Mastering the art of bin picking: revolutionising warehouse automation with AutoStore
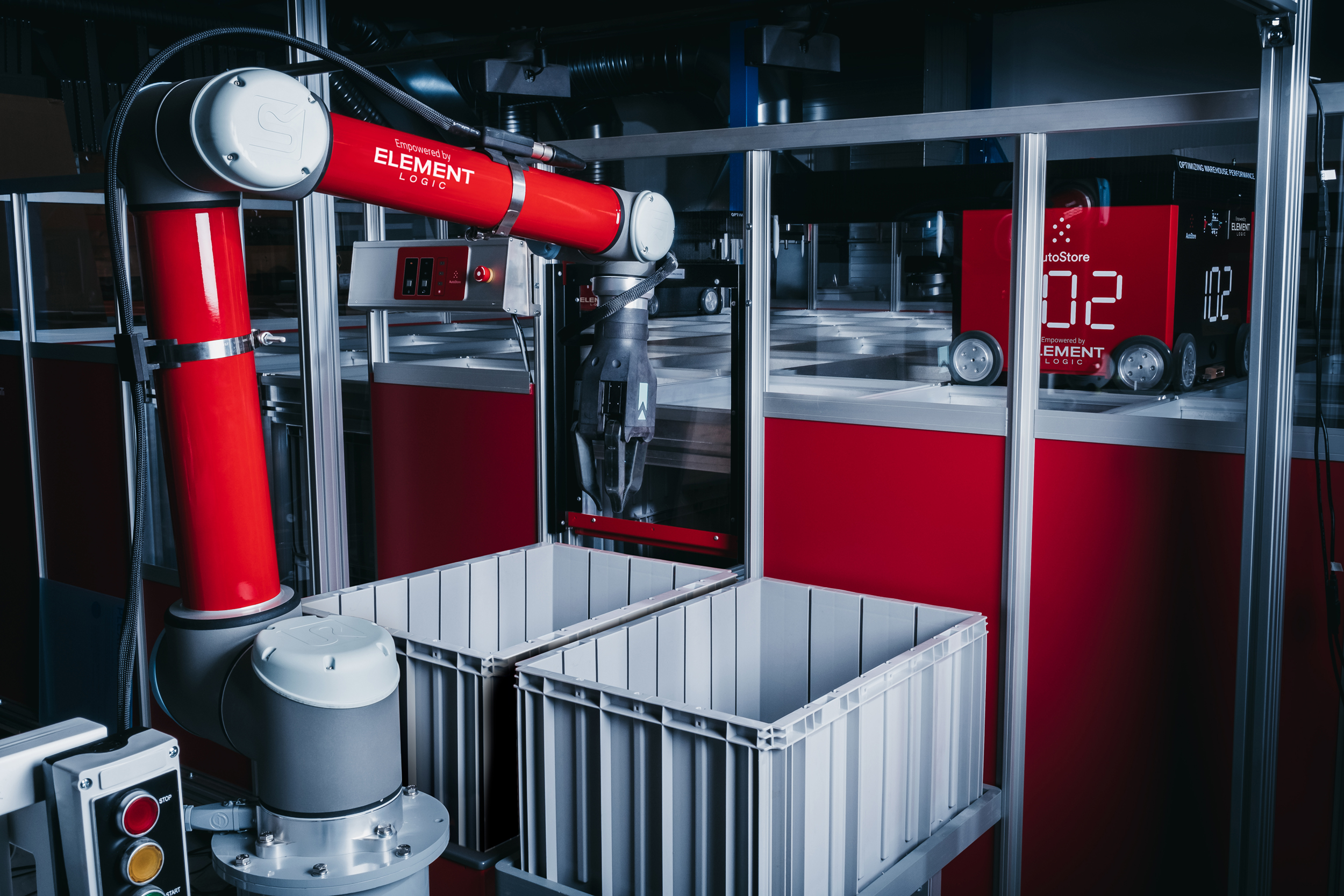
At Element Logic, we’re passionate about transforming warehouse operations through cutting-edge automation solutions, with AutoStore at the heart of our offerings. One of the most crucial aspects of modern warehousing is bin picking — a process that’s evolving rapidly with technological advancements.
In this blog, we’ll explore how to successfully integrate bin picking systems into your AutoStore-powered warehouse environment, unlocking new levels of efficiency and productivity. From understanding the basics to implementing state-of-the-art robotic bin picking solutions, we’ll guide you through the journey of warehouse automation.
Unlocking efficiency: the essentials of warehouse bin picking
Bin picking in a warehouse is a fundamental process that’s undergoing a revolutionary transformation. At its core, bin picking involves retrieving specific items from storage containers or bins to fulfil orders or move products through the supply chain. It’s a crucial component of warehouse operations and order fulfilment processes, directly impacting your bottom line.
In traditional warehouses, bin picking was a manual task, relying on human workers to locate and retrieve items. However, with the advent of automation and robotics, we’re seeing a shift towards more efficient and accurate bin picking solutions.
At Element Logic, we specialise in integrating advanced bin picking systems with AutoStore, a cutting-edge automated storage and retrieval system (AS/RS). This combination allows for unprecedented levels of efficiency and accuracy in warehouse operations.
Modern bin picking solutions often use sophisticated technologies like:
- Vision systems: 3D cameras and artificial intelligence identify and locate items within bins.
- Robotics: Robotic piece-picking arms equipped with specialised grippers or suction cups retrieve items from bins.
- Software: Advanced algorithms plan optimal picking paths and avoid collisions.
By implementing these technologies, warehouses can overcome common challenges such as dealing with diverse product ranges, improving efficiency and accuracy, and seamlessly integrating with existing warehouse management systems (WMS).
As we continue to innovate in the field of robotic bin picking, we’re excited about the possibilities for further optimising warehouse operations and enhancing overall supply chain efficiency.
The power and pitfalls of bin picking: a balanced perspective
At Element Logic, we’ve seen firsthand how bin picking can transform warehouse operations. However, like any technology, it comes with its own set of advantages and challenges.
Let’s explore these to help you make an informed decision about implementing bin picking solutions in your warehouse.
The benefits of bin picking include:
- Supercharged productivity: Bin picking robots, such as those from AutoStore, can operate round the clock, significantly boosting your warehouse’s output. They’re tireless workers, consistently picking items at high speeds without the need for breaks.
- Cost-effective labour management: By automating repetitive picking tasks, you can reassign your workforce to more value-added roles. This not only reduces labour costs but also enhances job satisfaction among your team.
- Pinpoint accuracy: Automated bin picking systems dramatically reduce human errors in product positioning and picking. This leads to fewer order mistakes and improved customer satisfaction.
- Space optimisation: The AutoStore system, combined with efficient bin picking, allows you to maximise storage density and make the most of your warehouse space.
- Adaptability and flexibility: Modern bin picking systems can adapt to various environments and be reprogrammed for different tasks. They’re designed to handle a wide range of product shapes, sizes, and orientations, making them versatile assets in your warehouse.
- Enhanced safety: By reducing the need for repetitive manual tasks, automated bin picking systems help minimise the risk of repetitive strain injuries among your workforce.
The challenges of bin picking include:
- Complexity: Bin picking, especially random bin picking, is a complex task for robots. It requires advanced vision systems and sophisticated algorithms to recognise and locate parts accurately.
- Initial investment: Implementing a robotic bin picking system involves a significant upfront cost. However, at Element Logic, we work with you to ensure a strong return on investment over time.
- Product variability: Handling a diverse range of products can be challenging, requiring sophisticated gripping mechanisms and vision systems. Our solutions, including the eOperator robotic arm, are designed to tackle this challenge head-on.
- System integration: Bin picking systems need to be seamlessly integrated with existing WMS. Our team of experts ensures a smooth integration process, minimising disruption to your operations.
- Maintenance and upkeep: Regular maintenance of robotic systems and vision components is necessary. We provide comprehensive support and maintenance services to keep your system running smoothly.
- Training requirements: Your staff may need training to operate, maintain, and troubleshoot the automated bin picking systems. Offer thorough training programmes to ensure your team is fully equipped to manage the new technology.
While these challenges exist, the benefits of bin picking often far outweigh the difficulties for many warehouse operations. As technology continues to advance, we’re constantly improving our solutions to address these challenges and maximise the benefits for our clients.
Seamless integration: Bin picking and AutoStore in perfect harmony
AutoStore is a unique cube storage automation system where goods are stored in bins stacked directly on top of each other in a grid structure. Robotic units glide along the top of this grid, retrieving and storing bins as needed. This innovative design forms the foundation of the bin picking solution.
The bin picking process in AutoStore includes:
- Robotic retrieval: Intelligent robots navigate the top of the AutoStore grid with precision. They can access any bin in the system, even digging through stacks to reach the required products. This flexibility ensures that no item is ever out of reach.
- Workstation delivery: Once retrieved, bins are brought to workstations, which we call ports. These ports serve as the interface where either human operators or our advanced piece picking robots interact with the AutoStore system.
- Natural slotting for optimal efficiency: A clever “natural slotting” method can optimise bin placement. Popular bins are returned to the top layer of the grid for quick access, while slower-moving items naturally descend to the bottom over time.
This intelligent organisation means AutoStore robots rarely need to dig to the bottom of the stack, significantly speeding up the picking process.
The AutoStore system’s efficiency speaks for itself:
- On average, 80% of orders come from just 20% of the inventory.
- An impressive 39% of bins are accessible with zero digging.
- The average bin is located just 2.5 cells deep and takes only about 27 seconds to retrieve.
These metrics translate to lightning-fast order fulfilment and improved warehouse productivity.
Taking it further: integration with piece picking robots
To push the boundaries of automation even further, we’ve integrated piece picking robots at the workstations:
- Order preparation: Robots can pick products from AutoStore bins and place them in empty bins or totes for future fulfilment.
- Pick and pack: In combination with automated packing systems, robots can pick items directly from AutoStore bins and place them into shipping cartons.
- Batch picking: Robots can pick items from AutoStore bins and distribute them to multiple destinations, such as totes or put wall compartments.
By combining efficient storage, intelligent slotting, and robotic retrieval, an AutoStore bin picking system offers a highly optimised solution for warehouse operations. It’s particularly suited for environments with high SKU counts and varying demand patterns.
With this system, we’re not just improving bin picking — we’re revolutionising the entire warehouse workflow, helping you stay ahead in today’s fast-paced logistics landscape.
Elevating your warehouse with Element Logic
At Element Logic, we’re proud to offer cutting-edge bin picking solutions that seamlessly integrate with the AutoStore system. eOperator, our robotic piece picking solution, is at the forefront of this technology.
The eOperator uses advanced vision systems and AI to identify and pick individual items from AutoStore bins. It can handle a wide variety of product shapes, sizes, and materials, achieving high pick rates of up to 600 picks per hour. This system can operate 24/7, dramatically improving warehouse productivity.
Our eOperator also features flexible gripper technology, machine learning capabilities for continuous improvement, and easy integration with existing warehouse management systems.
Embracing the future of warehouse automation
As we look to the future, we see even greater potential for AI and robotics in warehouse automation. We’re continually innovating to stay ahead of the curve, ensuring our clients have access to the most advanced and efficient bin picking solutions available.
Ready to take your warehouse operations to the next level? Get in touch with us today.