A brief guide to mastering warehouse health and safety
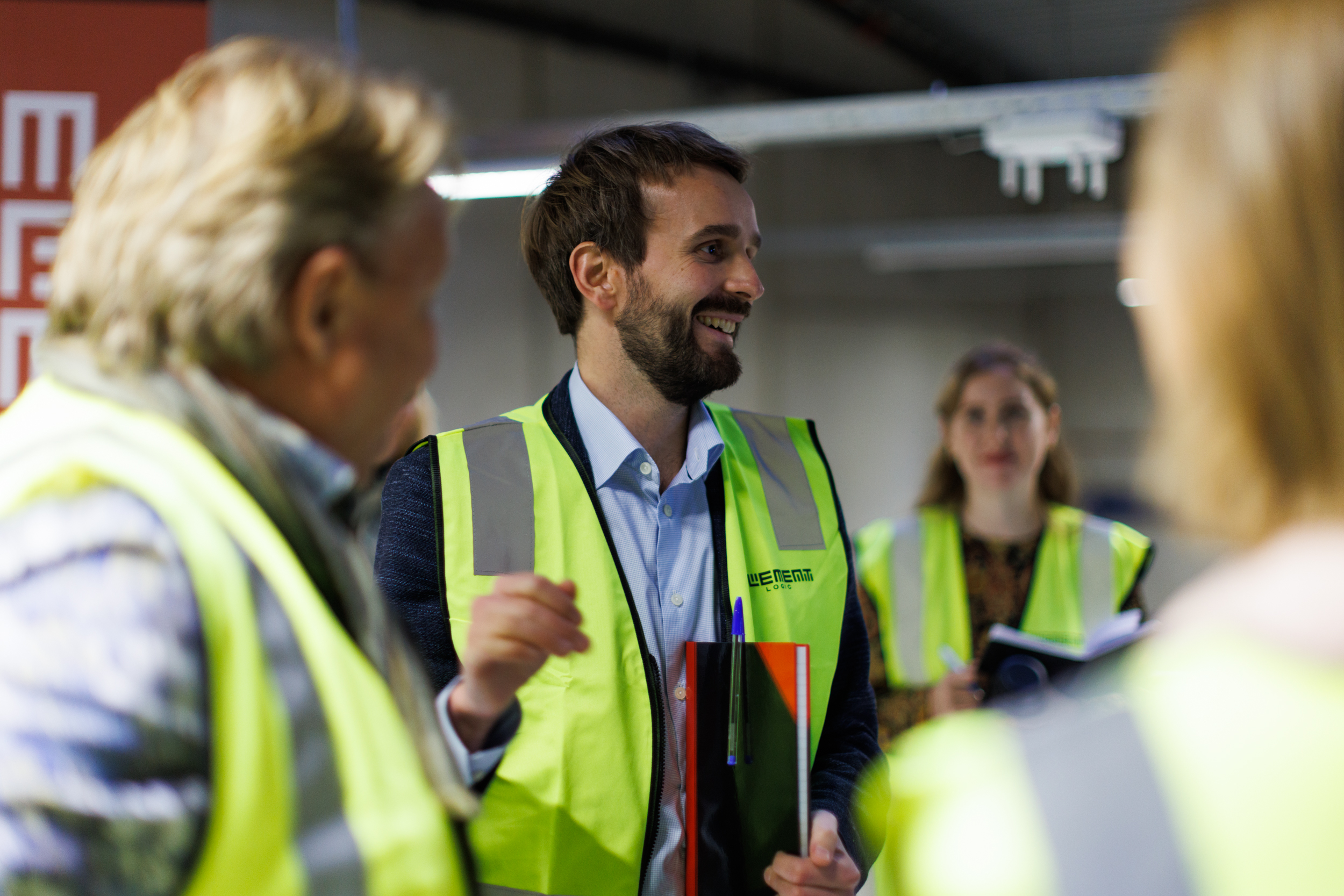
A Forbes survey from last year revealed a sobering truth – warehouse work ranks as the third most dangerous job in any industry.
This statistic underscores the critical importance of improving warehouse health and safety, including building awareness of the risks involved and implementing strategies and tools to enhance worker safety and wellbeing. Automation and robotics offer powerful new solutions for handling hazardous, repetitive tasks such as transport and heavy lifting, significantly reducing the risk of worker injuries.
This blog spotlights the essential elements of a robust warehouse health and safety programme and technology’s indispensable role in warehouse safety best practices.
Defining warehouse safety
Warehouse safety involves adopting various strategies, guidelines, and preventive measures to avoid injuries, accidents, and hazards in a warehouse environment. These safety protocols include equipment usage, warehouse layout optimisation, worker training, and integrating robotics and automation.
Investing in warehouse safety is crucial as it minimises risks and enhances operational efficiency and productivity. Major safety hazards in warehouses typically encompass issues like slips and trips, working at heights, manual goods handling, falling or moving objects, and the movement of vehicles in and around the warehouse.
Why is warehouse safety important?
The primary reason for having warehouse health and safety measures is to provide protection, preventing injuries or more severe outcomes for everyone working within the facility. The Occupational Safety and Health Administration (OSHA) recognises warehouses as one of the most hazardous work environments in the industry. A significant number of incidents each year result from sharp or falling objects, high heat or excessive cold, forklifts, and other material handling equipment.
Additionally, warehouse employees are subject to various other risks that may lead to severe health conditions, including vibration syndrome, hearing loss from loud machinery, respiratory diseases from airborne dust and particles, or chemical illnesses. Beyond safeguarding physical wellbeing, maintaining a safe warehouse environment is crucial for a business’ financial health, as accidents or health-related incidents can lead to substantial legal and financial consequences.
The essential elements of a warehouse health and safety programme
An effective safety programme should encompass all aspects of warehouse operations, including hazard identification, risk assessment, and control measures. Revising and updating the programme regularly to reflect changes in operational practices, equipment, or regulations is vital.
Here are the essential elements of a warehouse health and safety programme:
1. Risk assessment and evaluation: Before introducing safety protocols, it’s crucial to pinpoint the existing risks within the warehouse. Conducting regular audits and inspections helps locate potential hazards and set subsequent safety priorities.
2. Training and education: Equip your staff with the necessary knowledge and skills to operate equipment safely. Continuously revise training sessions to meet changing risks and challenges.
3. Safety protocols for equipment operation: Establishing clear guidelines for operating equipment like warehouse automation systems, forklifts, conveyors, and pallet jacks is vital in reducing accidents and boosting safety in the warehouse.
4. Utilisation of safety equipment: Using appropriate safety gear, such as personal protective equipment (PPE) and machinery with built-in safety features, is essential for preventing accidents.
5. Technology integration: Implementing sensors, alarms, and surveillance cameras can aid early risk detection and improve incident response.
6. Emergency response plans: It’s important to have well-defined and accessible emergency procedures for fires and medical emergencies, which employees should regularly rehearse.
7. Regulatory compliance: Following national and local safety standards sets a foundation for safety practices and minimises potential legal liabilities.
Technology’s role in augmenting warehouse health and safety
With ongoing technological innovations, warehouses can now access an expanding toolkit to bolster safety. These include:
- Automated Storage and Retrieval Systems (AS/RS) like the AutoStore system enhance safety by concealing all potentially dangerous and moving parts away from operators. The only moving part that operators can access is the bin at a port, which includes safety functions to halt movement if something is wrong or the operator makes a mistake. This increases warehouse safety and uptime since the risk of human errors is substantially minimised.
- The Internet of Things (IoT) uses technology to monitor health and safety conditions, such as air quality, temperature, sound, and worker activity, helping to monitor and safeguard the physical health of the workforce.
- Wearable technology, such as smartwatches, helmets or vests, can track vital signs to prevent workers from experiencing excessive strain or heat and detect signs of fatigue.
- Radio frequency identification (RFID) tags enable real-time tracking of goods, facilitating safe and optimal storage while reducing the risks associated with overstocking and mishandling.
- Machine Learning and AI can anticipate equipment failures by analysing historical data, making preventative maintenance possible.
- Warehouse drones can perform safety inspections of infrastructure, reducing the risk associated with climbing ladders. Smart drones also have hazard detection sensors to identify gas leaks, fires, and structural damage. In cases where a worker might become trapped or lost, drones equipped with thermal cameras can swiftly locate the individual and alert emergency services.
- Sensors in the warehouse can detect unusual movements or changes in conditions, helping to prevent accidents and machinery malfunctions.
- Video surveillance ensures real-time monitoring and strict adherence to safety protocols and guidelines.
- Alarm systems provide immediate alerts for potential risks, such as fires or security breaches.
- Automated guided vehicles (AGVs) minimise human involvement in high-risk tasks, reducing accident rates.
How warehouse automation improves health and safety
Automation equipment like AS/RS, robotic piece picking arms, AGVs, and conveyor belts, handle repetitive, physically strenuous, or hazardous tasks, such as lifting heavy items. This reduces the risk of injuries like strains and sprains frequently seen in warehouse environments.
Automated systems also follow precise and consistent protocols, decreasing the likelihood of accidents resulting from human mistakes, such as improper equipment handling, non-compliance with safety regulations, or incorrect storage methods that could cause hazardous spills or falls.
For example, AutoStore robots handle storage bins by moving along the top of an aluminium framework or grid. This eliminates the need for workers to enter the grid area and risk being struck by a moving robot or falling from heights. The system’s automated bin handling process also removes the need for workers to manually lift or carry heavy bins, preventing potential back injuries or strain from repetitive lifting.
Many automated systems have sensors and connectivity that can monitor real-time warehouse conditions. This capability enables the early detection of potential hazards like bin jams or robot malfunctions. For instance, AutoStore’s advanced sensor technology, including light curtains and laser scanners, ensures precise movements of the robots and immediately stops them if an obstacle or worker is detected within the grid area, preventing potential collisions.
In traditional warehouses, the movement of equipment like forklifts can endanger floor workers. Automated systems can synchronise these movements, optimising the traffic flow and minimising the risk of collisions or other incidents. Smart systems may incorporate features like collision avoidance and controlled access to restricted areas to ensure a safer workplace.
Building a culture of continuous care
In conclusion, a robust warehouse health and safety programme is critical for maintaining the efficiency and wellbeing of any operation. Emphasising proactive risk management strategies, comprehensive training sessions, and regular audits can dramatically reduce workplace incidents. Technology plays an indispensable role in enhancing these safety measures.
Innovative tools such as automated data collection, real-time monitoring systems, and AI-driven predictive analytics are revolutionising safety management in warehouse environments. By integrating these technologies, businesses can not only adhere to high safety standards but also foster a culture of continuous improvement and care that benefits everyone in the workplace.
Ready to explore warehouse automation solutions that prioritise worker safety and productivity? Contact Element Logic today to learn how our cutting-edge technologies like AutoStore can transform your warehouse operations.