Warehouse Tips for Perishable Inventory Management
The effective management of perishable inventory within warehouses has become paramount for businesses across industries as consumer demands for freshness and quality continue to skyrocket.
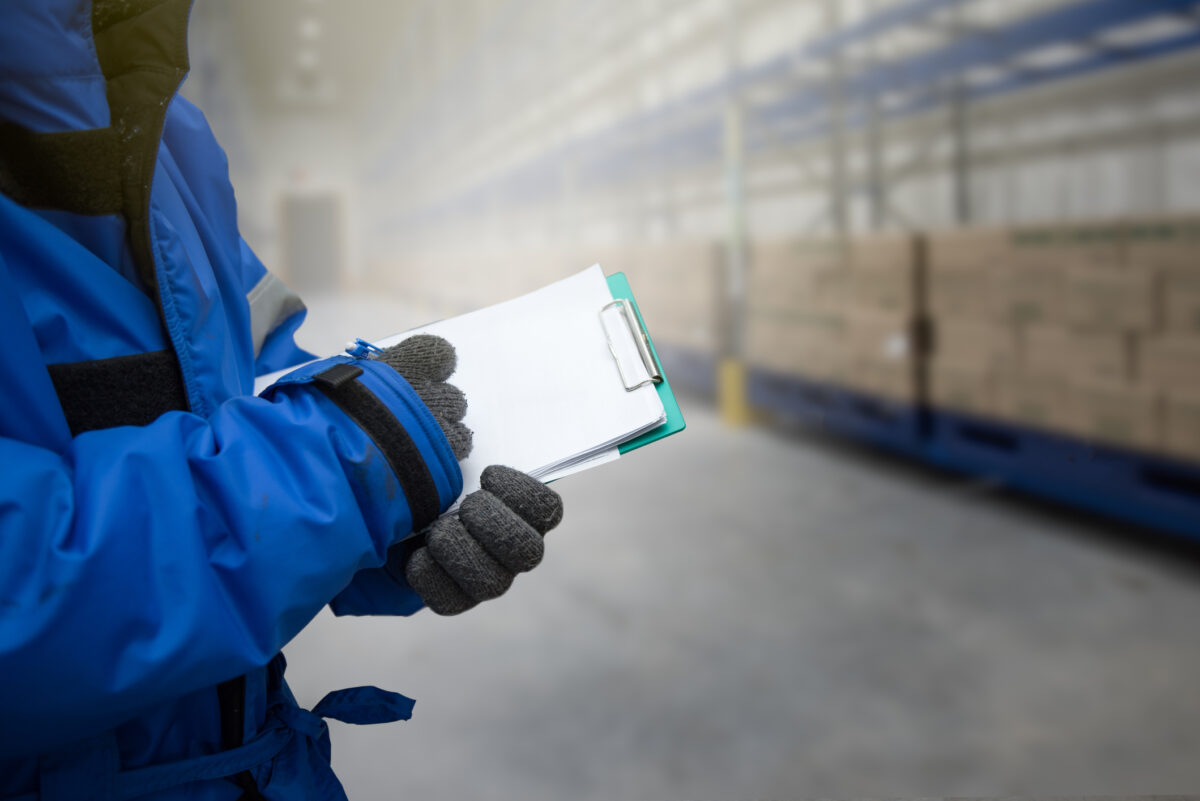
Whether you are dealing with fresh produce, dairy products, or other time-sensitive goods, maintaining the integrity of perishable items from the moment they enter the warehouse to the point of reaching the consumer is a delicate balancing act.
As the lifeline between manufacturers and consumers, warehouses play a pivotal role in ensuring that products not only meet but exceed customer expectations for freshness. With the advent of cutting-edge technologies like AutoStore, warehouses now have a powerful arsenal at their disposal to uphold the quality of perishable goods.
The Challenge of Perishable Goods
Perishable goods present a unique set of challenges for warehouses, largely in part because they require meticulous attention to detail and a firm commitment to maintaining industry standards. Let’s dissect the 3 primary factors of handling these time-sensitive items and explore what warehouse managers must contend with to ensure the freshness and quality of perishable goods.
Adherence to Industry Standards
Handling perishable goods with precision to comply with stringent industry standards is of the utmost importance. This includes following all the guidelines set by regulatory bodies to guarantee the safety and quality of the products. Additionally, warehouse staff must be well-versed in the specific requirements for each type of perishable item, from fresh produce to dairy and beyond.
Preserving Freshness
Undoubtedly one of the most prevalent challenges with perishable goods lies in preserving their freshness, from the moment that they arrive at the warehouse to the time it takes for them to reach the end consumer.
Some strategies for maintaining freshness may involve having an efficient inventory turnover, streamlining your supply chain processes, and adopting technologies that extend the shelf life of these goods. Some of the technologies include advanced monitoring systems that allow real-time tracking of environmental conditions, ensuring that temperature and humidity levels are consistently maintained within optimal ranges.
Environmental Factors
As touched on above, temperature and humidity are critical factors that can significantly impact the quality and shelf life of perishable items. Warehouses must invest in suitable storage solutions, including refrigeration and climate-controlled areas, to mitigate the effects of temperature variations.
Another environmental factor to consider which may not come to mind immediately is external contaminants, both biological and chemical. Contaminants pose a constant threat to perishable goods, which is why stringent cleanliness and hygiene protocols must be established and adhered to in warehouses to prevent contamination.
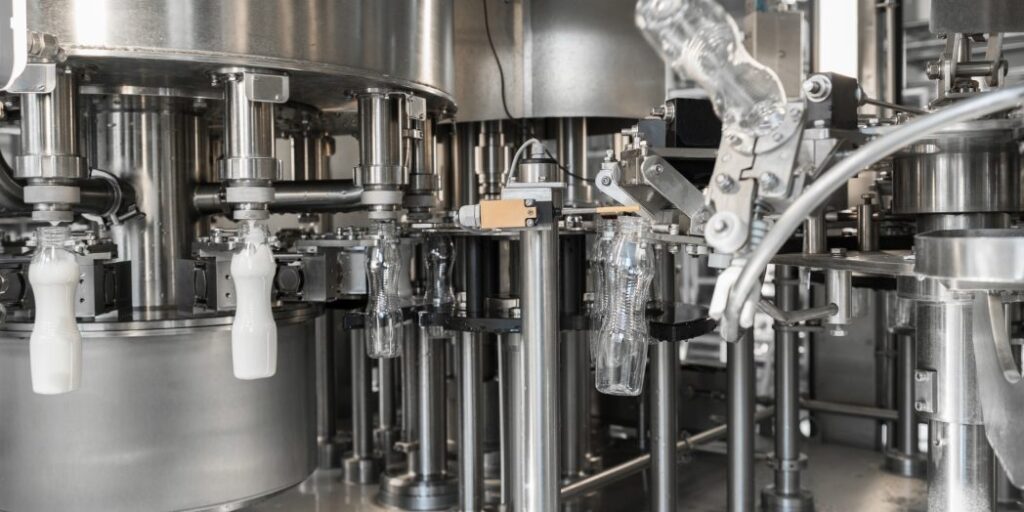
Warehouse Storage for Perishable Goods
Efficient storage is a cornerstone of successful perishable inventory management in warehouses, without it you are doomed to fail. The way perishable goods are stored can have a profound impact on their freshness, shelf life, and overall quality. The three most common storage methods we will discuss are Full Pallet Storage, Case Storage, and Mobile Pallet Racking.
- Full Pallet Storage: a traditional method where entire pallets of perishable goods are stored together. This approach is commonly used for items that have a consistent shelf life and uniform storage requirements.
Benefits:
- Facilitates quick and easy inventory management as products are stored in bulk.
- Ideal for goods with similar temperature and humidity requirements, ensuring uniform storage conditions.
- Case Storage: involves the breaking down of pallets into individual cases or cartons for storage. This method is suitable for perishable goods with different shelf lives or storage requirements.
Benefits:
- Allows for greater flexibility in managing diverse product ranges with varying storage needs.
- Enables better control over inventory turnover, reducing the risk of items reaching their expiration dates.
- Facilitates more accurate picking and packing processes, enhancing overall warehouse efficiency.
- Mobile Pallet Racking: a dynamic storage solution that uses adjustable racks mounted on guided tracks. This method maximizes space utilization by compacting storage when not in use.
Benefits:
- Enhances storage capacity by eliminating fixed aisles, making it suitable for warehouses with limited space.
- Offers improved accessibility to goods as racks can be moved to create open aisles for picking.
- Enables better temperature control as the system can be integrated with climate-controlled storage areas.
How Automation Can Ensure Freshness
In the realm of perishable goods warehousing, where precision and efficiency are paramount, Automated Storage and Retrieval Systems (ASRS) emerge as a game-changing technology. ASRS, like AutoStore, not only elevates the standard of freshness maintenance but also addresses key challenges associated with perishable inventory management.
Here are 6 benefits that ASRS systems, such as AutoStore, can offer to ensure the freshness of your perishable goods.
The first benefit that AutoStore can offer your warehouse is precise temperature control. ASRS systems can be integrated with advanced climate control mechanisms, providing precise temperature regulation for storage areas. This is crucial for preserving the freshness of perishable items, as even slight deviations from optimal temperatures can lead to spoilage on a grand scale.
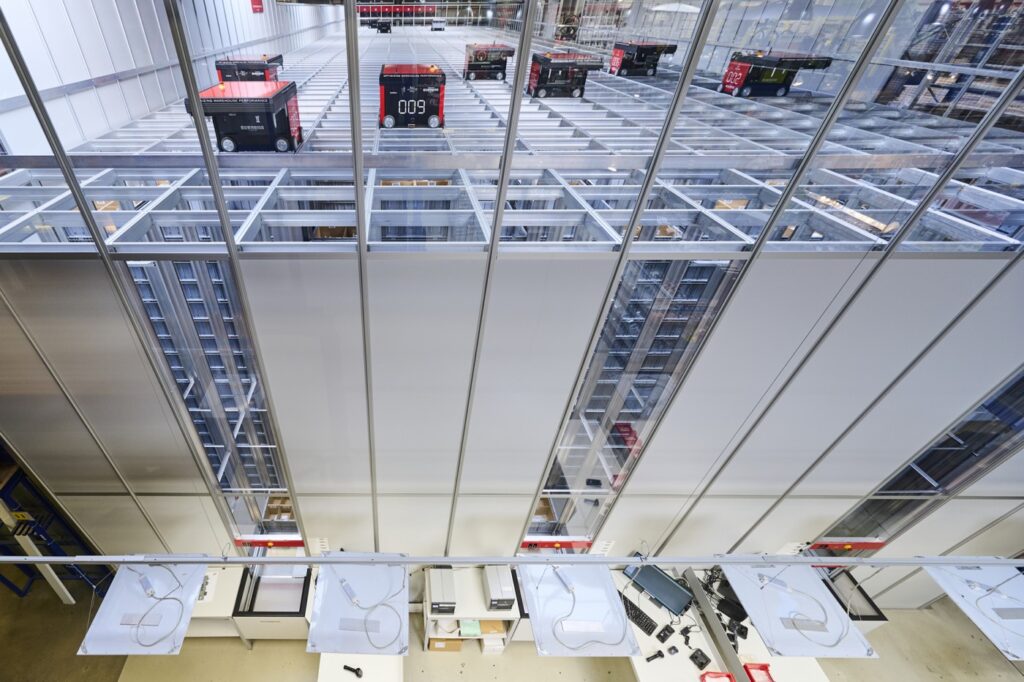
Secondly, AutoStore’s systems automate the retrieval of items based on the First-In, First-Out (FIFO) principles which are a fundamental part of perishable goods warehousing. FIFO ensures that products are used or shipped in the order they are received, minimizing the risk of products reaching their expiration dates while still in storage. By systematically accessing and retrieving the oldest items first, the risk of perishable goods expiring in the warehouse is significantly reduced.
Utilizing AutoStore within your perishable goods warehousing operation will greatly reduce human handling interactions and, most importantly, the errors that come with it. By reducing the reliance on human labor, businesses can also address the challenges of retrieving items from extremely cold storage environments, enhancing safety for warehouse personnel.
Additionally, incorporating an ASRS system in your warehouse operation will minimize waste by using precise temperature control, FIFO inventory management, and reducing human handling. By ensuring that perishable goods are handled correctly and efficiently, the risk of products going to waste due to spoilage is significantly reduced, translating to cost savings.
Finally, ASRS systems excel in providing rapid retrieval of items. The efficiency of the retrieval process ensures that products move quickly through the warehouse, reducing the time perishable goods spend in storage and enhancing overall freshness.
ASRS Considerations for Perishable Goods
While Automated Storage and Retrieval Systems (ASRS) bring a plethora of advantages to perishable goods warehousing, their seamless integration requires careful consideration of various factors. Implementing automation is a strategic decision that can revolutionize warehouse operations, but it’s essential to navigate potential challenges and ensure a smooth transition. Here are key considerations for warehouses contemplating the adoption of ASRS for handling perishable goods:
- Compatibility with Legacy Systems:
- Warehouses often operate with existing legacy systems that manage inventory, orders, and other critical processes. Compatibility between these legacy systems and ASRS is crucial for a cohesive and efficient workflow.
- Upgrading or integrating ASRS with existing systems may pose challenges, and it’s imperative to evaluate the compatibility and invest in necessary upgrades or modifications.
- Workflow Design for Perishable Goods:
- The implementation of ASRS necessitates a re-evaluation and redesign of workflows, particularly when it comes to handling perishable goods. New processes must be established to align with the capabilities of the automated system.
- Considerations should include how perishable items will be stored, retrieved, and moved within the warehouse. Creating a workflow that optimizes the benefits of ASRS for freshness while maintaining efficiency is key.
- Employee Training:
- Transitioning to an automated system requires comprehensive training for warehouse staff. Employees must be familiar with the operation, maintenance, and troubleshooting of ASRS to ensure its effective utilization.
- Specialized training programs should be developed to address the unique aspects of handling perishable goods within the automated system, emphasizing the importance of maintaining optimal storage conditions.
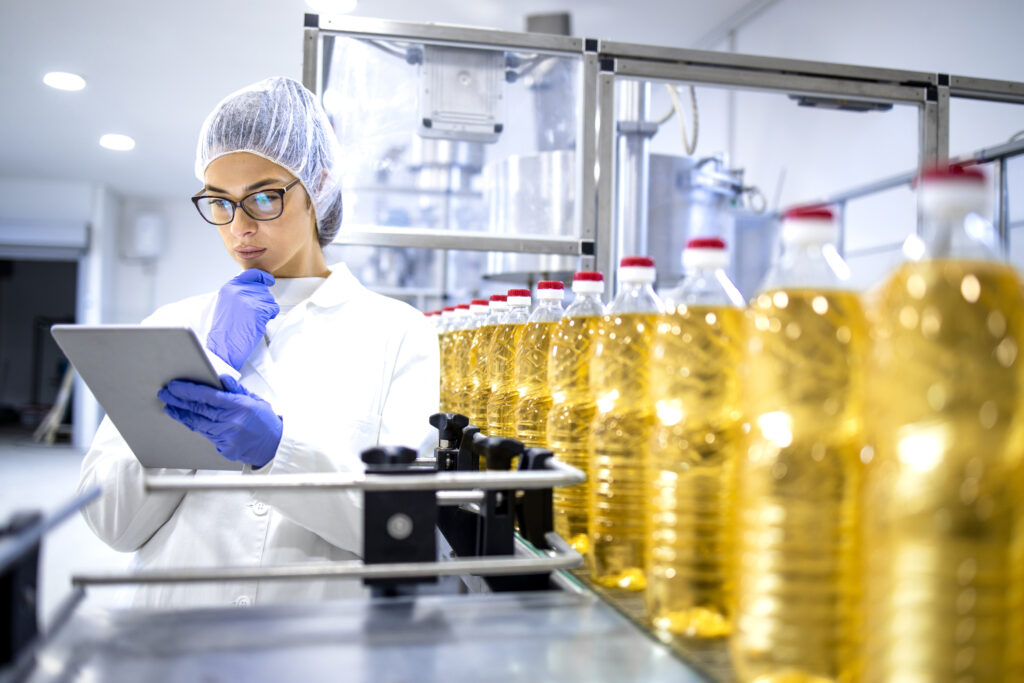
- Cost-Benefit Analysis:
- Assessing the cost-effectiveness of implementing ASRS is essential. While automation offers long-term benefits, there are upfront costs associated with installation, training, and potential system modifications.
- Conduct a thorough cost-benefit analysis to determine the return on investment (ROI) and evaluate whether the advantages, such as reduced waste and increased efficiency, justify the initial expenses.
- Scalability and Flexibility:
- Consider the scalability and flexibility of the chosen ASRS solution. The warehouse’s needs may evolve over time, and the system should accommodate changes in inventory volume, product variety, and operational requirements.
- Opt-in for a solution that allows for easy scalability and adjustments to meet future demands without significant disruptions.
- Maintenance and Support:
- Regular maintenance is crucial for the optimal performance of ASRS. Ensure that there is a robust maintenance plan in place, including routine inspections and prompt repairs.
- Establish a relationship with the system provider for ongoing support and updates, ensuring that the technology remains aligned with industry standards and evolving best practices.
Conclusion
While the prospect of implementing ASRS in a perishable goods warehouse is exciting, a thoughtful and thorough approach is essential to overcome potential challenges. By addressing compatibility issues, designing effective workflows, providing adequate training, conducting a cost-benefit analysis, ensuring scalability, and establishing maintenance protocols, warehouses are given the tools to maximize the benefits of automation and elevate their capabilities in managing perishable inventory.
For a deeper exploration of the many benefits and the challenges in warehouse automation, you may also refer to our whitepaper “Cost vs Benefit in Warehouse Automation: Calculate Your ROI with Element Logic”.