5 Warehouse Layout Optimization Tips for Maximum Efficiency
An efficient warehouse layout is crucial for optimizing the storage, movement, and overall operations of a warehouse facility. A well-designed layout can significantly impact a company’s productivity, cost-effectiveness, and customer satisfaction.
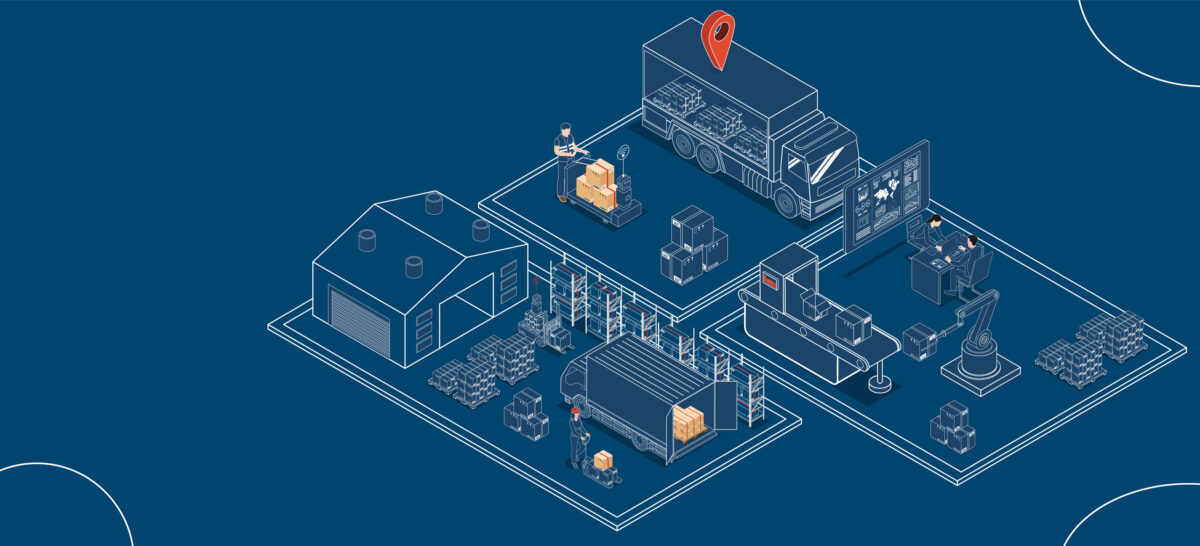
What is Warehouse Layout Optimization?
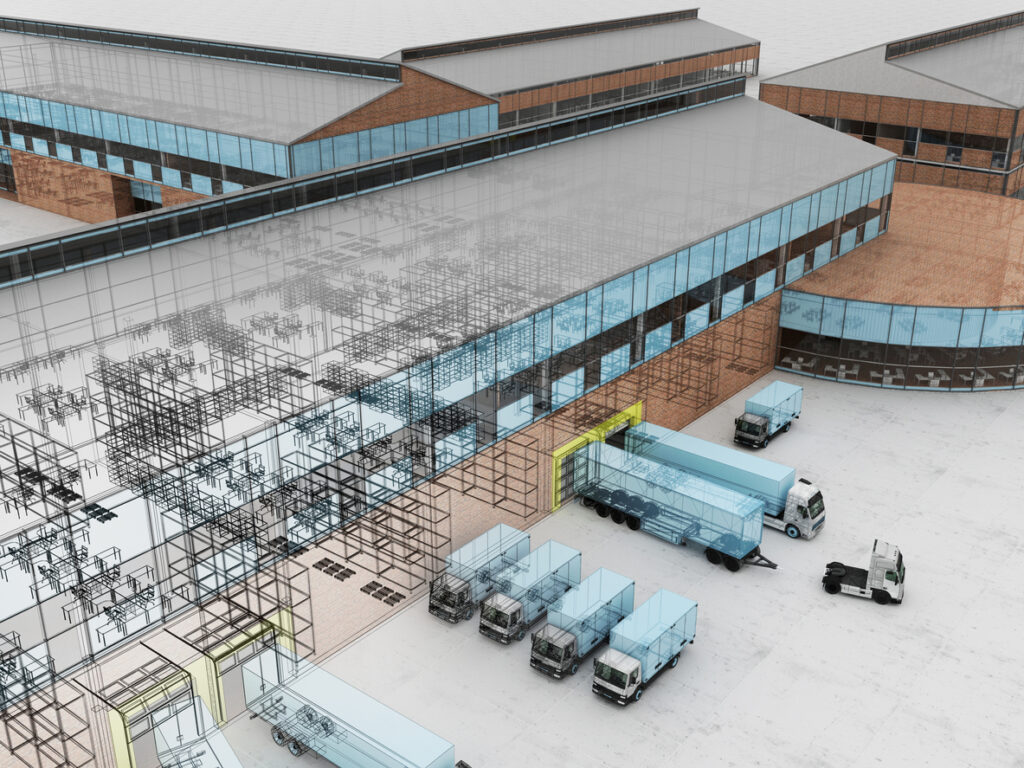
1. Analyzing Current Warehouse Layout
Analyzing your current warehouse layout is a critical step in improving warehouse operations. When you conduct a thorough assessment, you can identify inefficiencies, bottlenecks, and areas for improvement. Some ways in which analyzing your current warehouse layout could be beneficial include improved order picking, minimizing congestion, and increased safety.
When you analyze your current warehouse layout, you can quickly reveal opportunities for optimizing the placement of products. By organizing frequently picked items closer to shipping areas or reducing the number of touches required for each order, you can significantly enhance the order picking process. Additionally, having these products in a smoother transitional environment allows for seamless order picking and shipping, which results in faster and more efficient operations.
As mentioned above, by analyzing your current warehouse layout you will also be able to identify problem areas and improve traffic flow. By recognizing these congested zones, you can help prevent delays and accidents while also creating a much safer and more efficient working environment.
Workplace safety is paramount in most industries, and this holds especially true in the warehousing industry. We touched upon the importance of clearing up congestion for safety’s sake, but further analyzing your warehouse layout will help identify other potential safety hazards. One such example is exposing the need for separating pedestrian and forklift traffic, or zones entirely devoted to foot traffic.
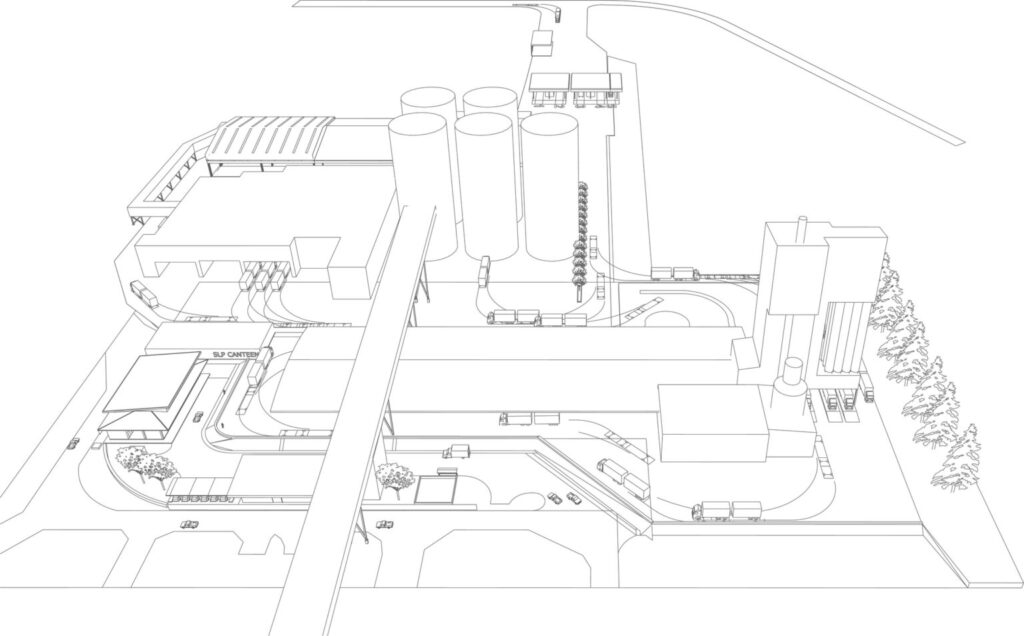
2. Implementing an Effective Warehouse Floor Plan
Implementing an effective warehouse floor plan is crucial for optimizing operations and increasing efficiency. This involves utilizing efficient zoning, product grouping, optimizing the placement of high-demand items, and incorporating clear and logical traffic flow patterns.
By dividing your warehouse into distinct zones based on the types of products you store, and their closely associated products, you can drastically reduce the time it takes to fulfill orders. Some common factors to consider include size, weight, demand, and storage requirements. If you are looking for ways to push this even further, you may also assign specific purposes to each zone, such as storage for bulk items, a staging area for outgoing shipments, or a quality control zone for incoming goods.
Optimizing high-demand item placement may seem like a no-brainer, but it is an important factor to remember as it may often be overlooked. By having these items in easily accessible and highly visible locations you can both minimize the travel time for workers as well as having a clear view of product levels which will reduce the likelihood of stockouts. We recommend utilizing dynamic slotting techniques which adapt the placement of items based on changing demand patterns.
We want to hammer in the importance of traffic flow patterns, as analyzing your warehouse layout will ultimately show you what layout works best for your current system. By designing a clear and logical traffic flow pattern, you ensure smooth movement of both goods and personnel. Always mark which zone is which, even utilizing physical barriers separating the two to enhance safety.
3. Maximizing Space Utilization
By examining your current warehouse layout, you may be shocked to see that there is a surprising amount of “empty” space. Maximizing space utilization in warehouse layouts is essential for efficient operations and cost savings. The three factors mentioned below are some possible options in getting the most out of your space available to you!
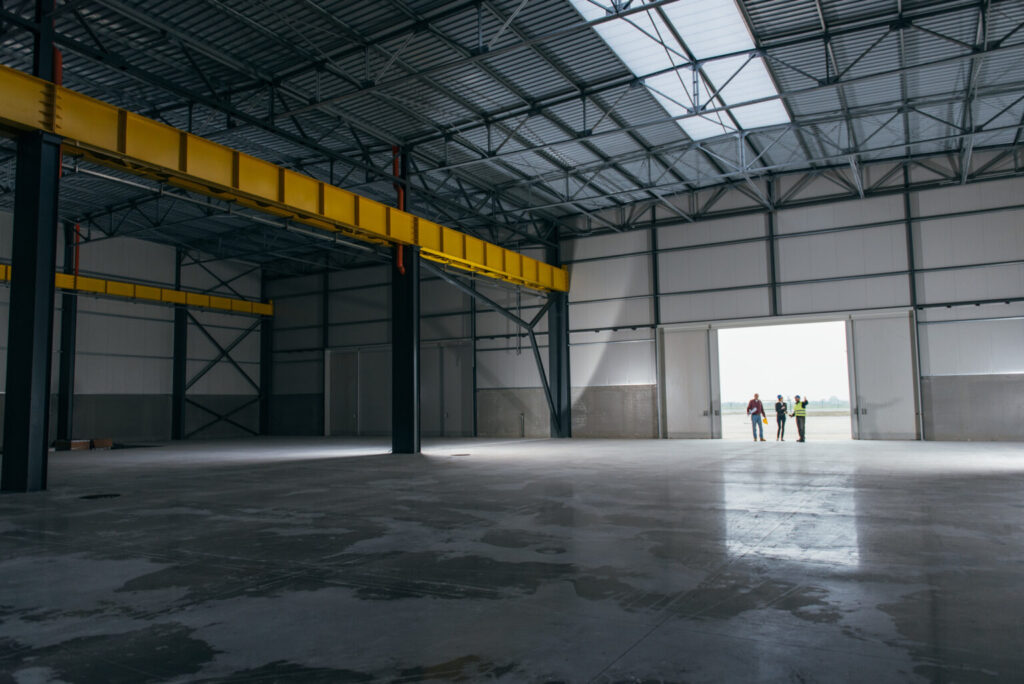
- Vertical Space Utilization
- Install tall and sturdy racking and shelving systems to properly make use of vertical space.
- Utilize adjustable shelving units that can conform to the heigh of the stored items.
- Implement double-deep, selective, driven-in, or push-back pallet racking systems to store palletized goods vertically.
2. Implementing Automated Storage and Retrieval Systems (ASRS)
- High-density ASRS can maximize vertical space. while reducing the need for extensive horizontal storage.
- ASRS systems greatly reduce the need for extensive horizontal storage, allowing more room for other equipment, storage, or pedestrian food traffic.
- Goods-to-person sortation equipment, like AutoStore, makes use of the Pareto Principle to manage popular SKUs to increase the expediency of orders.
3. Utilizing Space-Saving Technologies and Equipment
- Install mezzanine platforms to create additional storage or workspace areas above ground level without expanding the warehouse’s footprint.
- Implement mobile racking or compact shelving systems that enable you to condense storage aisles by moving shelving units closer together.
- Automated storage and retrieval systems are king when it comes to saving floor space, as they consist of vertical shelves that automatically bring the items to the operator.
4. Streamlining Order Picking Processes
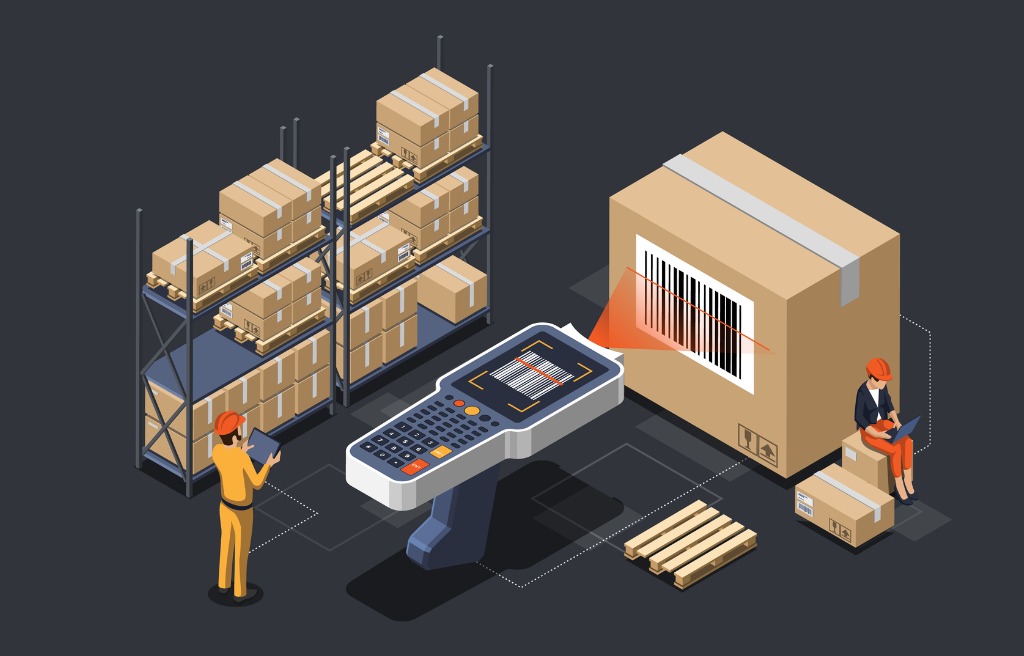
Streamlining order picking processes in warehouse layout optimization is crucial for improving efficiency, reducing errors, and enhancing overall customer satisfaction. You can begin your journey in streamlining order picking processes by implementing a well-organized picking strategy, optimizing order batching and wave picking techniques, and utilizing automation and technology for efficient order fulfillment.
A well-organized picking strategy is not some kind of overarching application, meaning that option A may work for your business, but option B may be best suited for another business. Some potential picking strategies you may want to investigate are zone picking, batch picking, and pick-to-light or voice-guided picking. Incorporating a system that works best for your business can reduce errors and improve order accuracy.
When deciding between batch picking and wave picking there are a few key things to keep in mind. Batch picking involves picking the same items for various orders together, while wave picking involves picking items with matching elements like item size or order time frame. If your business deals with high volumes of orders consisting of small items, then batch picking may be best for you. If your warehouse deals with a high volume of orders consisting of similar orders, then wave picking is the ideal choice for you.
We have discussed the possibilities that become available to you once you incorporate automation within your warehouse operation, almost ad nauseam. We wouldn’t talk about them if they were not a proven method of improving the overall performance of your warehouse! By implementing any of the numerous automation systems available, you stand to significantly enhance the efficiency of your order picking processes which leads to faster order fulfillment, reduced errors, and an improvement in your operations.
5. Enhancing Inventory Management Systems
Enhancing inventory management is a crucial component of warehouse layout optimization, as it helps keep everything in check. This includes ensuring there is efficient space utilization, accurate order fulfillment, and cost savings.
One way of enhancing your inventory management system is integrating a warehouse management system (WMS). By incorporating a WMS in your warehouse operation, you can gain real-time visibility and control over your inventory while managing proper stock levels, tracking item locations, and streamlining inventory-related processes.
Speaking of tracking, it is important to incorporate systems that aid you in the upkeep and management of tracking items (especially high value ones). Utilizing barcoding and Radio Frequency Identification (RFID) helps not only with simplifying order picking, but also with real-time tracking. Many of these technologies do not require a line-of-sight, which can make tracking large quantities of inventory much more efficient.
Lastly, but certainly not least, data analytics. If you are not actively collecting and utilizing data analytics, then you are missing out. We highly recommend collecting data on the various aspects of your warehouse operations, including order history, lead times, demand patterns, and inventory turnover rates. Receiving reports on these matters will give you valuable insights into the market and even help you forecast demand for products.
Conclusion
In conclusion, optimizing your warehouse layout is a multifaceted endeavor that holds the key to improving operational efficiency, reducing costs, and enhancing customer satisfaction. By carefully considering the strategies outlined in this blog, it is possible to transform your warehouse into a well-organized and high-performing hub for your business.
With the right tools and technologies at your disposal, anything is possible! If you are looking to take that first step towards optimizing your warehouse layout for maximum efficiency, touch base with one of the many professionals here at Element Logic!