How to create an automated warehouse slotting strategy
Warehouse slotting, also called bin digging, is crucial for optimising the AutoStore workflow and achieving maximum throughput in the hundreds of AutoStore systems worldwide that are powered by Element Logic.
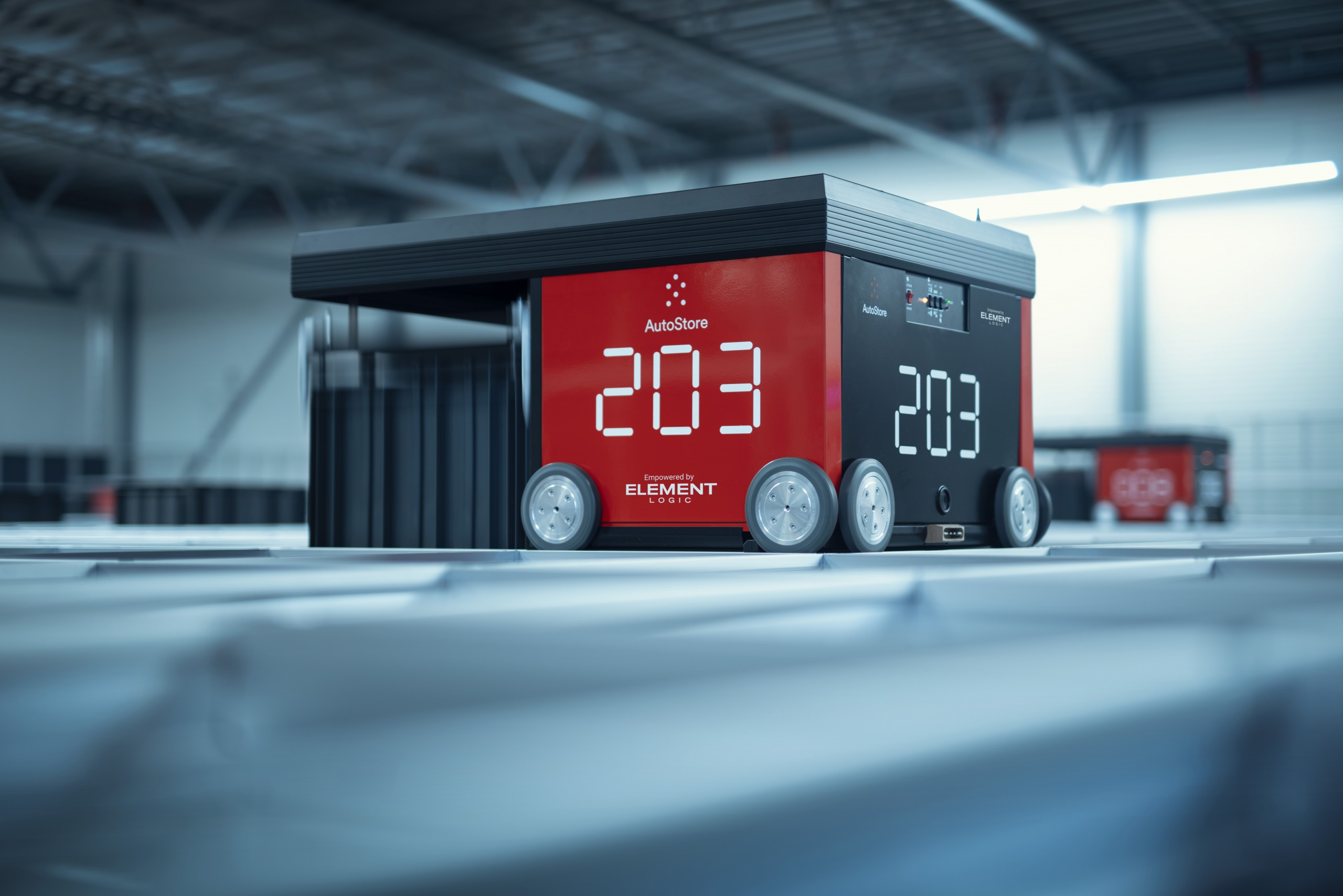
What does “warehouse slotting” mean?
One of the costliest jobs in a warehouse is rearranging inventory, otherwise known as slotting. The goal of warehouse slotting strategies is to ensure that frequently picked items are easily accessible and stored in the most convenient location, reducing the time and effort required to fulfill orders.
It is costly to use human labor for warehouse slotting and, in modern fulfillment centers, there are often too many products to rearrange inventory with just manual labor.
Automated warehouse slotting: The smart way to rearrange inventory
All storage systems have a slotting function – whether traditional or automated storage and retrieval systems (ASRS). The general idea is that popular items that sell frequently are stored in front or outside of double or triple deep locations. However, the demand for each item is rarely predictable, never stable and highly seasonal, making static warehouse slotting fail.
Slotting optimisation is essential but traditionally too costly for companies. With eCommerce projected to reach $7 trillion annually by 2025, warehouses must consider solutions beyond the capabilities of human labor to rearrange inventory.
How slotting optimisation works with an AutoStore system
An AutoStore system eliminates manual warehouse slotting by embracing three key assumptions:
- Inventory is not static. It is highly dynamic – constantly growing and changing.
- The most reliable predictor of which bin is required is the order demand.
- New inventory is always more popular than older inventory and can be placed on top of older inventory.
The performance of the AutoStore system is unaffected by the product volume stored inside the grid or how the individual Stock Keeping Units (SKUs) are arranged.
By using something called “natural slotting”, the system ensures high performance – warehouse slotting optimisation.
In short, “natural slotting” is when popular bins are returned and stored at the top layer of the grid. Over time, slower moving bins descend to the bottom of the stack, ensuring that robots rarely have to dig down that far.
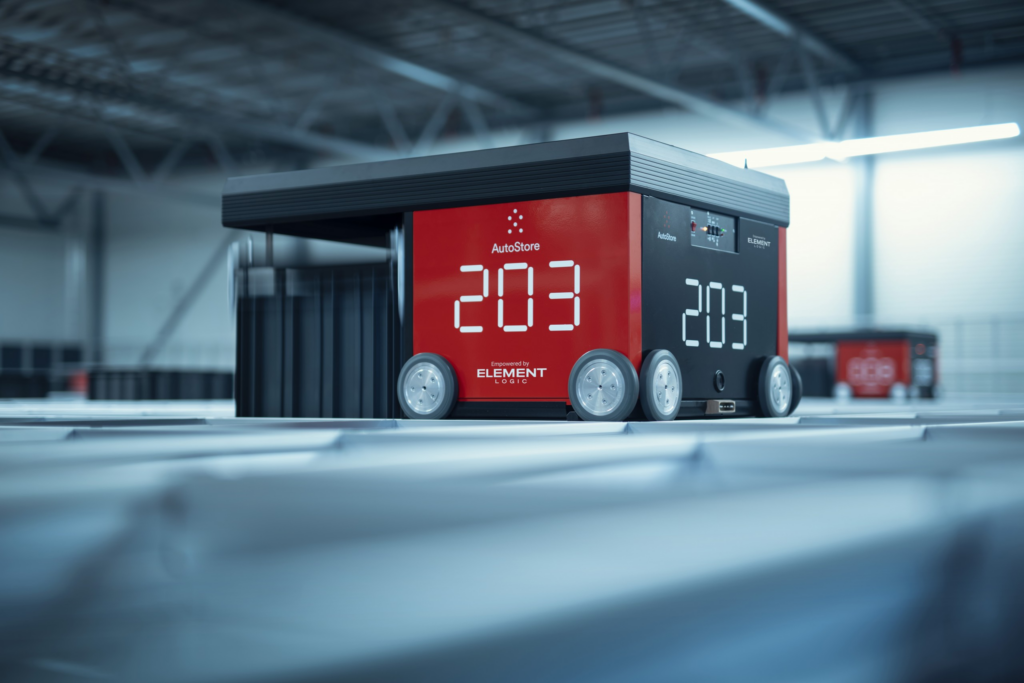
How much time is spent slotting in AutoStore?
The average AutoStore robot fleet spends roughly 80% of its time serving bins and only 20% digging. Digging is mostly done during breaks or overnight when other systems sit idle.
To eliminate the need for operators to wait for orders, bins are proactively positioned through a process called bin preparation that uses the warehouse management system (WMS). By completing this step prior to order fulfillment, operators can work continuously without delays or interruptions.
In the worst-case scenario, when a bottom bin is needed for an order, the robot spends three minutes and 36 seconds to pick the item on average.
If the bottom bins are needed more frequently, you can always add more robots.
20% of inventory equals 80% of orders
On average, an AutoStore system comprises 16 bins stacked in a grid and around 80% of the products ordered from this warehouse constitutes just 20% of the entire inventory.
Based on this 80/20 example:
- Thirty-nine percent of bins are accessible with zero digging.
- The average bin is located just 2.5 cells deep in the stack and takes about 27 seconds to retrieve.
- The bottom half, or eight levels, represent less than 5% of bins needed.
If you look at other ASRS systems that move bins vertically by climbing or using lifts, AutoStore warehouse slotting is often faster and more efficient at fulfilling orders.
Three distinctive AutoStore features help save time by offsetting digging efforts:
- Density makes travel distances 25% to 40% shorter.
- When a grid is exposed on top, it provides a high-capacity environment for robots to move efficiently.
- No queuing when bins are delivered to ports.
Warehouse slotting with unrivaled performance
Given the short distances AutoStore robots need to travel, you avoid wasting time. If you add in the structure, aisle navigation and the long waiting time in queues at ports, AutoStore product slotting in warehouse outperforms its competitors – with the average robot achieving 30+ bin deliveries an hour.
The average digging depth of 350 AutoStore systems measures just 2.6 bins deep, which is a perfect 80/20 distribution on a 16-bin tall grid.
No system on the market can achieve the same level of performance.