Transforming logistics with AutoStore™ : Linney’s journey to operational excellence
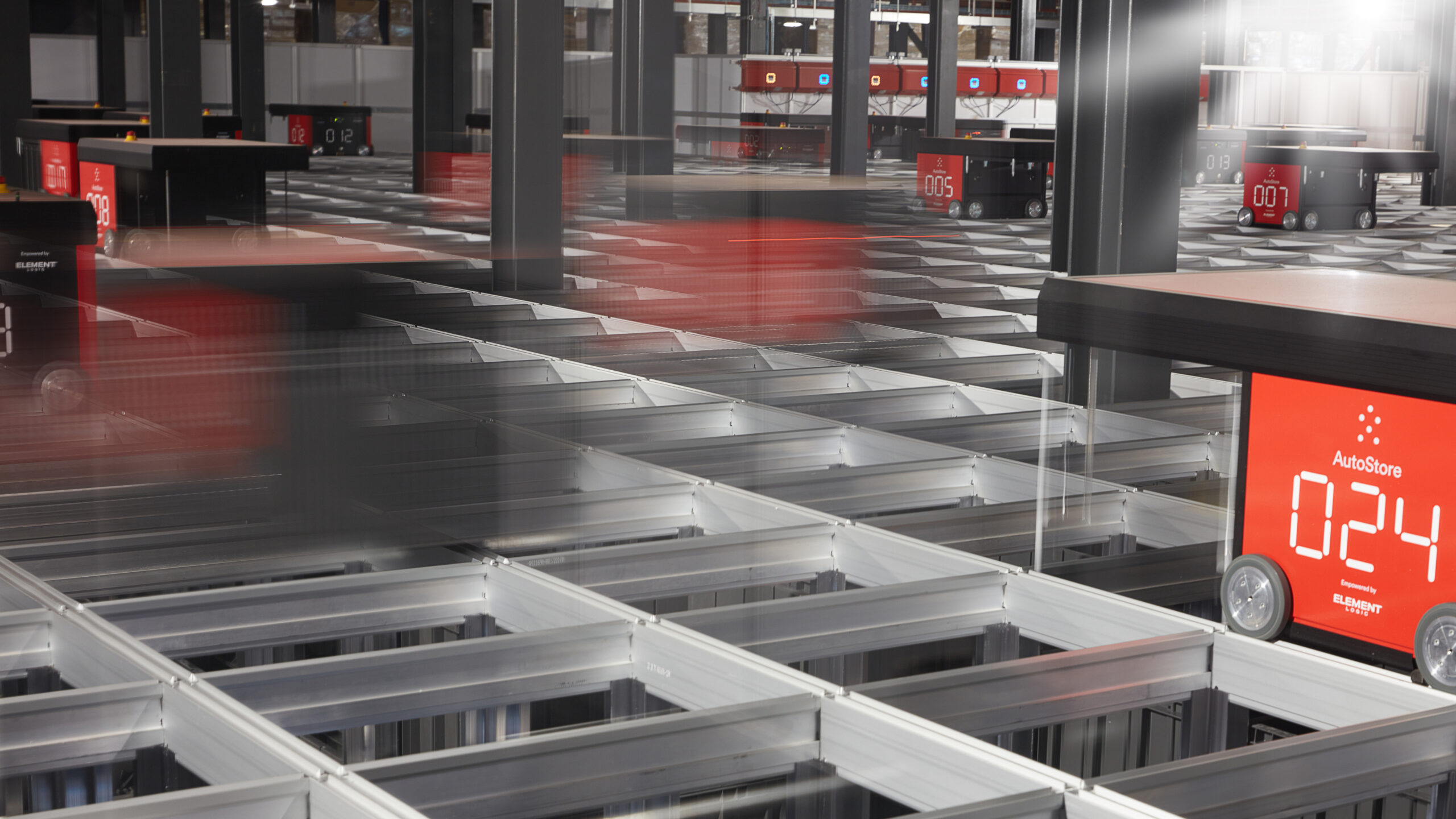
Linney, a leading connected marketing group that offers world-class third-party logistics services (3PL), has significantly optimised its operations with an AutoStore™ solution from Element Logic. Achieving a throughput of 1,870 bins per hour, the company’s investment in automation technology is driving even greater efficiency in its fulfilment and warehousing operations.
As a full-service marketing group with a specialism in ecommerce fulfilment, Linney has many years of experience assisting retailers with warehousing and logistics, covering the full ecommerce spectrum from pick-and-pack fulfilment to distribution and returns management.
Linney strives to be world-class in all its activities and ecommerce is no exception. With clients of varying sizes and differing needs, AutoStore™ enables the company to scale up storage to match its clients’ growth needs, giving them the flexibility to find the fulfilment solution that suits them.
To meet its complex needs, Linney engaged Element Logic to design and build an AutoStore™ system for its fulfilment centre. A key advantage of AutoStore™ was its modular implementation, allowing it to be introduced in three phases. This approach enabled Linney to test the system as a proof of concept after each stage, ensuring optimal scalability and effectiveness.
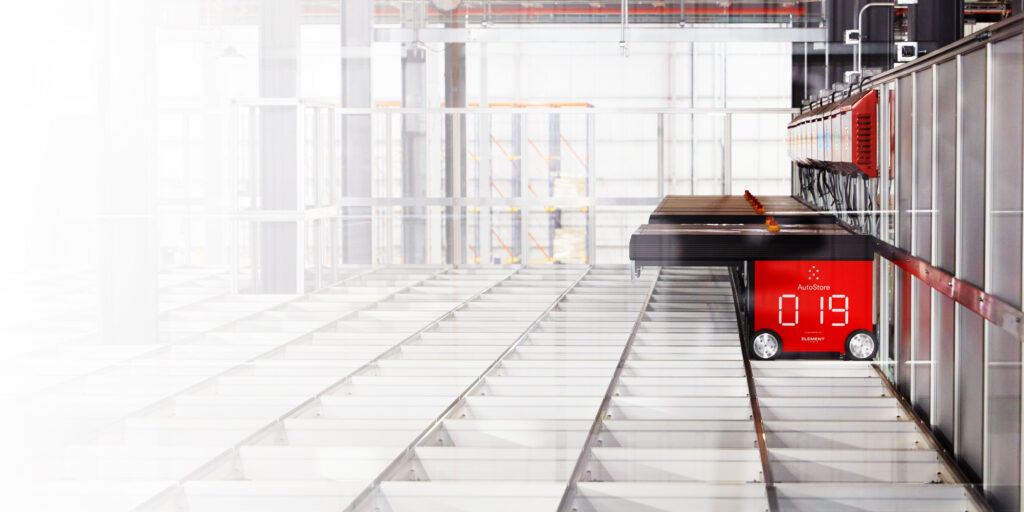
A success from the start
In the first phase, Element Logic installed a 16,000-bin system with 25 robots and seven pick ports in Linney’s warehouse. This installation took place between March and September 2022, with the system going live in mid-October, just in time for the golden quarter and Black Friday peaks for Linney’s key ecommerce clients.
Following this successful initial phase, Linney invested in an additional 15,000 bins, 10 more robots, and extra pick ports for the second phase of the implementation.
This expansion brought the total to 31,000 bins and increased the grid size to about 1,000 square metres, covering only around 10% of the total warehouse space. The benefits to Linney’s operations were substantial. The company was able to double throughput and focus even more effort on maintaining high pick-accuracy levels. This enhanced precision, coupled with AutoStore’s™ efficiency, enables Linney to easily manage peak periods.
Benefits for workers – and the company as a whole
The new system also had a positive impact on Linney’s warehouse teams. Consolidating the pick area into one location and replacing repetitive manual tasks by employing robots for the movement of goods has enabled Linney to upskill its people. For example, staff no longer spend time walking through the warehouse, allowing for more focused and productive work. Linney used this opportunity to roll out low-level engineering training as standard for employees working in the fulfilment area. This provided them with higher-level skills and created more engaging job roles.
From a business perspective, the investment in automation gave Linney a competitive edge over other third-party logistics providers. With many competitors lacking the means to invest in such advanced systems, Linney positioned itself at the forefront of the industry, offering a faster, more accurate and more efficient way of working.
In essence, the AutoStore™ system delivered on multiple fronts, strengthening Linney’s market position and establishing a robust foundation for further growth.
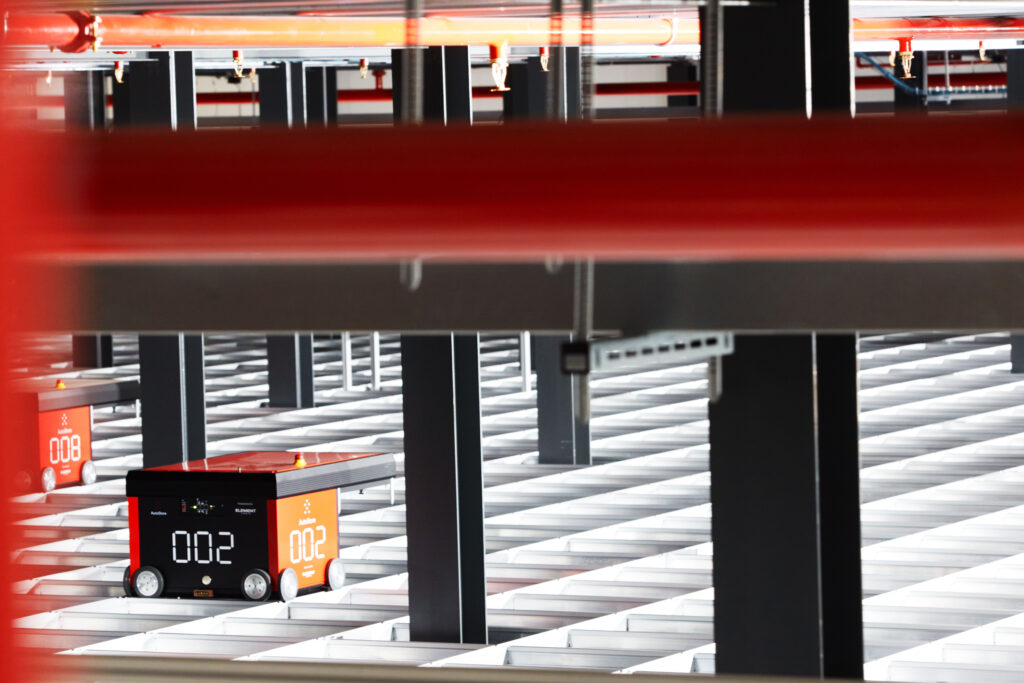
Making the most of customised processes
One of AutoStore’s™ key strengths for Linney has been its flexibility. As a third-party logistics provider serving multiple clients with varying requirements, Linney needed a highly configurable solution. AutoStore™ delivered on this front, allowing for a non-standard operation with a high degree of customisation. At Element Logic, we worked closely with Linney to design pick categories tailored to the company’s specific needs, enabling the efficient handling of a diverse range of products onsite.
The success of the first two phases led Linney to introduce the GMC Genesys automated packaging system in a third phase. By configuring AutoStore™ to pick and place items directly into the Genesys automated packaging machine, Element Logic streamlined Linney’s fulfilment process even further. This seamless connection between storage, picking and packaging showcases the system’s ability to integrate with other automated solutions for maximum efficiency.
Another crucial aspect of the implementation was the bespoke integration between AutoStore™ and Linney’s carrier management system. This allowed Linney to achieve a smooth flow of information from order picking to shipping, reducing errors and improving overall logistics management.
All of which highlight AutoStore’s™ flexibility. By adapting the system to work seamlessly with existing processes and additional automation, Element Logic created a truly optimised fulfilment operation for Linney, capable of meeting the diverse demands of the company’s clients.
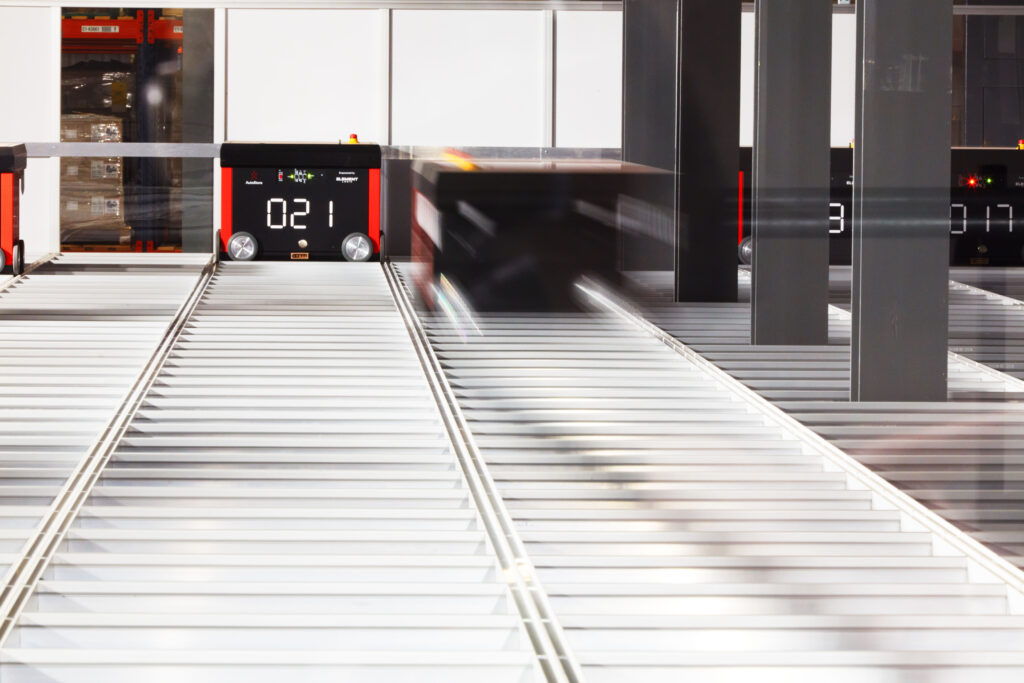
Ongoing support and service
After fully integrating the AutoStore™ system, Element Logic continues to provide Linney with comprehensive ongoing support and service.
A cornerstone of this support comes in the form of monthly performance review meetings. These regular check-ins allow both parties to assess the system’s efficiency, address any concerns, and discuss potential improvements. This proactive approach, coupled with around-the-clock support, helps maintain peak performance and allows for timely adjustments as needed.
At Element Logic, we also conduct regular data reviews, analysing the system’s performance metrics to identify trends, bottlenecks and areas for improvement. These insights are invaluable in ensuring that AutoStore™ always operates at its most efficient and effective.
Planning for the future
While AutoStore™ has already been a tremendous success for Linney, Element Logic continues to engage with the company on future changes and improvements. These collaborative meetings focus on planning for growth, ensuring that the AutoStore™ system can scale alongside Linney’s expanding business needs.
For instance, to prepare Linney for various scenarios, we’ve been working closely together using our simulation services. These simulations model different operational conditions, allowing the company to test and prepare for peak periods or other challenging situations before they occur.
Through these ongoing discussions and plans for potential expansion, we’re able to analyse what’s possible. And we’re pleased to support Linney as they continue to grow.
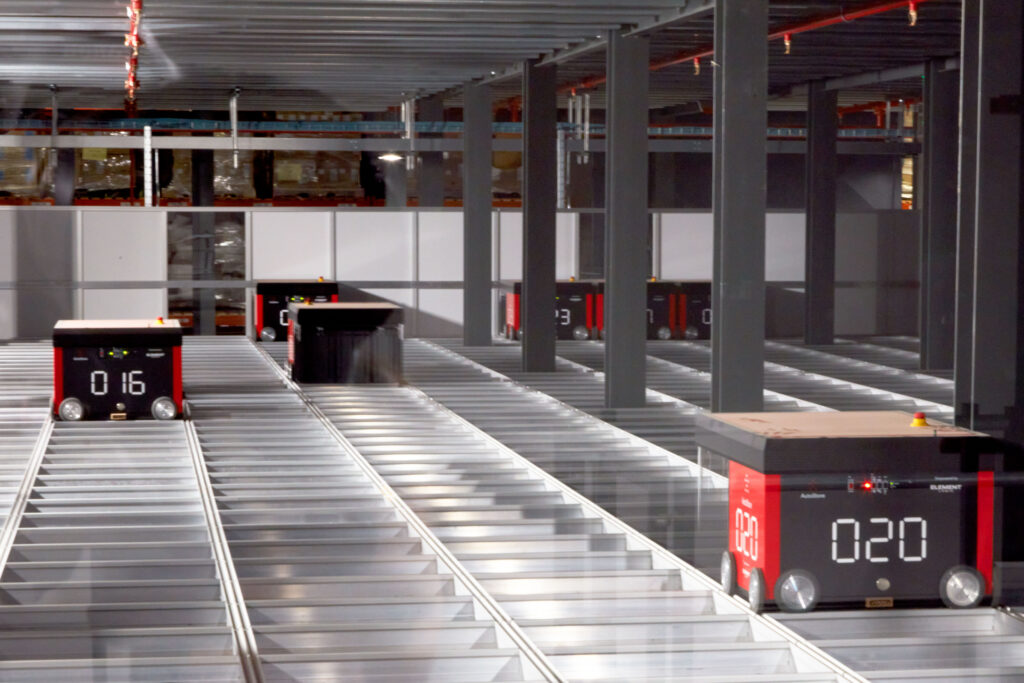
AutoStore™ @ Linney stats:
- Installed in September 2022
- 31,000 bins and 35 robots
- Packing 800 boxes per hour through the Genesys
- Picking 1,870 bins per hour via AutoStore
- Peak day is 485 orders per day per robot
- AutoStore™ phase 1 : 21m x 28.2m = 592sqm (6.7% of our warehouse)
- AutoStore™ phase 2: 33.8m x 16.8m = 567sqm (6.42% of our warehouse)
- AutoStore™ total size: 45.8m x 45m = 1,159 sqm (13.1% of our warehouse)