Want the perfect AS/RS design for your warehouse? Here are 10 factors to consider
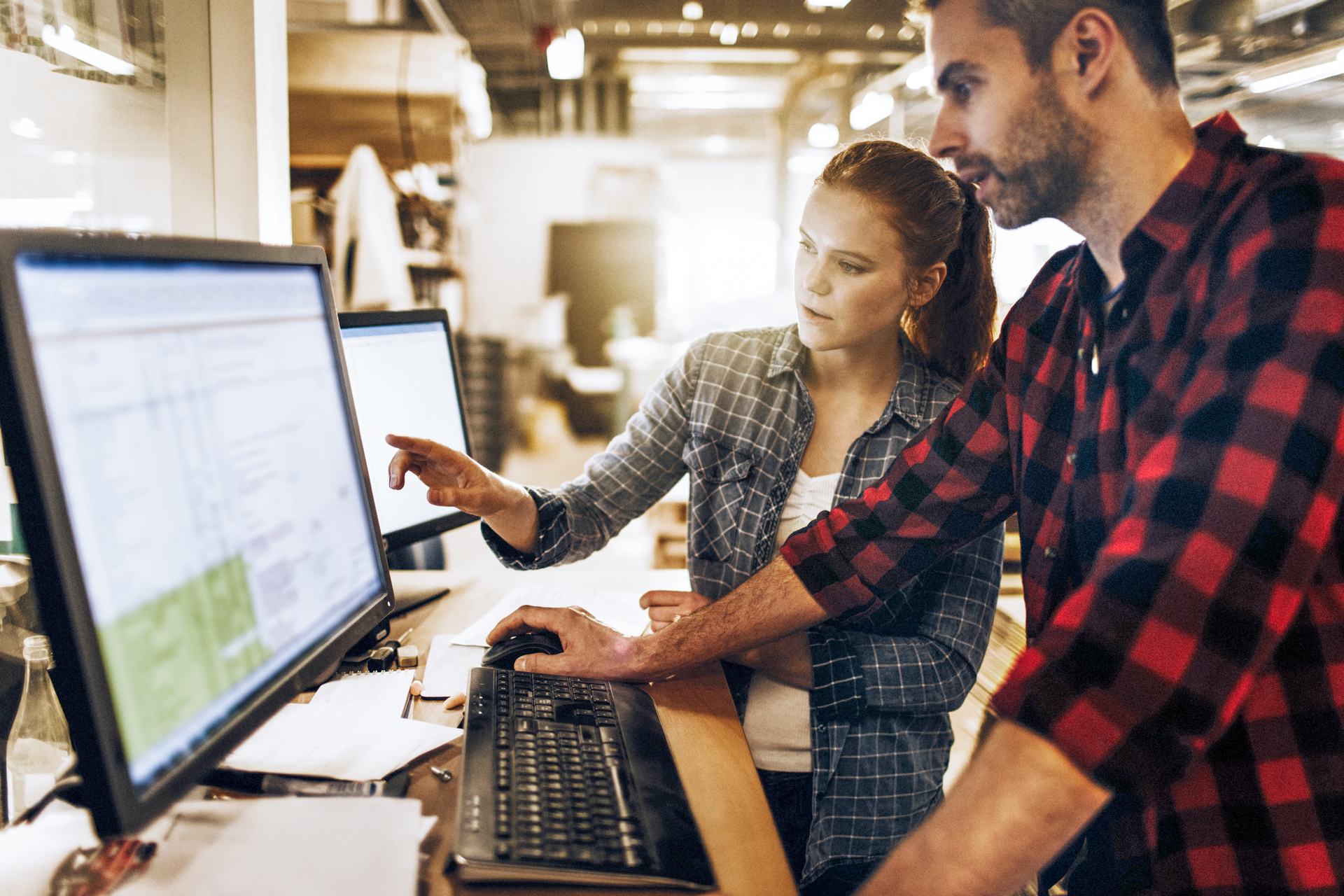
Automated Storage and Retrieval Systems (AS/RS) have completely transformed the logistics and warehousing industries. These computer-controlled systems automate the storage and retrieval of goods, allowing businesses to optimise storage density, streamline inventory management, and improve overall operational efficiency.
Whether it’s a robotic cube-based AS/RS like AutoStore, vertical lift modules (VLMs), or carousel systems, selecting and designing the right solution can significantly influence your warehouse’s success.
However, an AS/RS is not a one-size-fits-all solution. Each warehouse is unique, so your design must reflect your facility’s specific constraints, operational requirements, and long-term goals.
In this blog, we’ll discuss the 10 most important factors to consider when developing an AS/RS system design. Carefully weighing these considerations will help ensure your system achieves optimal performance and adapts to your future business needs.
1. Facility and space requirements
The physical constraints of your facility lay the foundation of your AS/RS design. It’s essential to understand your space, as every warehouse offers different challenges. From ceiling height to floor strength, these factors influence which system will be most suitable.
For example, AS/RS solutions like AutoStore are designed to maximise vertical storage, making them ideal for facilities with high ceilings and limited floor space. However, if your floor’s load-bearing capacity is low, a structural assessment will be needed to ensure it can support the dense, concentrated weight these systems deliver.
Furthermore, effective planning should take into account obstructions within your warehouse, such as columns, sprinklers, or HVAC systems, which could impact installation. It’s equally important to consider how the AS/RS will integrate within the existing workflow to avoid disruption to critical processes like staging, picking, and packing. By addressing your facility’s specific requirements, you can achieve an AS/RS design that aligns perfectly with the overall layout and operational flow.
2. Inventory characteristics
The nature of the goods you handle is just as important as the physical space when designing your AS/RS. Different types of inventory demand different storage solutions. For example, the size, weight, and shape of your stock-keeping units (SKUs) will determine the bin or tote sizes used in the system. Warehouses handling standardised product dimensions will find it easier to optimise their AS/RS design, while operations with irregular or oversized goods may need customised configurations.
In facilities relying on high turnover rates, frequently retrieved items should be placed where they can be accessed quickly, with slower-moving SKUs stored deeper within the system. For businesses handling temperature-sensitive items, such as frozen foods, the design must incorporate proper environmental controls. Factoring in your inventory’s specific characteristics ensures the AS/RS effectively supports daily operations while improving its reliability in the long term.
3. System throughput and workflow integration
System throughput, or the rate at which goods are retrieved and processed, is a critical design consideration. The demands of your operation — such as order volume, average pick sizes, and peak fulfilment periods — dictate the system’s design. A high-throughput warehouse requires an AS/RS capable of handling numerous transactions within tight timeframes. For example, systems like AutoStore excel at supporting fast-moving e-commerce environments due to their ability to quickly retrieve bins, even at peak demand.
Moreover, the AS/RS must integrate seamlessly with workflows across your warehouse. Order picking, staging, and shipping areas should be positioned efficiently to minimise unnecessary travel or delays. The placement of portals (workstations where operators interact with the system) plays an important role, as they should reduce transportation bottlenecks and maximise productivity. By understanding your operational processes in detail, you can ensure the AS/RS doesn’t just support throughput but enhances the entire workflow.
4. Scalability and adaptability
Warehouses are rarely static environments. A flexible AS/RS design needs to accommodate your business’s growth and evolving needs. Modular systems, like robotic cube-based AS/RS solutions, are particularly effective because they allow for incremental expansion. As demand increases or inventory profiles change, you can simply add robots, expand grids, or increase storage capacity without overhauling the entire system.
Scalability also ensures your system can adapt to peak workloads or seasonal surges without compromising efficiency. For instance, businesses experiencing high fluctuations in order volume — such as retailers during the peak holiday season — can design their AS/RS to maintain throughput and minimise operational disruption. Planning for the future at the design stage ensures your investment delivers long-term value.
5. Automation level
Determining the right level of automation for your AS/RS system involves balancing performance, complexity, and cost. Fully automated systems can deliver exceptional accuracy and efficiency with minimal human intervention, resulting in fewer errors and lower long-term labour costs. However, they also require more significant upfront investment compared to semi-automated systems.
Beyond choosing between full and partial automation, consider how your AS/RS integrates with smart robotics, such as automated guided vehicles (AGVs) or picking arms, to enhance workflows further. The most effective systems not only optimise processes but are also intuitive for operators to manage and maintain — a key factor for long-term success.
6. Cost considerations
The cost of designing and implementing an AS/RS can vary significantly depending on its complexity and scale. Both the initial capital expenditure and the operational costs need to be factored into the decision-making process. For instance, some systems may cost more initially but deliver higher returns over time due to lower maintenance and energy needs. AutoStore designs, for example, offer excellent cost-efficiency by reducing warehouse footprint while improving throughput.
Additionally, businesses should conduct a clear ROI analysis before investing. This should take into account labour savings, productivity improvements, and reduced space requirements. While cost is an important factor, the ultimate priority is ensuring your warehouse reaps measurable benefits in both the short and long term.
7. Safety and compliance
Safety and compliance requirements should never be overlooked when designing your AS/RS. Fire safety measures, especially in high-density storage systems, must meet regulatory standards. Systems like AutoStore can integrate with fire prevention and suppression systems to create compliance-ready designs.
Protecting your operators is also essential. Anti-collision technologies ensure moving robotics operate without risking worker safety, while ergonomic workstations minimise the physical strain on employees. Ensuring compliance with industry regulations and creating a workplace that prioritises safety will help avoid disruptions and maintain efficiency.
8. Environmental and energy considerations
Incorporating sustainability into your AS/RS design is increasingly important, especially for businesses aiming to reduce their carbon footprint. Modern AS/RS systems, like AutoStore, are built to be energy-efficient, requiring only the equivalent of a few light bulbs to power their operations. Using compact designs also reduces lighting, heating, and cooling needs in large warehouses, driving down energy costs.
By planning for sustainable operations, businesses can contribute to environmental goals while improving long-term cost-efficiency.
9. Maintenance and downtime
Minimising downtime is critical for maintaining peak performance. Your AS/RS design should incorporate features such as predictive maintenance using IoT sensors, which alert you to potential issues before they become a problem. Systems with built-in redundancy, like AutoStore’s independent robotic units, help ensure no single equipment failure disrupts the entire operation.
Easy access for repairs and strong vendor support are also crucial to reducing downtime and maximising your system’s uptime.
10. Software integration
Finally, the software powering your AS/RS system plays an equally vital role. Seamless integration with your existing Warehouse Management System (WMS) is essential for real-time tracking of inventory, order fulfilment, and predictive analytics. User-friendly software allows operators to manage the system efficiently, minimising training requirements and maximising productivity.
Building the best AutoStore design
If you’re considering an AutoStore system — one of the most advanced AS/RS solutions available — there are a few critical design factors to keep in mind. Start by evaluating your operational needs, such as storage density and throughput goals. AutoStore excels in high-density environments, where space is limited but SKU variety is high.
The grid layout is central to its efficiency, so understanding your facility’s dimensions and ceiling height will help maximise both vertical and horizontal capacity. Additionally, the number of robots and ports should align with your current workflow and allow room for scalability. A well-designed AutoStore solution integrates seamlessly with your processes, delivering unmatched flexibility and efficiency.
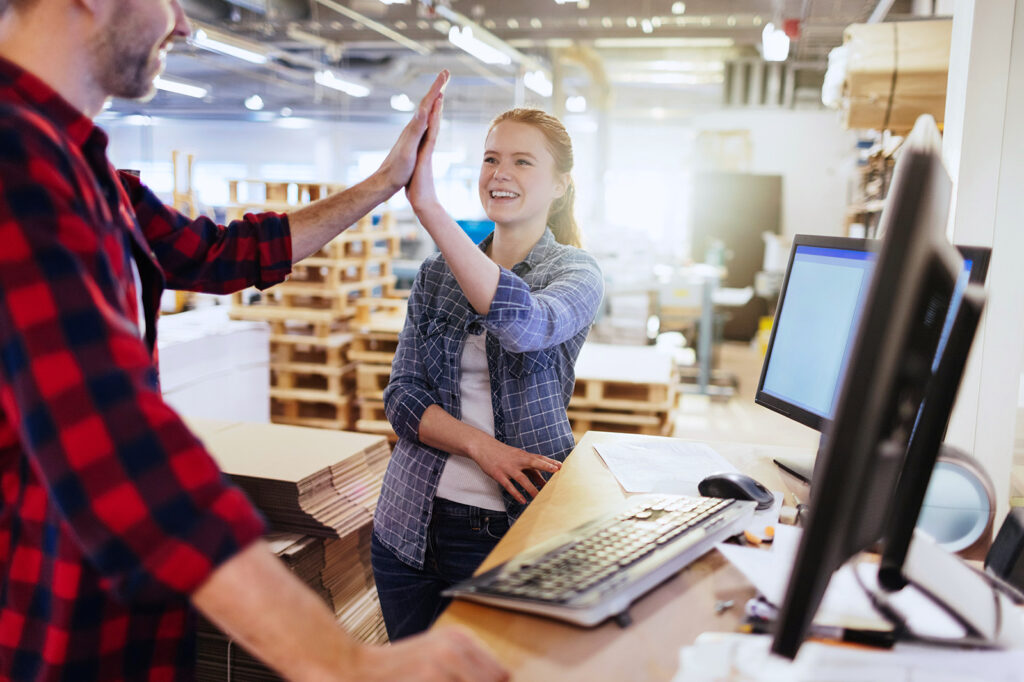
Conclusion: future-proof your warehouse with AS/RS design
Designing the perfect AS/RS or AutoStore system requires careful planning and consideration of your specific requirements. From evaluating your facility’s physical constraints to optimising throughput and ensuring safety compliance, every decision impacts the system’s performance and long-term value.
At Element Logic, we specialise in designing and implementing tailored AS/RS solutions that evolve with your business. If you’re ready to optimise your warehouse efficiency, contact us today — our experts are here to help.