What is order picking?
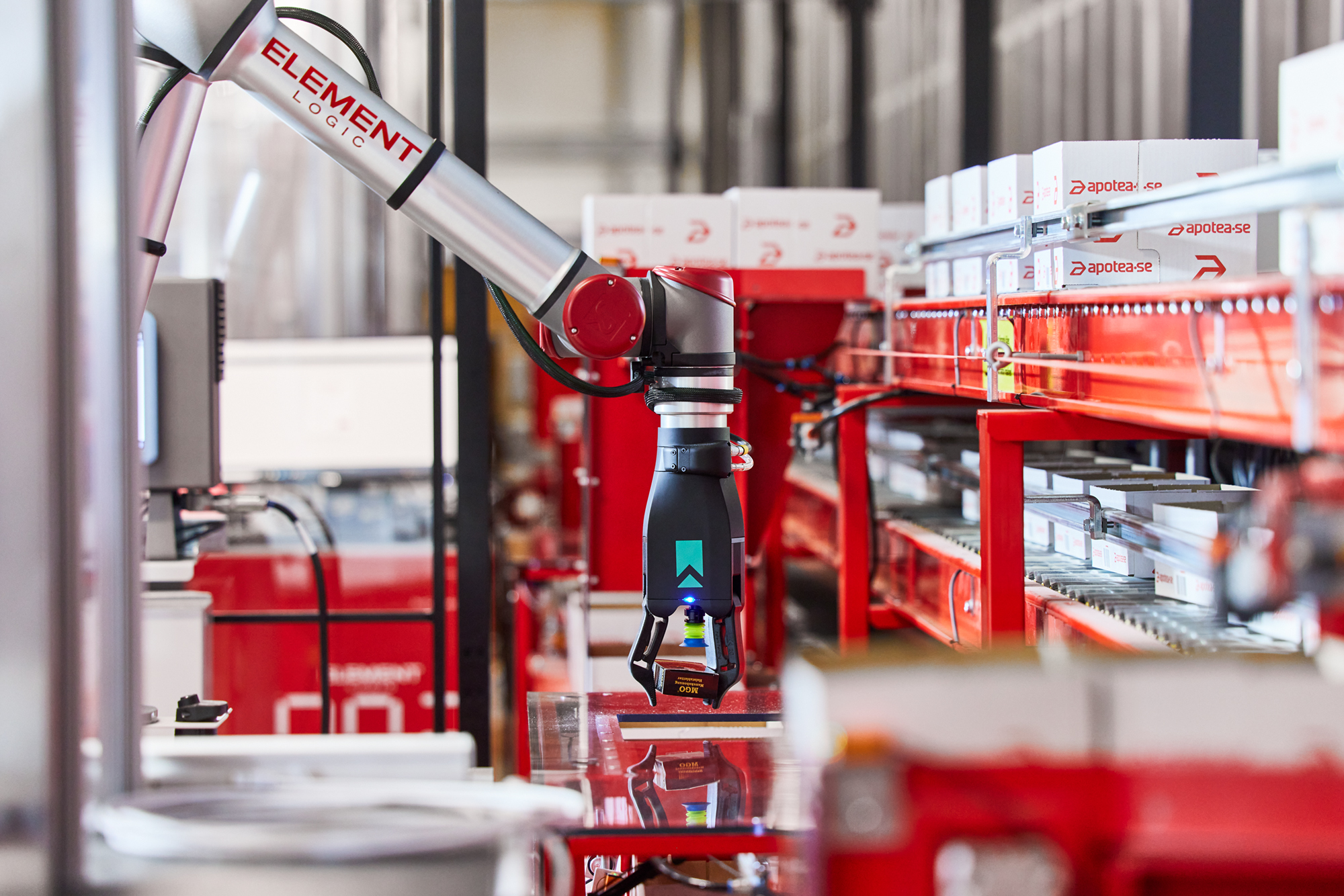
Order picking is the most labour-intensive activity for most warehouses, estimated to comprise up to two-thirds of their total operating expenses. Yet it forms the backbone of successful order fulfilment operations and is crucial in boosting customer satisfaction, making it arguably the most critical activity for e-commerce and retail businesses.
The emergence of e-commerce in recent years has led to a surge in customer demand for more frequent and faster deliveries of smaller orders. Many companies are turning to a range of process improvement solutions to tackle this thorny supply chain issue.
Order picking, the first step in the fulfilment process, involves the collection of items listed in a customer order from a warehouse. Reviewing, optimising, and adapting to operational changes is critical in ensuring that the subsequent stages of order filling, shipping, and post-sales activity proceed seamlessly.
Therefore, you must constantly perfect order picking methods as your business grows and develops. Success in order picking is measurable by high picking accuracy, low cost-per-pick, and timely fulfilment of customer orders.
Get in touch to discuss order picking solutions for your warehouse
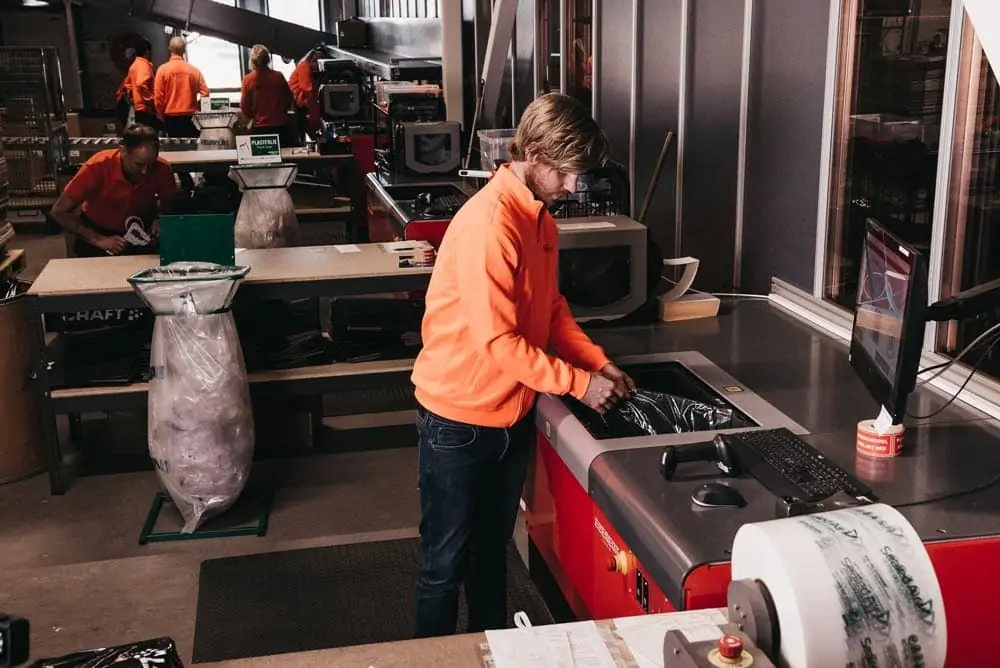
Types of order picking
Given the considerable cost and time investment, improving processes such as picking speed, data accuracy and route optimisation can immediately impact the bottom line.
The following are three fundamental types of order picking:
1. Single order picking
Also referred to as piece picking or discrete picking, this is the most commonly employed technique. In a manual warehouse, pickers move from location to location within the warehouse to retrieve stock-keeping units (SKUs) to fulfil one order at a time. There are more efficient methods than this, but it works well in smaller warehouses that handle simple orders with limited inventory.
2. Batch picking
In batch picking, workers pick multiple orders in one round, resulting in optimised picking activities by reducing travel time and speeding up the fulfilment process. This approach is particularly effective for warehouses that receive multiple orders containing the same SKUs.
3. Multi-batch order picking
Like batch picking, workers reduce picking and travel times by picking multiple orders simultaneously using multi-tiered picking carts. This method is used for orders coming from different areas in the warehouse.
Order picking strategies
Warehouse operators must start with one of the fundamental order picking methods mentioned above. They can then execute more specific order picking strategies, some of the most popular being:
1. Cluster picking
This piece picking process enables the fulfilment of multiple orders simultaneously while also reducing picker travel. It involves workers retrieving SKUs from multiple pick lists and sorting them into various containers, forming a batch. Although this eliminates the need for sorting, it necessitates using advanced warehouse software solutions for accurate scheduling and cluster assignment.
2. Wave picking
Wave picking employs a methodology similar to single order picking, where a picker retrieves one SKU at a time. However, orders are grouped into waves or sets based on customer location and shipping time, and workers send SKUs for sorting and consolidation into individual shipments. This approach is helpful for large warehouses that receive multiple high-volume orders.
3. Zone picking
The zone picking system divides the warehouse into distinct zones, with workers assigned to each zone responsible for fulfilling orders within their designated area. Once all the items in a zone have been picked, the order carton is passed on to the next zone. This system significantly reduces travel time as workers remain within their designated zones while picking items.
What are automated order picking systems?
Automated order picking systems comprise various technologies, systems and devices that streamline and accelerate the order picking process.
These systems typically replace outdated manual processes and materials handling with automated storage and retrieval systems, autonomous mobile robots (AMRs), and order picking robots such as those from AutoStore. They can also include wearables such as mobile barcode scanners and headsets.
Some benefits of automated order picking systems include increased efficiency and productivity, enhanced accuracy, and far fewer, if any, picking errors. They also result in cost savings associated with labour, equipment, and maintenance.
Types of automated order picking solutions
Choosing the most efficient automated order picking system requires identifying your specific requirements since each company’s needs are unique, and a solution that works for one may not work for another.
Here are four types you might consider:
1. Automated storage and retrieval systems (ASRS)
An ASRS is a computer-controlled inventory management system that streamlines the handling, storing, and retrieving of items in a warehouse. The six most prominent types of ASRS are carousel-based, vertical lift module, mini-load, robotic shuttle-based, robotic cube-based, and floor robots.
2. Automated mobile robots (AMRs) and automated guided vehicles (AGVs)
Robots have swiftly risen to warehouse prominence in recent years. Workers no longer must manually push carts along the aisles to retrieve items. Instead, mobile robots do the hard work of moving items throughout the warehouse while either being controlled by human operators or acting autonomously.
3. AutoStore solutions from Element Logic
AutoStore, an innovative robotic cube-based, goods-to-person ASRS, is the market’s fastest order fulfilment system per square metre. It offers the highest storage density of any ASRS and can be customised to meet the evolving needs of businesses.
The robotics technology is eco-friendly, energy efficient, and boasts a dependable average system uptime of 99.7%. Its flexible and modular ability provides an efficient and sustainable picking solution for companies of all sizes.
The synergies between the tailored AutoStore hardware and Element Logic’s specialised software, eManager, offer a unique, complete solution. With this solution, we guarantee fewer picking errors, continuous inventory control, branch-leading availability, and no single point of failure.
For example, one of our customers, European e-grocer Rohlik Group, delivered a threefold increase in picking productivity and created 30% more storage space with our AutoStore solution.
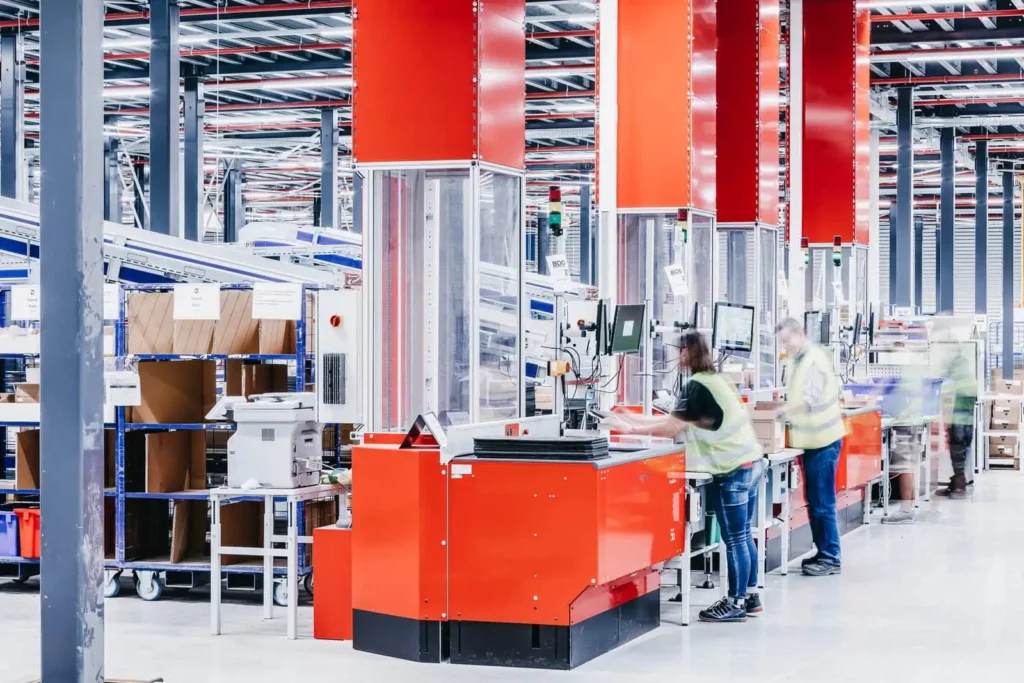
4. Hybrid solutions
These aren’t quite automated order picking solutions, but they can empower workers by easing their workload and improving ergonomics. Two such examples are:
- Pick-to-light: To implement this system, pick-to-light LEDs and barcode scanners are installed on all racks and shelves. When a picker scans a barcode attached to a specific shipping carton being used to fulfil an order, the LEDs for the corresponding SKUs which need to be picked light up. The picker then follows the lit-up LEDs to retrieve the SKUs on their pick list.
- Mobile scanner-based picking: To implement this solution, each SKU must have a unique barcode. Workers carry mobile scanners that display pick lists and the location of each SKU, which they scan as they pick. An error detection feature helps improve accuracy, while warehouse managers can provide optimised picking routes to pickers to increase efficiency.
OneTouch Dispatch
The ideal combination of automation and processes for optimised order picking is Element Logic’s OneTouch Dispatch process, where one operator at an AutoStore port picks, packs, and dispatches all orders they work on. The AutoStore system, empowered by Element Logic’s AutoStore interface software, eManager, presents all items to be shipped to the operator – removing the need for workers to manually pick products.
The same operator handles the packing of the order at the port with the necessary peripheral packaging equipment – there’s no need to pass the picked products over to another team. This process is perfect for single unit orders and bulkier multi-unit orders. The operator saves time when there are multiple units/SKUs in a single order as they only need to perform the packing action once.
Typically, dispatching an order is the responsibility of a completely different team. In OneTouch Dispatch, the same operator who picked and packed the order performs this task. Dispatch labels are printed off at the port and eManager confirms the pick complete to the customer system. The operator then places the packaged orders in a nearby cage or on a conveyor for transportation.
This single-touch process significantly increases efficiency and cost savings, especially in eCommerce order fulfilment and whole store replenishments.
Get in touch to discuss order picking solutions for your warehouse
Thinking rather than spending
Not all warehouse processes are created equal, so it’s important to consider the operational processes of your warehouse before transitioning to automation. Some of these processes, like order picking, are more repetitive, and most likely to benefit from automation.
However, the implementation of automated order picking systems can be complex and disruptive. Element Logic’s warehouse automation and design experts will help you map out your needs and preferences, run simulations, and then design the solution that yields the most value.
A last word on order picking challenges
Large warehouses with a high volume of different SKUs face significant challenges in their picking processes. The key to mastering the art of picking and packing is overcoming the dual threat of inaccurate inventory records and missing product information.
Failure to do so can prove disastrous for any warehouse operation, making the use of reliable processes imperative. One of the primary challenges is coordinating various order management and logistics solutions to ensure effective control of the entire operation.
Lastly, in the e-commerce industry, modern fulfilment centres are crucial and highly complex operations. However, no matter how well-funded they are, they are destined to fail if their order picking systems are not equally sophisticated.
Investing in advanced and appropriate order picking systems is essential to ensure long-term success. It’s the most effective and only way to both optimise warehouse operations and future-proof them.
Posted by Gavin Harrison, UK Sales Director, Element Logic.
Want to know more about automated order picking systems? Contact us today to discover how you can optimise your warehouse efficiency.
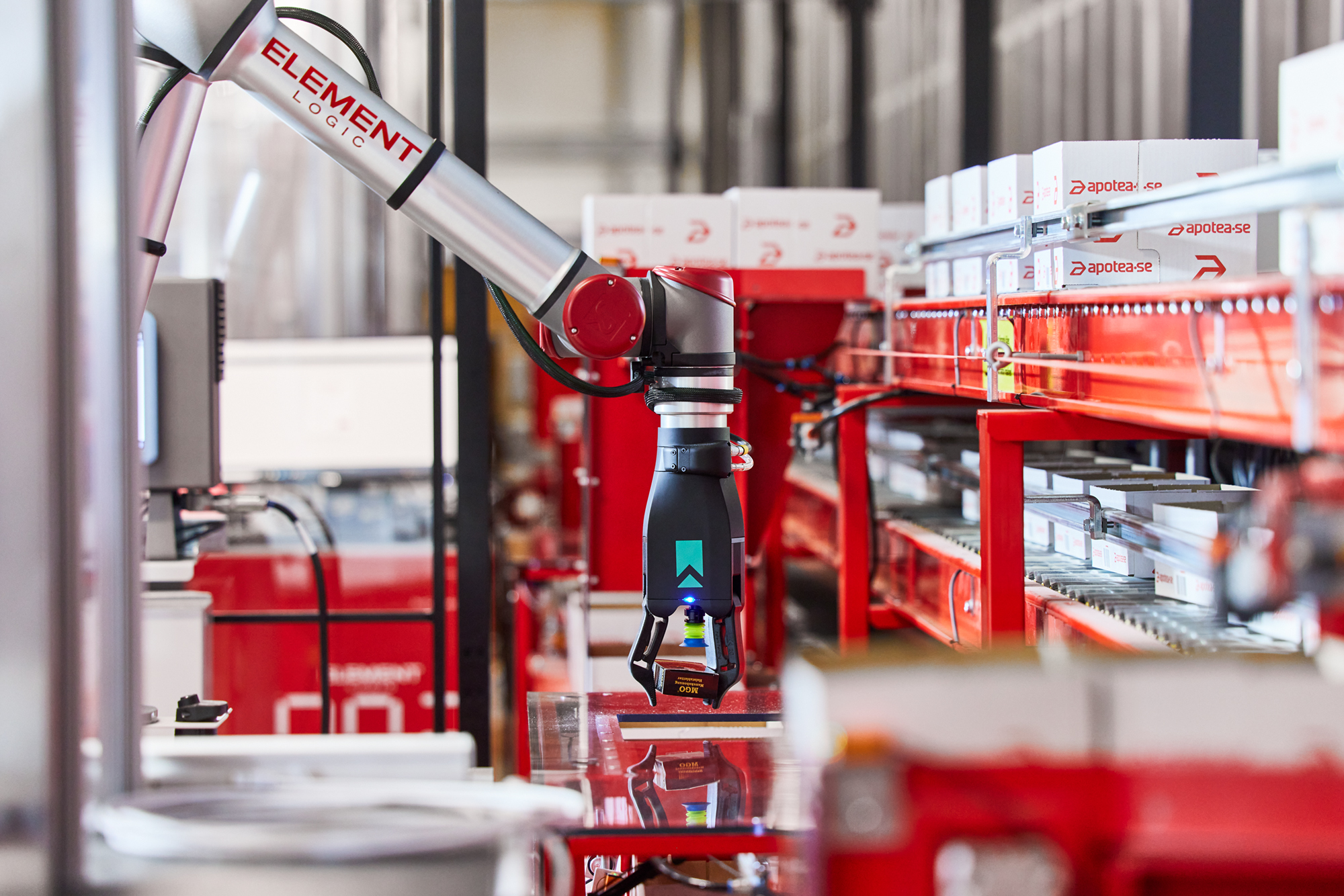