Warehouse Management Tips for the Holidays
The winter holidays are notoriously the busiest season of the year for warehouses. While the potential for increasing revenue is high, there’s also the challenge of efficiently managing inflated inventory levels, high-volume order fulfillment, and the risk of equipment malfunctions. In order to capitalize on holiday profits, it’s critical that warehouses overcome these challenges to operate efficiently.
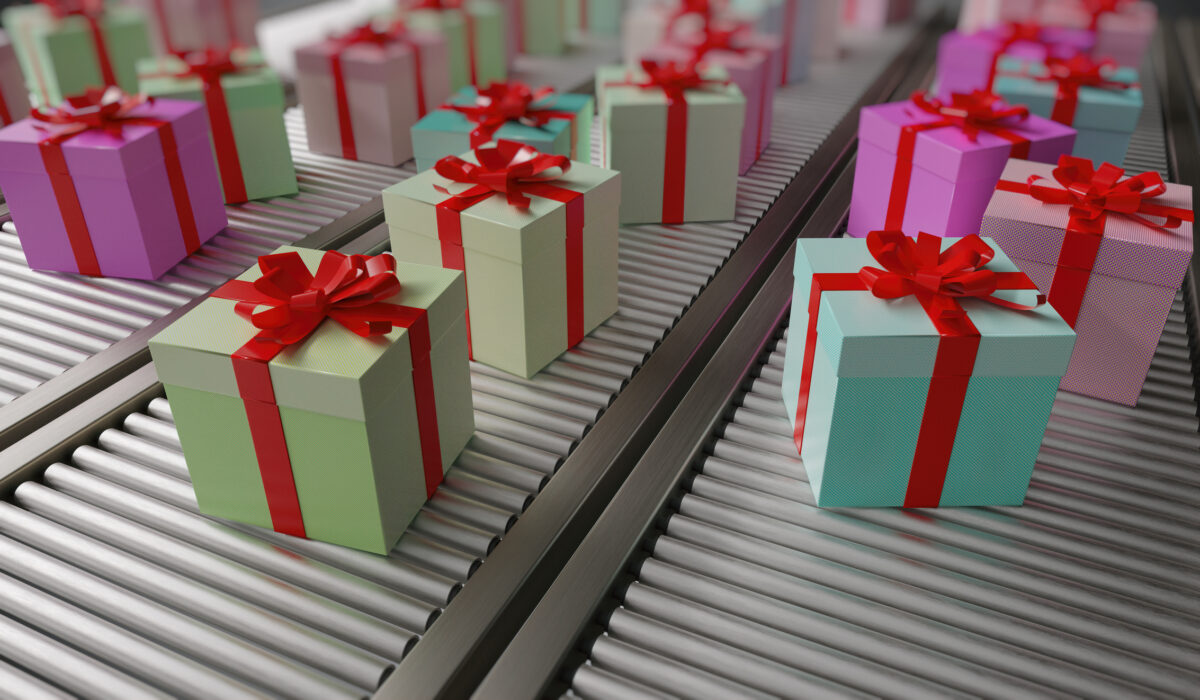
However, warehouse management during the holidays doesn’t need to be stressful. In this blog, we will cover several tips to help warehouse managers maximize efficiency, productivity, and ultimately, profits for a successful holiday season.
Hire Seasonal Employees
With a spike in warehouse workload during the holiday season, it’s essential to maintain a well-staffed warehouse. An understaffed warehouse is prone to costly problems including inventory errors, delayed order fulfillment, employee burnout, overtime costs, and more. These issues are detrimental to warehouse productivity and can be damaging to your bottom line.
Hiring seasonal employees is an effective way to meet this increasing demand. Not only will seasonal employees help reduce burnout, but the additional workers will ensure productivity, minimize avoidable errors, and limit expensive overtime hours. With more hands on deck, high volumes of orders can be processed quicker and go out faster. This expeditious turnaround time will please your customers and help make the holiday season a success.
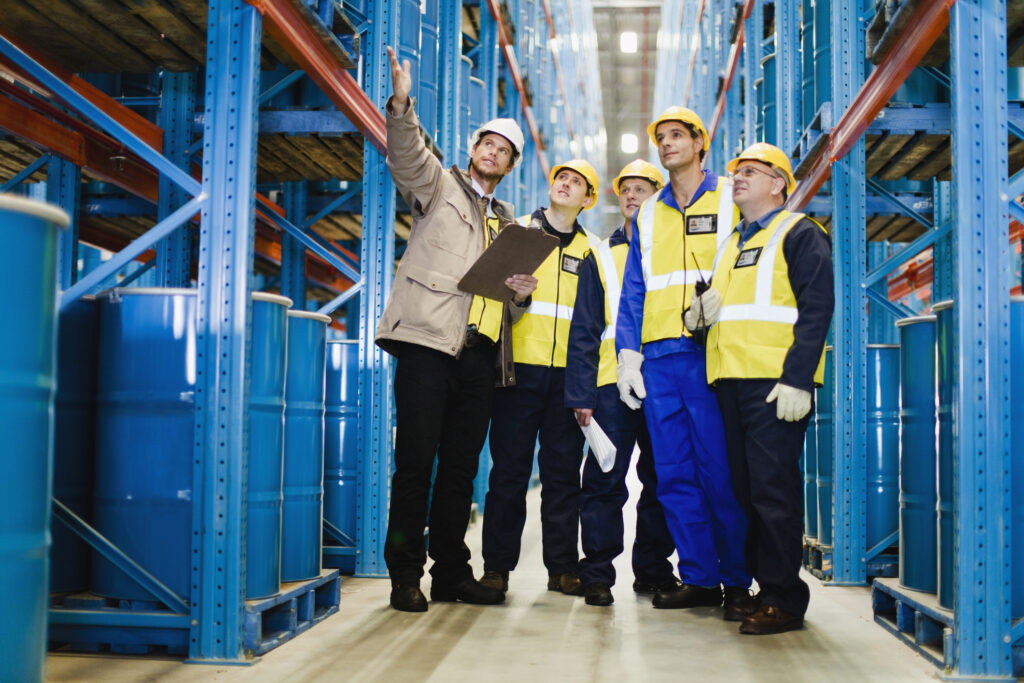
Make Sure All Employees Are Properly Trained & Scheduled
While increased staff levels are beneficial to warehouse operations in the peak season, this is only true if the staff is well-trained and properly scheduled. Both seasonal and full-time employees must be scheduled efficiently and prepared for seasonal warehouse workflows. Let’s review tips for training and scheduling during this time.
- Training Warehouse Staff: Comprehensive and timely training is important for effective warehouse management. All employees, both seasonal and full-time, should be trained on the proper warehouse procedures, including how to use the warehouse equipment and identify if there is an issue with equipment functionality. The holiday season is not the time to start brand-new training, ideally, training takes place ahead of time. Likewise, this means hiring seasonal workers far enough in advance to ensure there is adequate time to complete warehouse training. With all of your workers being properly trained and certified, your warehouse will be prepped for handling the busy holiday workload.
- Scheduling Warehouse Staff: Maintaining an optimized and flexible warehouse schedule will be vital to keeping your operations running smoothly. That being said, scheduling during the holidays can be complex with changing availability, sickness, and a fluctuating workforce. Investing in scheduling optimization software is a great way to ensure that there is visibility and flexibility into warehouse schedules. For instance, scheduling software that operates in real-time can sort out last-minute changes in availability and optimize the warehouse schedules to guarantee there are always qualified employees on the floor.
Evaluate Your Warehouse Layout
Unorganized warehouse layouts can cause inefficiencies, slowing down time sensitive workflows. This is especially true when your warehouse is housing more products and workers during the busy holiday season. Before the holidays, warehouse managers should audit the warehouse layout and flow of operations to better understand the root cause of inefficiencies. By rearranging workstations, removing obstacles, and streamlining maneuverability, warehouses will be prepped for handling the influx of activity. In addition, warehouse managers should consider separating machinery operations and pedestrian traffic to ensure safe and efficient traffic flow.
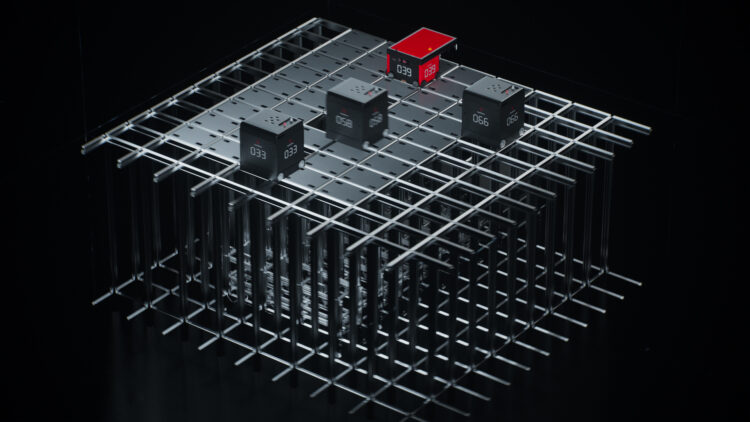
Use Technology To Your Advantage
Technology is an easy way to upgrade your warehouse management. With an advanced warehouse management system, time-consuming workflows like sorting, picking, and transporting can be automated. For instance, robotic systems like the AutoStore Automated Storage and Retrieval System (ASRS), can pick and pack more orders per hour while reducing inventory errors and available floor space. With faster turnaround times and more accurate order fulfillment, your warehouse will be prepared to scale operations during peak season.
There are several innovative warehouse management technologies to help you scale efficiently depending on your unique business needs. Diverse types of sortation equipment can help to streamline sorting operations for products of varying sizes. Goods to person technology can optimize product picking and inventory storage. However, warehouse managers should consider investing in new warehouse technologies before the holiday season starts. This will allow for adequate time to train employees on the equipment and adjust to the new workflows before there is additional pressure on your timelines and supply chain.
Prepare Adequate Inventory Levels

Inventory management is a critical aspect of managing a warehouse, but it is notoriously difficult during the holiday season, especially with ongoing supply chain issues. Warehouse technology can help to improve inventory management, keeping accurate inventory records regardless of complexities caused by returns or exchanges.
In addition to investing in technology that maintains accurate inventory levels, warehouse managers should also use data analytics. Analyzing inventory data from previous holiday seasons can help to forecast potential inventory fluctuations for the coming year. This will help to ensure that you can provide customers with the products they want to purchase from you this holiday season.
Acquire Extra Warehouse Equipment If Needed
As warehouses take on increasing inventory levels and high-volume orders, it’s essential that there is adequate equipment available to get the job done. With access to the right equipment, your warehouse operations won’t be forced to slow down, and instead will be positioned to scale with holiday demand. If your warehouse is not in a position to outright purchase new equipment such as forklifts, aerial lifts, etc., consider renting extra equipment this holiday season. Equipment rentals offer a flexible way to handle seasonal fluctuations without the commitment of purchasing new equipment. However, keep in mind that maintaining your existing equipment is just as important as adding new equipment to your warehouse operations.
Establish a Returns Process

Returns are an inevitable part of warehouse operations throughout the year, and even more so during the holiday season. Likewise, warehouse managers will need to create a streamlined process for handling returns or exchanges before the holiday season starts, and train employees on the correct protocol. This might include setting up a dedicated workstation to manually process returns or exchanges, or investing in warehouse technology that can automate the processes for you. The faster returns are handled, the better the customer experience. And customers with a positive customer experience are more likely to return to your business in the future.
Prepare Ahead of Time
With preparation and organization, your warehouse will be ready to take on the increased holiday workload without missing a beat. Just remember to give yourself time to implement any new changes or processes well before you need them to be live in production.