Automating DIY retail: How Element Logic streamlines port operations during peak seasons
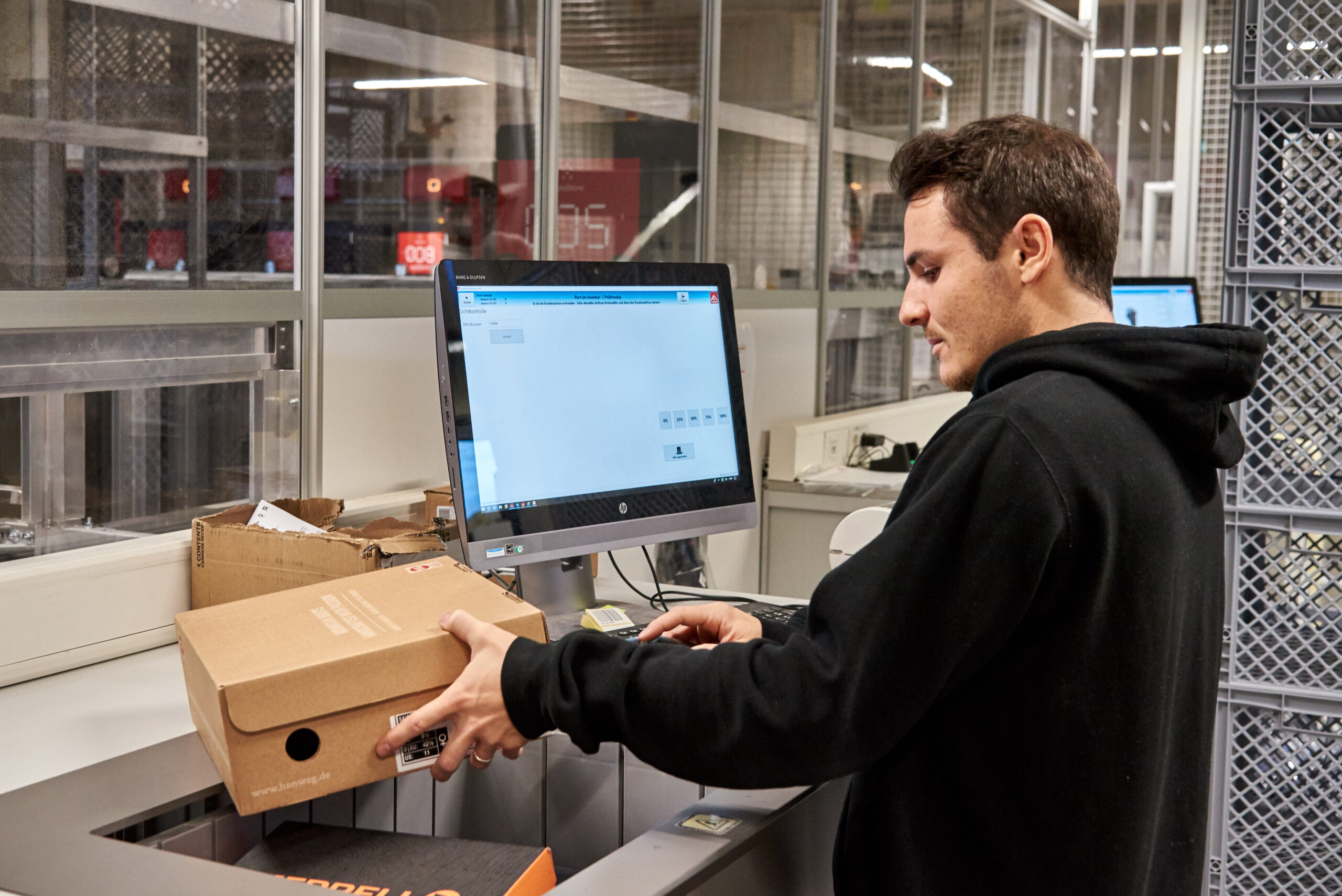
DIY retail is booming, but with success comes challenges — especially during peak seasons. For DIY stores, these peak periods typically occur in spring and early summer, during Black Friday and holiday sales, and sometimes in the back-to-school season.
As homeowners embark on their latest projects, DIY stores face a surge in demand that can stretch port operations to their limits. That’s where warehouse automation solutions step in, transforming the way we handle inventory and fulfil orders.
At Element Logic, we’re at the forefront of this revolution, offering solutions that turn the chaos of peak seasons into smooth, efficient operations.
In this blog, we’ll explore how our cutting-edge automation technology is helping DIY retailers navigate the complexities of port operations, ensuring that your shelves stay stocked and your customers stay happy — no matter how busy it gets.
The challenges of peak seasons in DIY retail
Peak seasons in DIY retail are a double-edged sword. While they bring increased sales, they also present a host of challenges that can test even the most seasoned operators.
Firstly, there’s the rollercoaster of seasonal demand. Spring brings a flood of gardening enthusiasts, while Black Friday sees a rush for power tools and other electronics. This fluctuation makes inventory management a complex puzzle.
Space becomes a premium commodity during these times. Warehouses and ports struggle to accommodate the influx of goods, leading to potential bottlenecks in the supply chain.
Staffing issues also rear their head. The need for temporary workers can lead to training hurdles and potential errors in order fulfilment.
Moreover, the sheer variety of products in DIY retail — from tiny screws to bulky lawnmowers —adds another layer of complexity to storage and handling.
These challenges, if not addressed effectively, can lead to delays, errors, and ultimately, unsatisfied customers. However, automation offers promising solutions to these issues.
The role of automation in meeting increased demand
Automation is revolutionising the way DIY retailers handle peak season demands, particularly in pick and pack operations at ports. It’s not just about replacing manual labour — it’s about creating smarter, more efficient systems.
At the heart of this transformation is the Automated Storage and Retrieval System (ASRS). These systems, like our AutoStore solution, use robots to retrieve and store items in a compact grid. This means faster, more accurate picking and packing, even during the busiest periods.
AutoStore is like a giant 3D chessboard for your inventory. Imagine a grid of bins stacked from floor to ceiling, with robots zipping across the top, retrieving and delivering items as needed. It’s efficient, it’s compact, and it’s incredibly fast.
How does this address peak season challenges?
- It maximises space utilisation. AutoStore can store up to four times more inventory in the same footprint as traditional shelving. This helps ports handle increased stock levels without expanding physically.
- It improves accuracy. Automated systems reduce human error, ensuring the right products are picked and packed every time. This is crucial when dealing with the vast array of DIY products.
- It speeds up operations. Robots can work 24/7, retrieving items in seconds. This helps meet customer expectations for fast delivery, even during peak times.
- It reduces reliance on temporary staff. While human oversight is still important, automation minimises the need for large seasonal workforces.
- It’s flexible: AutoStore’s modular design means it can be easily expanded or reconfigured as your needs change.
AutoStore isn’t just about storing more stuff — it’s about creating a smarter, more responsive supply chain. It’s helping turn warehouses and port operations from bottlenecks into strategic assets, especially during those crucial peak seasons.
Enhancing efficiency with Element Logic’s software solutions
While hardware like AutoStore forms the backbone of automation, it’s our software solutions that truly bring it to life. Our eManager software is the brain behind the brawn, optimising every aspect of warehouse operations.
How does eManager reduce handling times?
- Intelligent order batching: It groups orders strategically, minimising robot movements and maximising efficiency.
- Dynamic slotting: The software continually reorganises inventory, placing high-demand items in the most accessible locations.
- Optimised picking routes: Advanced algorithms determine the most efficient picking sequences, slashing handling times.
But what about increasing available bin locations? eManager’s got that covered too:
- Bin optimisation: The software suggests optimal bin configurations to maximise storage density.
- Predictive replenishment: By anticipating stock needs, eManager helps maintain optimal inventory levels, freeing up valuable bin space.
- Real-time inventory management: Continuous stock control allows for better utilisation of available space.
By seamlessly integrating with existing Warehouse Management Systems (WMS) and offering cloud-based access, eManager doesn’t just improve efficiency — it transforms how you manage your entire operation.
These software capabilities significantly reduce handling times and increase available bin locations, leading to more efficient and productive AutoStore operations—a crucial advantage during peak seasons.
Supporting businesses during peak seasons
At Element Logic, we understand that peak seasons can be make-or-break for DIY retailers. That’s why we offer comprehensive support to ensure your automated systems perform when you need them most.
Our solutions are designed for scalability and flexibility. Need to quickly ramp up capacity for the spring gardening rush? We can help you expand your AutoStore system with minimal disruption to ongoing operations.
We’ve helped numerous businesses navigate their busiest periods successfully. Our team works closely with each client to understand their unique challenges and tailor our solutions accordingly, ensuring smooth operations even during the most demanding peak seasons.
Future of DIY retail automation
The future of DIY retail automation is exciting. We’re seeing trends towards even greater integration of AI in warehouse operations, enabling predictive inventory management and personalised customer experiences.
At Element Logic, we’re working on innovations like intelligent robotic piece picking and seamless order fulfilment. We envision warehouses that not only respond to demand but anticipate it, adjusting operations in real-time.
The potential is enormous: imagine a supply chain so efficient that stock-outs become a thing of the past, or a system that automatically adapts to seasonal trends without human intervention.
As technology evolves, we’re committed to keeping our clients at the cutting edge of retail automation.
Automation is no longer a luxury for DIY retailers — it’s a necessity, especially during peak seasons. With Element Logic’s solutions, you can turn the challenges of busy periods into opportunities for growth.
Ready to revolutionise your operations? Let’s talk about how we can help your business thrive.