Will Global Supply Chain Be Automated in the Future?
The global supply chain refers to the complex network of interconnected businesses, processes, and logistics that move products across the globe.
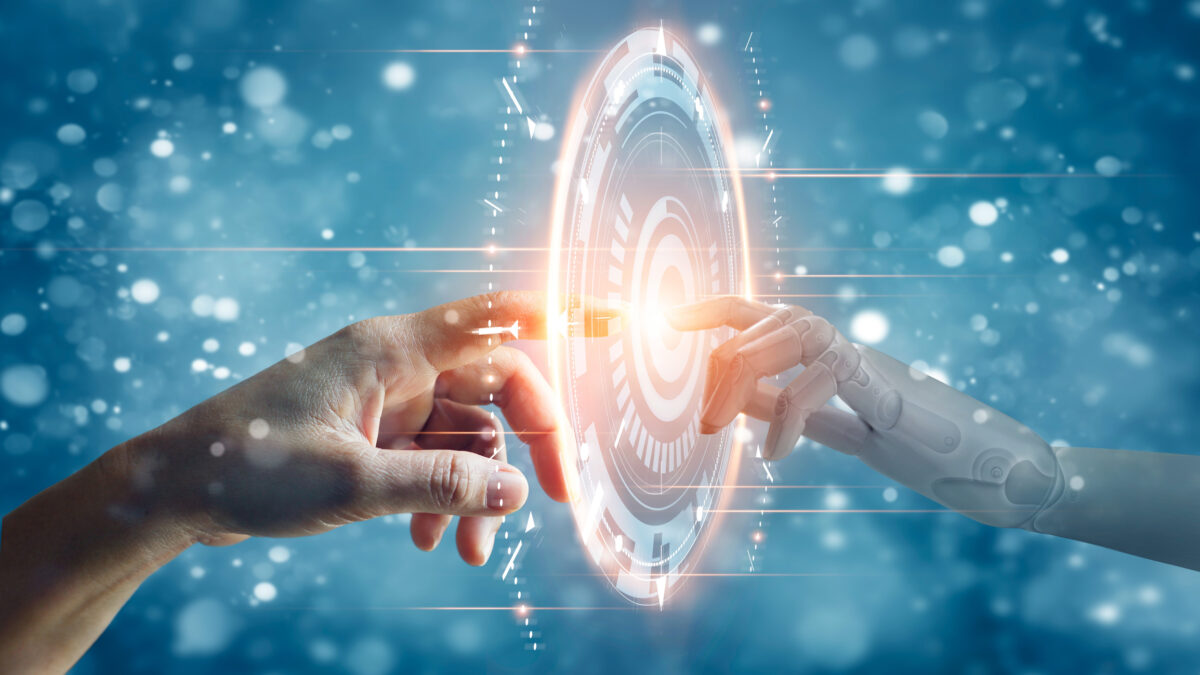
The products may range from raw materials to the end products that consumers use.
This vast system includes manufacturers, suppliers, transporters, warehouses, and retailers, all working in tandem to ensure the seamless production and distribution of goods. The global supply chain encompasses various stages such as procurement, production, transportation, warehousing, and final delivery, often spanning multiple countries and continents.
The Importance of Automation in Modern Materials Handling
Automation in modern industries and material handling involves using advanced technologies such as robotics, artificial intelligence (AI), machine learning, and the Internet of Things (IoT) to streamline and enhance various operational processes. The significance of automation in the global supply chain is multifaceted:
- Efficiency and Speed: Automation reduces the time required for tasks such as sorting, packaging, and transportation, allowing for faster processing and delivery of goods.
- Cost Reduction: By minimizing manual labor and reducing errors, automation lowers operational costs and improves profitability.
- Accuracy and Precision: Automated systems are less prone to human error, ensuring higher accuracy in inventory management, order fulfillment, and quality control.
- Scalability: Automation enables businesses to scale their operations seamlessly, accommodating increased demand without a proportional rise in labor costs.
- Safety and Working Conditions: Automated systems can handle dangerous or repetitive tasks, improving workplace safety and allowing human workers to focus on more complex and creative roles.
- Data-Driven Decision Making: Technologies like AI and IoT provide real-time data and analytics, helping businesses make informed decisions, predict trends, and optimize their supply chain operations.
Current State of Global Supply Chain Automation
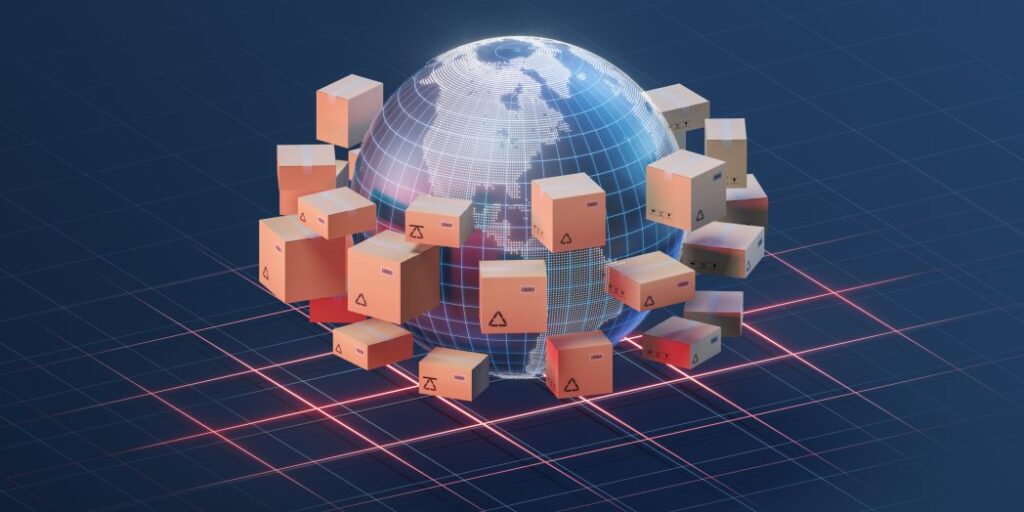
Supply chain automation has significantly evolved in recent years, integrating advanced technologies to enhance efficiency, accuracy, and responsiveness. Today, several key technologies form the backbone of supply chain automation, each contributing to different aspects of the process. Here’s an overview of the current state and the main technologies involved:
Robotics
Robotics play a pivotal role in modern supply chain automation, particularly in warehousing and fulfillment centers. These robots handle tasks such as picking, packing, sorting, and transporting goods within a warehouse. Examples include:
- Collaborative Robots (Cobots): Designed to work alongside human workers, cobots assist with repetitive or strenuous tasks, improving efficiency and reducing physical strain on workers.
- Sorting Robots: These robots automate the sorting of packages based on destination, size, and other parameters, significantly speeding up the process.
Automated Storage and Retrieval Systems (ASRS)
ASRS technologies automate the storage and retrieval of products within a warehouse, increasing storage efficiency and accuracy. One prominent example is AutoStore:
- AutoStore: This is an innovative ASRS system that uses a grid of bins and robots. Robots travel on top of the grid, retrieving and delivering bins to workstations where human operators or additional robots can pick items. AutoStore maximizes storage density and significantly reduces the footprint required for warehousing operations.
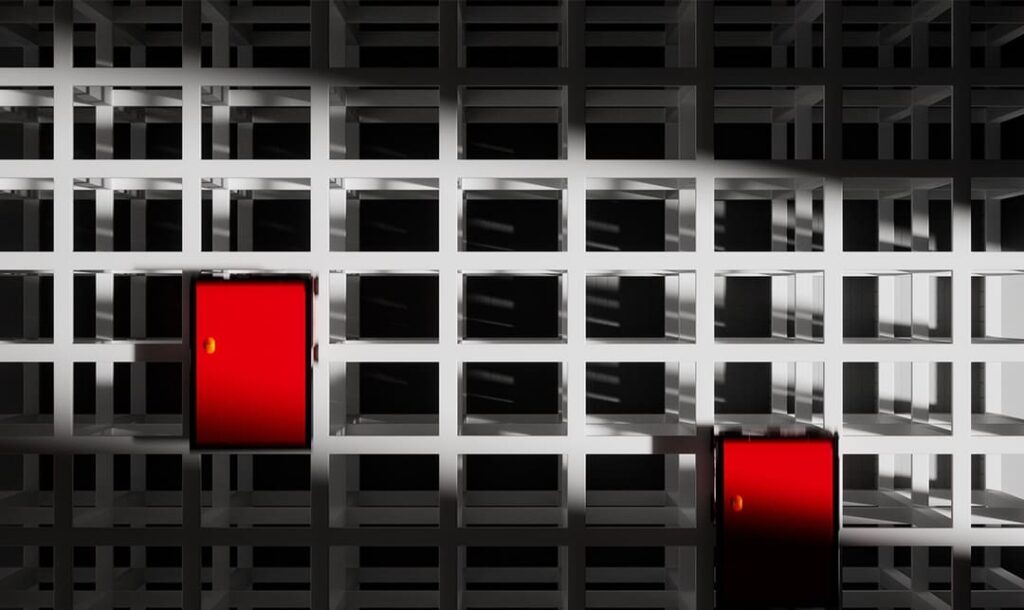
Warehouse Management Systems (WMS)
Warehouse Management Systems are sophisticated software solutions that manage and optimize warehouse operations. Key functionalities of WMS include-
- Inventory Management: Tracking inventory levels, locations, and movements in real-time.
- Order Fulfillment: Streamlining the picking, packing, and shipping processes to ensure accurate and timely deliveries.
- Labor Management: Monitoring and optimizing workforce productivity and scheduling.
- Integration with Other Systems: WMS often integrates with other enterprise systems like ERP (Enterprise Resource Planning) and TMS (Transportation Management Systems) to ensure seamless operations.
Internet of Things
The Internet of Things involves embedding sensors and connectivity in physical objects to collect and exchange data. In the context of supply chain automation, IoT has several applications:
- Real-Time Tracking: Sensors on packages, pallets, and vehicles provide real-time location and condition data, enhancing visibility and traceability throughout the supply chain.
- Predictive Maintenance: IoT devices monitor the condition of machinery and equipment, predicting maintenance needs before failures occur, thereby reducing downtime.
- Environmental Monitoring: Sensors track environmental conditions (temperature, humidity, etc.) in storage and transit, ensuring that sensitive products like pharmaceuticals and food items are kept within optimal conditions.
The current state of supply chain automation is marked by significant advancements and widespread adoption of technologies such as robotics, ASRS, WMS, and IoT. These technologies collectively enhance the efficiency, accuracy, and responsiveness of supply chain operations, paving the way for more resilient and scalable supply chains. As these technologies continue to evolve, we can expect even greater levels of automation and integration, transforming the landscape of global supply chain management.
Drivers of Supply Chain Automation
The rapid advancement and widespread adoption of supply chain automation are driven by several key factors. These drivers reflect both the changing landscape of consumer expectations and the operational challenges faced by businesses.
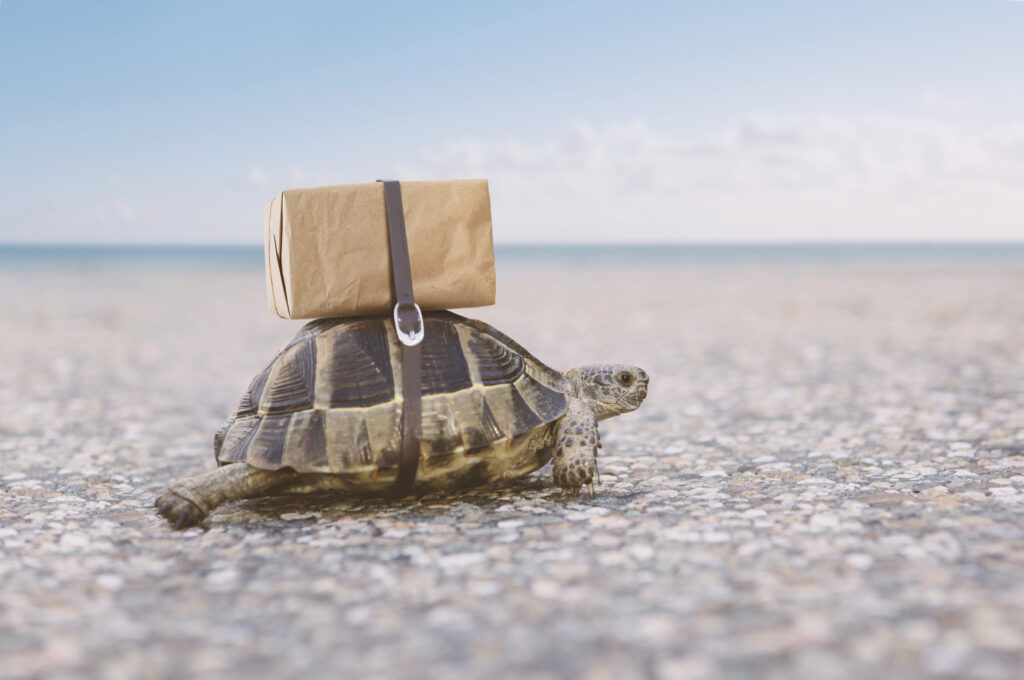
Increasing Demand for Faster Delivery Times
In the age of e-commerce and digital marketplaces, consumer expectations for rapid delivery have skyrocketed. Customers now expect same-day or next-day delivery as standard service options.
Automated systems are the answer to the customer’s increased expectations. By streamlining operations by minimizing manual intervention and optimizing processes, robots can work continuously without breaks, significantly speeding up tasks like picking, packing, and sorting.
Additionally, these same automation technologies can be coupled with IoT to provide real-time visibility into inventory and order status, enabling faster and more accurate fulfillment.
Competitive Pressure and the Need for Differentiation
In a highly competitive market, businesses must continually seek ways to differentiate themselves. Automation offers a strategic advantage by enhancing operational efficiency and customer satisfaction. Key aspects include:
- Cost Reduction: Automation reduces labor costs and minimizes errors, contributing to lower operational expenses and improved margins.
- Service Quality: Automated systems ensure consistent and high-quality service, reducing the likelihood of errors and delays. This reliability is crucial for maintaining customer trust and loyalty.
- Innovation: Implementing cutting-edge technologies positions a company as an industry leader. Being at the forefront of automation can attract tech-savvy customers and partners, creating a competitive edge.
Labor Shortages
Labor shortages are a growing challenge in many industries, particularly in warehousing and logistics. Factors such as an aging workforce, shifting job market preferences, and difficulties in attracting and retaining workers are contributing to this issue. Automation helps address labor shortages by:
- Filling the Gap: Robots and automated systems can perform tasks that are difficult to staff, ensuring continuous operation despite workforce constraints.
- Enhancing Productivity: By automating repetitive and physically demanding tasks, human workers can focus on more complex and value-added activities, improving overall productivity.
- Workforce Flexibility: Automation provides flexibility to scale operations without the need for proportional increases in workforce size, making it easier to adapt to fluctuations in demand.
The drive towards supply chain automation is fueled by the increasing demand for faster delivery times, competitive pressures, and labor shortages. These factors are pushing businesses to adopt advanced technologies that enhance efficiency, reduce costs, and improve service quality. As automation continues to evolve, it will play an even more critical role in addressing these challenges and shaping the future of global supply chain management.
Potential Automation Technologies in the Future
The future of supply chain automation is poised to be revolutionized by several cutting-edge technologies. Advanced robotics and artificial intelligence (AI) will play a pivotal role, with autonomous trucks and drones leading the charge. Autonomous trucks, equipped with AI and sophisticated sensors, will navigate and operate independently, enabling continuous operation, reducing delivery times, and cutting transportation costs while enhancing safety by minimizing human error. Drones, on the other hand, will transform last-mile delivery by swiftly transporting packages to remote or hard-to-reach areas, thus reducing traffic congestion and environmental impact.
Predictive analytics, powered by AI and machine learning, will significantly enhance demand forecasting. By analyzing historical data and identifying patterns, these technologies will provide accurate predictions of future demand trends, allowing businesses to optimize inventory levels, reduce instances of stockouts or overstock, and align production with market needs, thereby improving customer satisfaction and operational efficiency.
Blockchain technology will bring unprecedented transparency and security to supply chains. As a decentralized and immutable ledger, blockchain will ensure that all transactions and asset movements are recorded accurately and are accessible to all relevant parties. This will enhance traceability, reduce the risk of fraud and errors, and be particularly beneficial in industries requiring stringent tracking and verification, such as pharmaceuticals, food, and luxury goods.
Lastly, 3D printing, or additive manufacturing, will enable on-demand production and distribution. By creating products layer by layer from digital models, 3D printing will allow for localized and customized manufacturing, reducing the need for large inventories and long-distance transportation. This technology will enable companies to respond swiftly to market changes and customer preferences, offering greater flexibility, reducing lead times, and supporting a more efficient and adaptable supply chain.
Together, these technologies—advanced robotics and AI, predictive analytics, blockchain, and 3D printing—promise to create a more efficient, transparent, and flexible supply chain. As these innovations become more widely adopted, they will play a crucial role in shaping the future of global supply chain management, helping businesses meet evolving market demands and maintain a competitive edge in an increasingly dynamic environment.
Benefits of Full Automation in Supply Chains
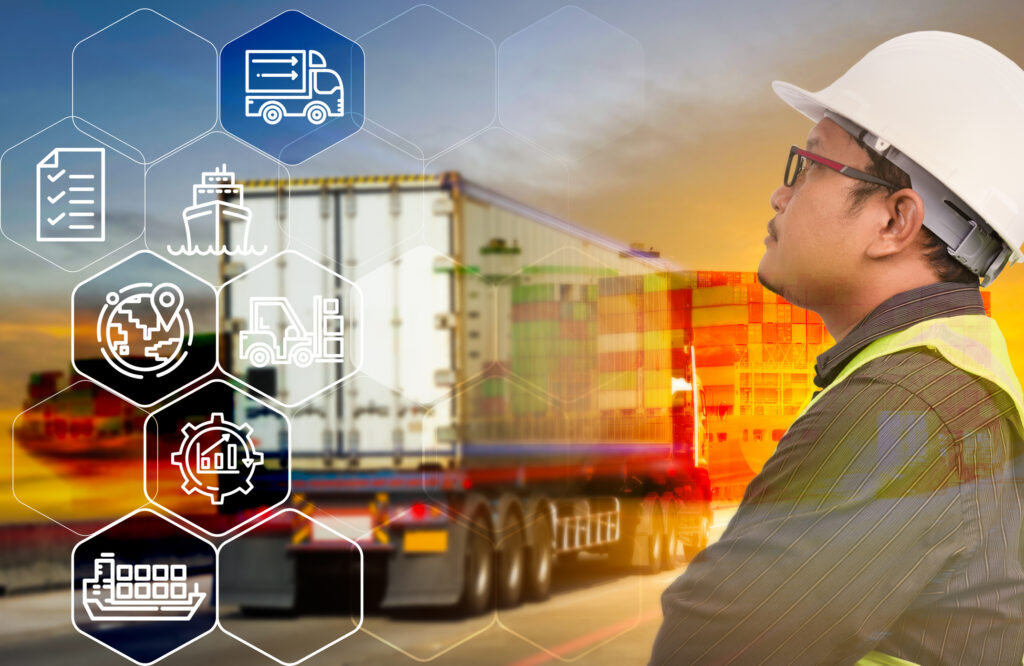
The full automation of supply chains brings a multitude of benefits that may significantly enhance operational efficiency, accuracy, and the overall adaptability of your business. Let’s review some of the key advantages you can expect to see!
- Reduction in Human Error
One of the most notable benefits of automation in supply chains is the substantial reduction in human error. Automated systems, governed by precise algorithms and real-time data, perform tasks with high accuracy and consistency. This minimizes the likelihood of mistakes that can occur due to manual processes, such as incorrect data entry, mislabeling, or picking errors. By ensuring greater accuracy in inventory management, order fulfillment, and shipping, businesses can enhance customer satisfaction and reduce the costs associated with errors and returns.
- Cost Savings Over the Long Term
While the initial investment in automation technology can be significant, the long-term cost savings are substantial. Automated systems streamline processes, increase productivity, and reduce labor costs. They also optimize resource utilization, leading to lower operational expenses. For example, automated warehouses can operate 24/7 without the need for breaks or overtime pay, and predictive maintenance enabled by automation can prevent costly equipment failures. Over time, these efficiencies translate into significant financial savings, improving the bottom line for businesses.
- Improved Safety
Automation also contributes to a safer working environment by taking over dangerous, repetitive, or physically demanding tasks. Robots and automated machinery can handle heavy lifting, hazardous materials, and work in environments that are not suitable for humans, such as extreme temperatures or high-contamination areas. This reduces the risk of workplace injuries and illnesses, leading to fewer worker compensation claims and associated costs. Additionally, enhanced safety protocols and real-time monitoring systems further ensure a secure working environment for human employees.
- Greater Flexibility
Full automation provides supply chains with remarkable flexibility and scalability. Automated systems can quickly adapt to changing demands and conditions without the need for extensive retraining or reconfiguration. For instance, automated warehouses can easily scale operations up or down in response to seasonal demand fluctuations or unexpected spikes in order volume. This flexibility allows businesses to respond swiftly to market changes, new opportunities, and disruptions, maintaining a high level of service and efficiency. Furthermore, automation facilitates the implementation of just-in-time (JIT) inventory practices, reducing the need for large stockpiles and enabling more agile and responsive supply chain management.
Challenges and Limitations
While the benefits of supply chain automation are substantial, there are also significant challenges and limitations that businesses must consider. Some of which include the high initial investment costs, the possibility of technical issues arising or having challenges with the initial integration with your existing system, the risks surrounding data privacy and cyber security, as well as ensuring that your business meetings or succeeds regulations standards.
High Initial Investment
One of the most prominent barriers to adopting full automation in supply chains is the high initial investment required. The cost of acquiring, installing, and configuring advanced technologies such as robotics, AI systems, IoT devices, and automated storage solutions can be substantial. This financial commitment includes not only the purchase of equipment but also the expenses associated with training staff, upgrading infrastructure, and maintaining these systems. For small and medium-sized enterprises (SMEs), these costs can be particularly prohibitive, making it difficult to compete with larger companies that have greater financial resources.
Possible Technical Issues and Integration Challenges
Implementing automation in supply chains often involves complex technical challenges and integration issues. Automated systems need to seamlessly integrate with existing processes, legacy systems, and enterprise resource planning (ERP) software. Achieving this integration can be technically challenging and time-consuming, requiring specialized expertise. Additionally, technical issues such as software bugs, hardware malfunctions, and connectivity problems can arise, potentially disrupting operations and causing delays. Ensuring that all components of the automated system work together harmoniously is critical to avoiding inefficiencies and maximizing the benefits of automation.
Cybersecurity Risks and Data Privacy Concerns
As supply chains become more automated and interconnected, they also become more vulnerable to cybersecurity threats. Automated systems often rely on vast amounts of data and networked devices, making them attractive targets for cyberattacks. Protecting sensitive information and ensuring the integrity of data across the supply chain is a significant challenge. Businesses must invest in robust cybersecurity measures to safeguard against data breaches, hacking, and other cyber threats, which adds to the overall cost and complexity of implementing automation.
Regulatory and Compliance Hurdles
Compliance with industry regulations and standards is another challenge associated with supply chain automation. Different industries and regions have specific regulatory requirements that automated systems must meet. For example, in sectors like pharmaceuticals and food, there are stringent guidelines for traceability, safety, and quality control. Ensuring that automated systems comply with these regulations requires careful planning, continuous monitoring, and potentially significant adjustments to automated processes.
Addressing these challenges requires careful planning, substantial financial resources, and a strategic approach to implementation. By understanding and mitigating these limitations, companies can more effectively harness the power of automation to enhance their supply chain operations and achieve long-term success.
The Bright Future!
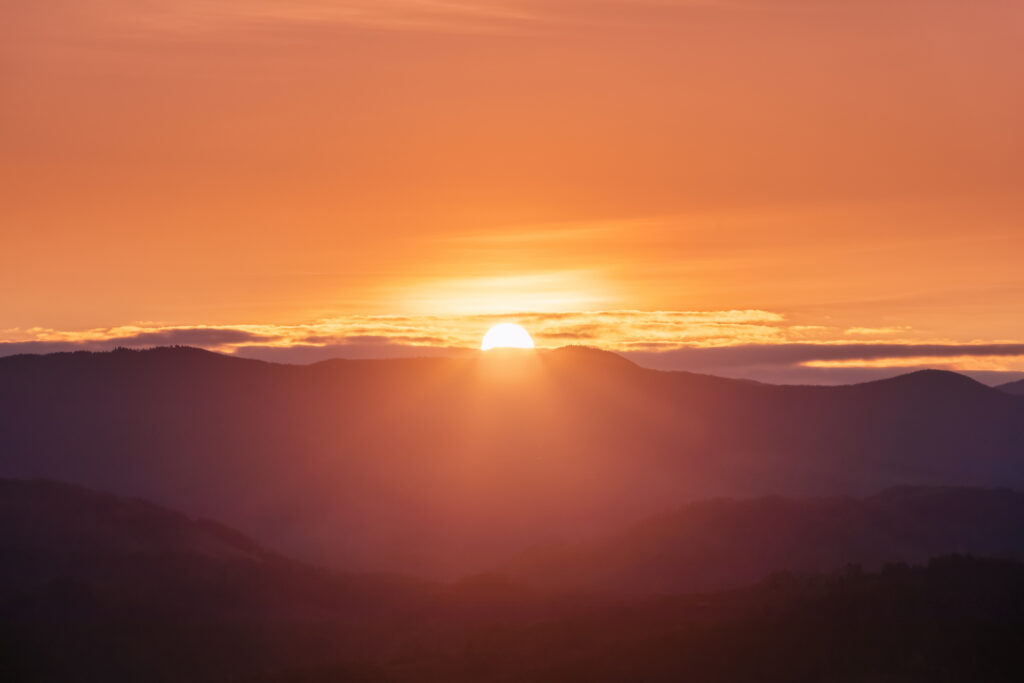
The future of supply chain automation is bright, with continuous advancements expected to further revolutionize the industry. Emerging technologies such as quantum computing and advanced AI will likely play pivotal roles in enhancing the capabilities and efficiency of automated systems. Quantum computing promises to solve complex optimization problems at unprecedented speeds, potentially transforming logistics and supply chain planning. Edge computing, by processing data closer to the source, will enable real-time decision-making and reduce latency in automated systems.
Furthermore, advancements in AI will continue to drive predictive analytics and machine learning, allowing for more accurate demand forecasting, inventory management, and dynamic supply chain adjustments. The integration of blockchain technology is anticipated to become more widespread, providing enhanced transparency, security, and trust across the entire supply chain network.
3D printing is set to further disrupt traditional manufacturing and distribution models by enabling localized and on-demand production, reducing lead times, and minimizing the need for large inventories. This will be particularly beneficial for industries that require rapid prototyping and customization.
Collaboration between humans and machines is also expected to evolve, with collaborative robots becoming more prevalent in warehouses and manufacturing plants. These collaborative robots will work alongside human workers, complementing their capabilities and increasing overall productivity.
Conclusion
The automation of supply chains holds immense potential for transforming the way businesses operate, offering significant benefits such as reduced human error, long-term cost savings, improved safety, and greater flexibility. However, it is essential to recognize the challenges and limitations, including high initial investments, technical and integration issues, cybersecurity risks, workforce impact, and regulatory compliance.
As we look to the future, the continued advancement and adoption of technologies such as advanced robotics, AI, predictive analytics, blockchain, and 3D printing will drive the evolution of supply chains. Businesses that proactively embrace these innovations and strategically address the associated challenges will be well-positioned to thrive in an increasingly competitive and dynamic market.
Ultimately, the successful implementation of supply chain automation will require a balanced approach that leverages technological advancements while addressing the human and regulatory aspects. By doing so, companies can create more resilient, efficient, and responsive supply chains, ensuring long-term sustainability and growth in the global economy.