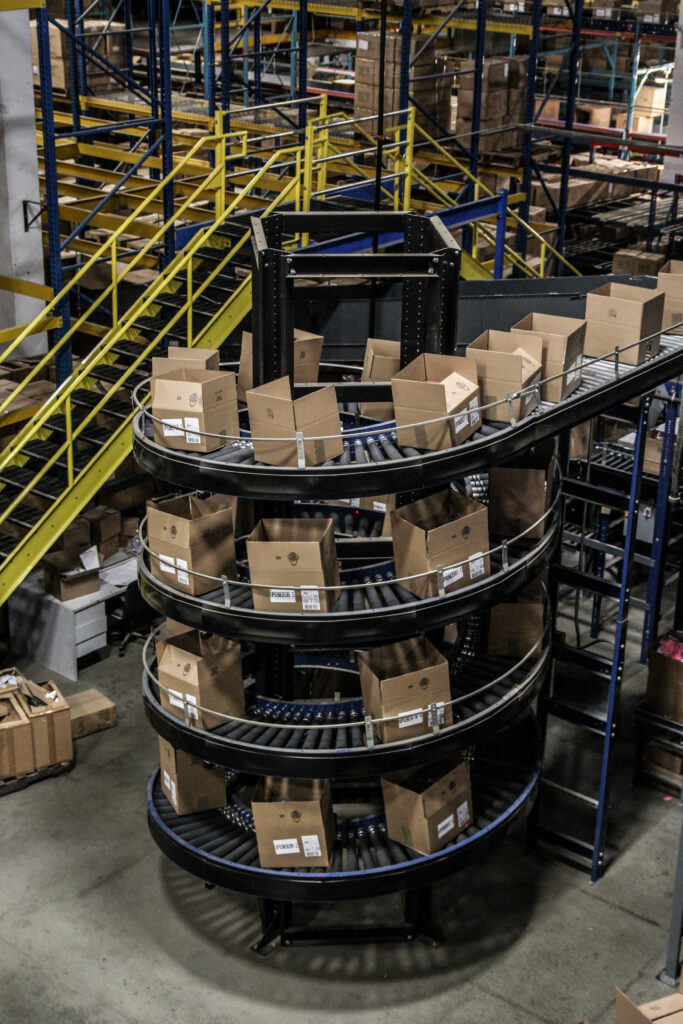
THE SYSTEM
- The new system provides Saramax with all the pick locations required and order carton routing between pick modules. Pick rates are 800 – 1100 UPH and order accuracy almost 100%
- Pre-engineering design features for the future will make expansion easy and cost-effective, while lost pallet locations have been minimized by adding overhead storage in the 28ft pick module racking.
- The PTL system provides additional fine-tuning for zones and load analysis complete with reporting pick rates by employee, zone or other criteria. Saramax utilizes the Smart Auditing functionality that keeps track of all picking transactions for each order.
ABOUT SARAMAX
Saramax Apparel is a leader in design, production, and manufacturing of intimate apparel for over 40 years.