Understanding the costs of an automated storage and retrieval system (AS/RS)
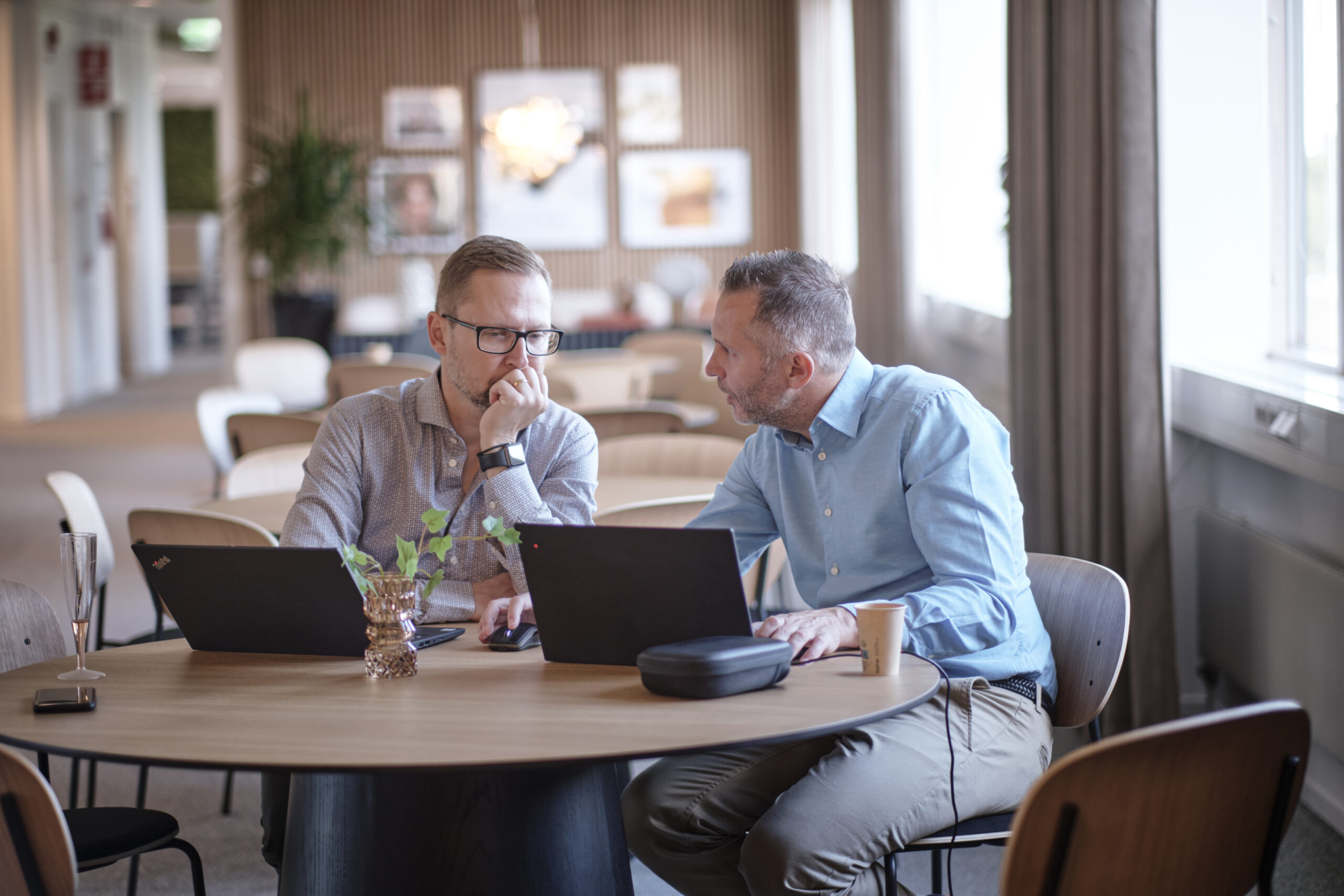
In the ever-evolving world of warehouse automation, Automated Storage and Retrieval Systems (AS/RS) play a pivotal role in streamlining operations. These advanced systems are designed to manage inventory with precision by automating the storing and retrieving process. By optimising supply chain efficiency and inventory management, AS/RS can transform the way warehouses operate — reducing manual workloads and enhancing throughput.
However, as enticing as automation may sound, the financial aspects require careful consideration. Understanding the cost of automated storage and retrieval systems is crucial for businesses evaluating this investment. Without proper insight into the various expenses involved, there’s a risk of encountering unexpected costs or misaligned expectations after implementation.
This blog will guide you through the key factors that influence AS/RS costs, breaking down both the direct and indirect costs. By the end, you’ll be well-equipped to make an informed decision about whether AS/RS is the right fit for your operation.
What drives AS/RS costs? Key factors to consider
Investing in an AS/RS involves weighing numerous variables. Delve into the key aspects that shape the cost and uncover how they might impact your budget.
- The type of AS/RS: There isn’t a one-size-fits-all AS/RS solution. From robotic cube-based systems like AutoStore to vertical lift modules (VLMs) or carousel-based setups, the technology you choose will define both capability and cost. Advanced systems, such as robotic cube-based solutions, often come with a higher price tag but offer unparalleled storage density and scalability. Simpler systems, like vertical or horizontal carousels, may be more affordable but are limited in terms of speed and throughput.
- Size matters: The size of your AS/RS — both in terms of storage density and the weight it must handle — has a direct impact on the total cost. Whether you’re storing lightweight electronics or heavy industrial components, scalability plays a critical role in determining expenses.
- Complex equipment = precision, but at a price: High-performance AS/RS systems come with advanced robotics, intricate structures, and cutting-edge input/output technology. While these features elevate operational efficiency, they also increase the price tag.
- Brains behind the system: Specialised software drives your AS/RS. Its level of sophistication can escalate costs, but it ensures smooth inventory tracking, automation, and overall efficiency.
- Customisation and integration: Adapting an AS/RS to your specific operational needs —whether integrating with existing workflows or optimising for unusual layouts — can demand a higher initial investment. However, this upfront tailoring prevents headaches down the road.
- Hidden costs: Expenses such as shipping, installation, and relocating inventory into the system often surprise buyers. Be sure to factor these into your budgeting process.
- Scaling for peak times: If your operation requires rapid picking and fulfilment —especially during seasonal peaks — the system’s configuration may lean toward higher speed and capacity, which will cost more.
- Ongoing maintenance: From routine servicing to replacement parts, ongoing upkeep should be baked into your AS/RS costs. Don’t forget to account for potential downtime impacts, as well.
- Support tools that keep it running: Accessories like totes, bins, and dividers are small but essential contributors to the overall functionality—and thus the bottom line.
The cost of an AS/RS isn’t just about the upfront price. Each decision plays a role in the long-term return on your investment, making careful consideration vital.
Direct and indirect AS/RS costs: planning for the full picture
When calculating the cost of automated storage and retrieval systems, it’s important to look beyond the numbers on the invoice. AS/RS expenses typically fall into two categories — direct costs, which are upfront and tangible, and indirect costs, which surface over time. Properly framing these expenses helps you plan for both immediate needs and long-term success.
Direct costs: what you pay upfront
- Equipment: The physical machinery, such as storage racks, retrieval units, and robotic components, is a key investment.
- Software: Integration with inventory management and existing ERP (Enterprise Resource Planning) systems is essential. Software licensing contributes here.
- Installation: Costs for delivery, system setup, and initial calibration are straightforward expenses.
- Training: Ensuring your workforce is equipped to operate and maintain the system is an important cost upfront.
Indirect costs: keeping things running smoothly
- Operational expenses: Energy consumption, maintenance, and repairs are unavoidable, ongoing expenditure.
- Downtime: Be aware of potential productivity losses during maintenance or unexpected malfunctions.
- Software renewals: Licence renewal fees for key management systems can crop up regularly.
- Facility upgrades: Adjustments like raising ceilings or strengthening floors may be necessary to accommodate your AS/RS.
- Insurance: An advanced AS/RS might increase premiums, depending on its complexity.
- Learning curve losses: Initial reductions in productivity during system adoption should also be accounted for.
Factoring in these direct and indirect AS/RS costs ensures that you walk into the process fully prepared. Long-term financial planning is essential to get the most from your system.
Ensuring long-term ROI from your AS/RS investment
An AS/RS is a significant financial commitment, but the return on investment (ROI) can be game-changing if approached with a comprehensive strategy. Follow these key steps to secure long-term value:
- Strategic investment: Ensure adequate resources — including time, capital, and skilled labour — are allocated to your AS/RS project. Ongoing maintenance and system updates aren’t optional but essential for sustained success.
- Plan for a holistic ROI: Don’t just consider labour savings or storage density when calculating ROI. Other key benefits include improved workplace safety, higher order accuracy, reduced downtime, enhanced inventory visibility, and lower energy costs.
- Design for efficiency: Work with your supplier to match the AS/RS design to your specific needs. Factors like warehouse height, environmental concerns, and seasonal demand shifts are vital when optimising costs and throughput.
- Think long-term: Budget for at least 20 years, incorporating inflation and other cost variables. Tools such as discounted cash flow analysis and net present value (NPV) calculations will help you assess projected ROI.
- Stay adaptable: Success demands ongoing performance evaluation. Be prepared to evolve with shifting market dynamics and allocate resources to initiatives with the highest value potential.
- Future-proof your system: Anticipate operational needs by planning for scalability and modularity. Trends like demographic shifts and technological advancements should also guide your implementation strategy.
By taking a forward-thinking, detailed approach, you ensure that your AS/RS not only boosts current operations but also continues to deliver value well into the future.
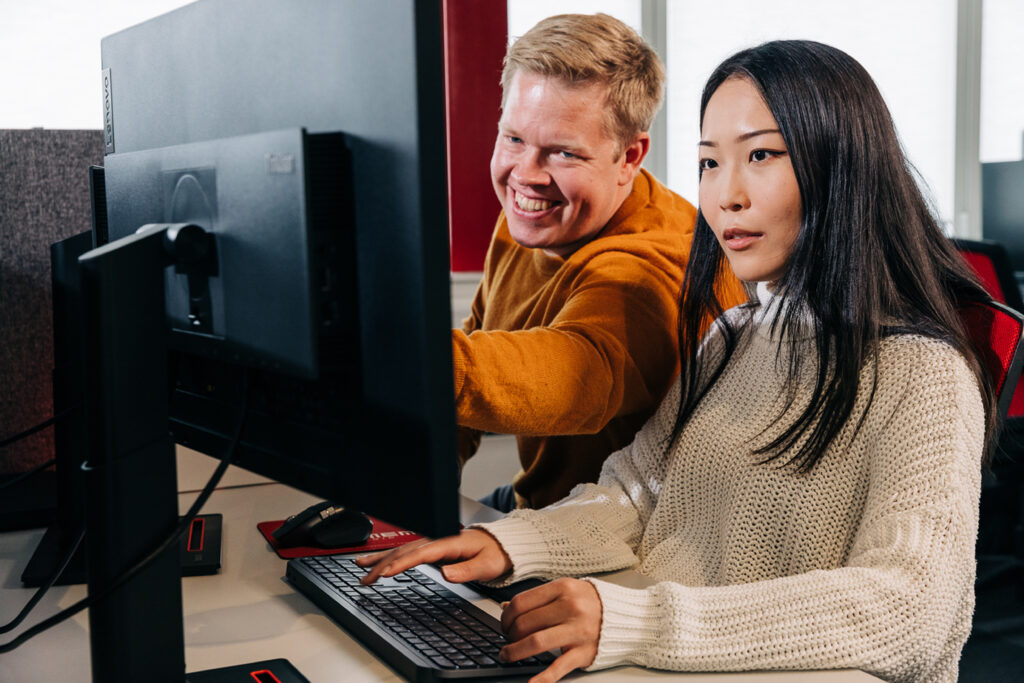
Partner with Element Logic to choose the right AS/RS
At Element Logic, we specialise in helping businesses identify and implement the right warehouse automation solutions for their operations. With decades of experience and solutions like AutoStore, we focus on delivering efficient, scalable results tailored to your needs.
Whether you’re looking for a small-scale optimisation or a complete overhaul, our team is here to guide you every step of the way. Reach out to one of our experts today and discover how our innovative solutions can transform your warehouse and maximise your ROI.