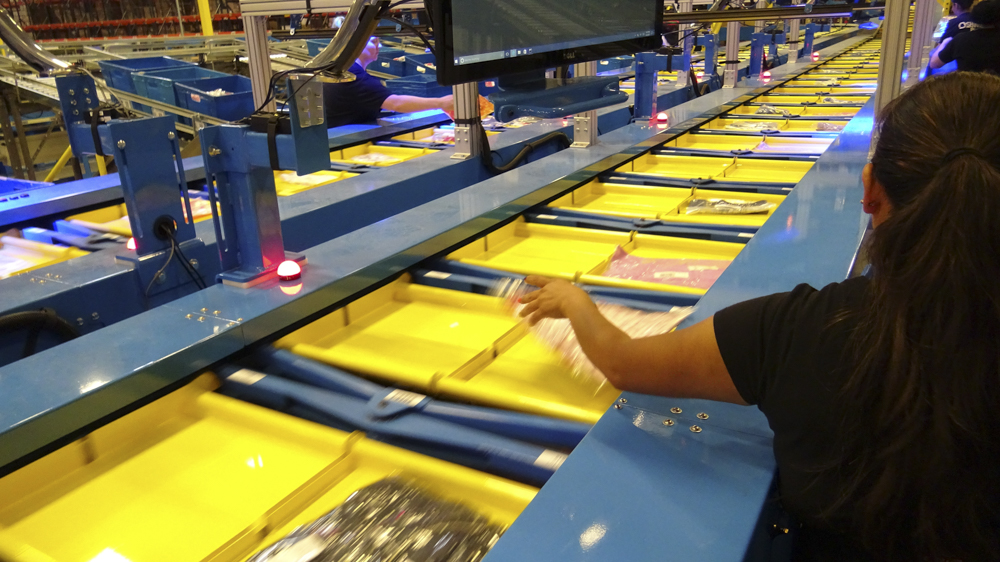
Carters Case Study
Key Highlights
The ELEMENT LOGIC Solution for Carter’s
CONSULTANCY APPROACH: As part of ELEMENT LOGIC’s consultancy approach, we analyzed the issues and limitations that needed to be addressed to meet forecasted volumes and service requirements.
AUTOMATED SOLUTION: Implemented a 600-drop dual tray SORTRAK machine.
ENHANCED OPERATION: The solution increased accuracy, space efficiency, and the throughput capacity of the DC’s Omni-Channel fulfillment.
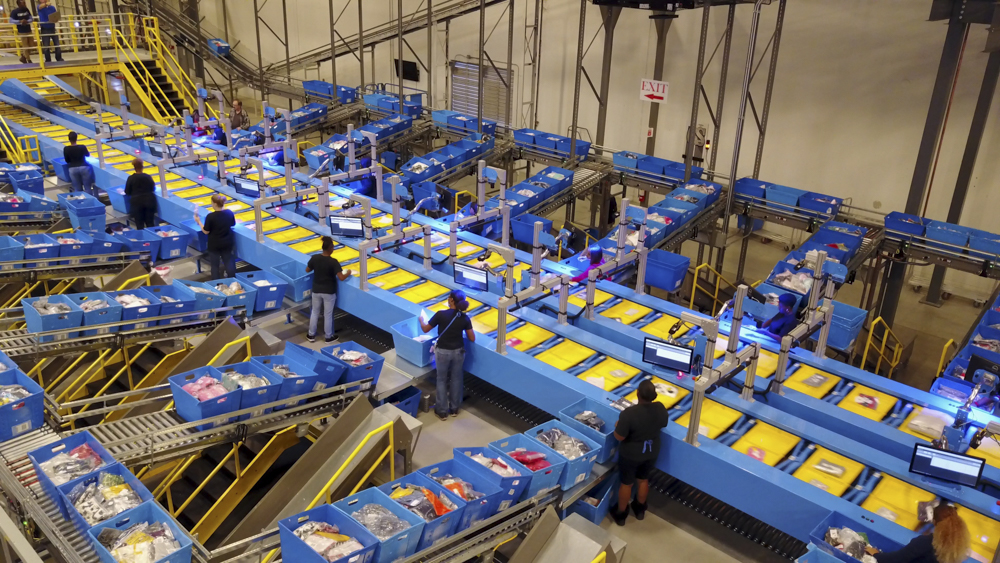
THE CHALLENGE
Carter’s has an existing distribution center in Braselton, Georgia, that uses a combination of a cross-belt sorter, shuttle system, put to store, and other automated systems to support their Omni- Channel facility. Retail store growth and increased replenishment was starting to out-grow the existing put to store automation. eCommerce also continued to grow with faster service requirements, making peak season demands more challenging. They needed a flexible sorter that could not only handle apparel, miscellaneous toys and baby products, but could also support Retail daily and adjust to eCommerce orders during peak times.
This solution needed to be delivered in seven months (before peak), with minimal room for delays and working with their specific conveyor vendor.
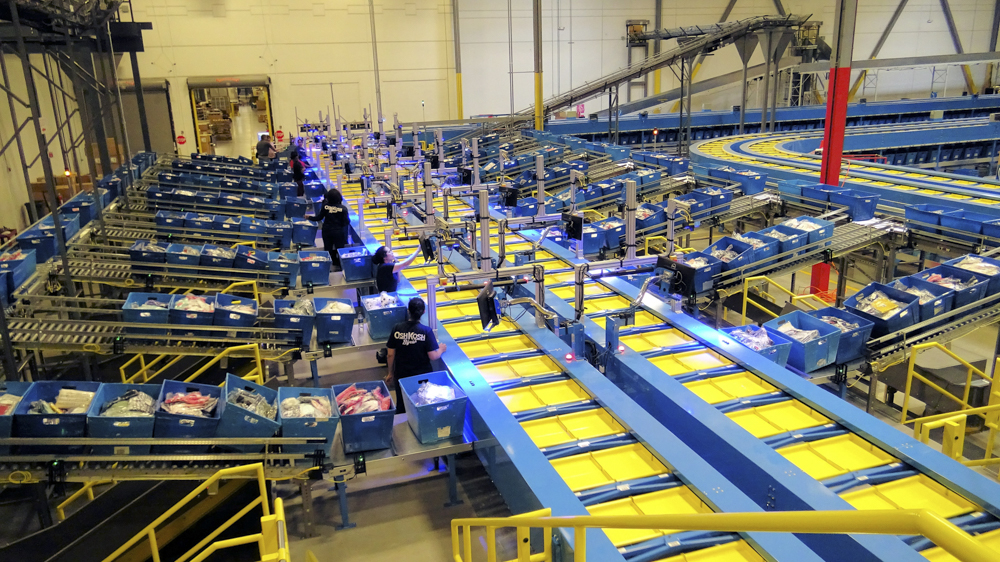
THE SOLUTION
After evaluating Carter’s business needs and budget, the best solution at the right price point was to install a 600-drop dual tray SORTRAK to handle both, retail store distribution and eCommerce order fulfilment. The SORTAK was installed within a 25,000 square foot area and integrated with Carter’s existing conveyor vendor. The system consisted of 16 induction points capable of handling various induction modes, customized sorter height, and ELEMENT LOGIC’s DCMS software that interfaced with the existing WCS and WMS.
ELEMENT LOGIC met material and manufacturing lead times and go-live by Labor Day 2017, in time for peak 2017. ELEMENT LOGIC’s project management, installation, controls and software group-maintained milestones during implementation and in partnership with the Carters PM team, ensured that there was the sorter was ready for Peak 2017.
“Simplicity of design that makes understanding process, mechanics, and systems very clear to the team,” Kelly Bryson from Carters PM team said. “We have made some software enhancements to increase chute turnover and reduce impact of miss-picks.”
THE SYSTEM
ELEMENT LOGIC provided a SORTRAK machine to increase Carter’s order fulfilment capacity and utilize 14,400 trays per hour past a single point. The flexibility in this solution provided Carter’s with multiple induction options (i.e. Scan on the Fly induction, Presentation scanning, and Batch induction), while standing out from the others and having a good ROI.
ABOUT CARTER’S
Carter’s, Inc., also known as the William Carter Company, is a major American designer and marketer of children’s apparel. It was founded in 1865 by William Carter. Carter’s acquired competitor OshKosh B’Gosh.