Warehouse control system (WCS) – what is it, and why do you need one?
A warehouse control system is an essential addition to any modern warehouse operation. The ability to automate more mundane floor tasks enables employees to be redeployed into more stimulating roles, as well as making the warehouse safer.
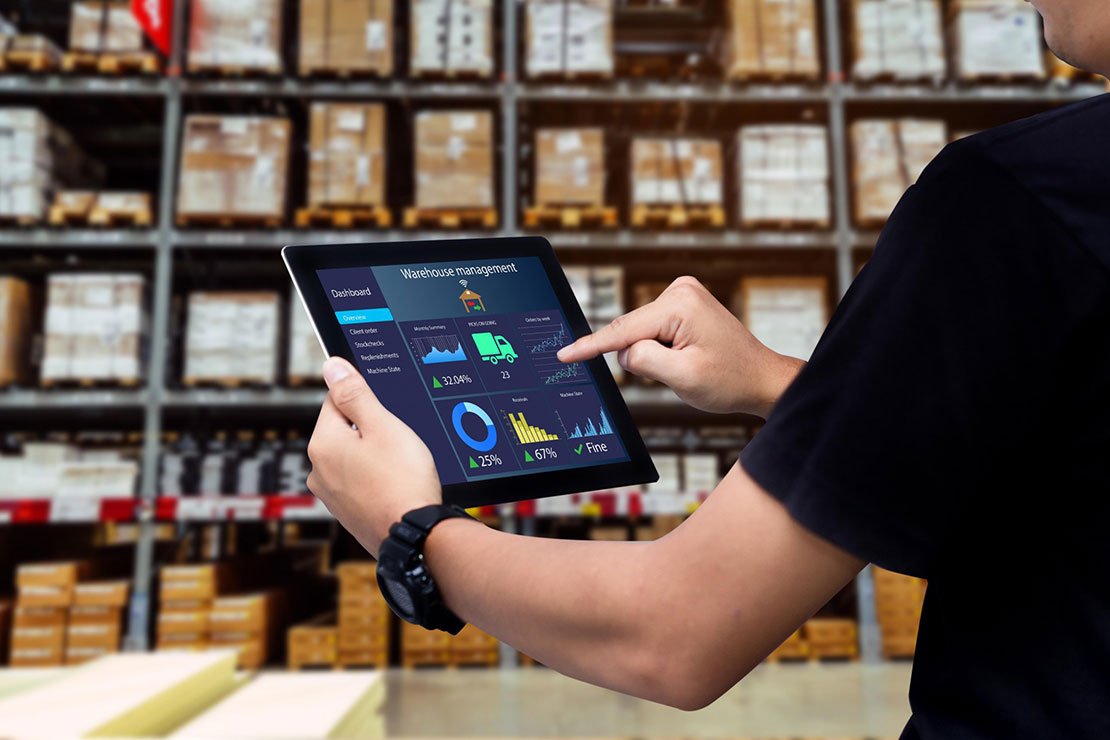
Four pillars of a good warehouse control system
In the world of e-commerce, supply chains operate at a fast-moving pace, requiring quick and accurate order fulfilment. Effective warehouse management is crucial for ensuring seamless delivery.
A proven strategy for optimising warehouse operations and improving inventory flow is incorporating a warehouse control system (WCS) that seamlessly integrates with the existing warehouse management system (WMS).
Warehouse control system definition
A warehouse control system is a software tool that assigns tasks to specific equipment within a warehouse, such as conveyors, sorters, carousals and Automated Storage and Retrieval Systems (ASRS). It achieves this by connecting to and obtaining data from a host system (in this instance, a WMS).
This fosters a seamless flow of inventory throughout the fulfilment process and enhances the overall efficiency of warehouse operations.
Functions of a warehouse control system
A WCS transmits vital information to a higher level “host” software which typically refers to a WMS. Even though the WMS collects information on overall inventory and fulfilled orders, it cannot track inventory movement throughout the entire fulfilment cycle. This lack of information ultimately obstructs warehouse optimisation since operators simply do not have the necessary data to identify areas that need improvement.
A WCS maintains a constant communication with all automated solutions in the warehouse and collects data from sensors attached to the equipment to monitor their real-time status. It also calculates the most efficient route for transporting products across the warehouse. This is highly advantageous for warehouse organisation as it enables all connected equipment to synchronise their movements for optimal efficiency.
What are the pillars of a good warehouse control system?
Understanding the key components of an automated warehouse control system architecture is crucial, regardless of whether you are starting from scratch or upgrading an existing WCS.
Here are four fundamental pillars of a good WCS:
1. A flexible interface
A WCS with a user-friendly interface can be seamlessly integrated with multiple devices, thereby minimising disruption and ensuring consistency between various activities within the warehouse. This ultimately leads to enhanced warehouse management and optimised performance as operators can conveniently track inventory, labour and equipment conditions from a single location.
2. Planning tools
Warehouse control systems offer enhanced planning capabilities that can significantly increase the efficiency of a warehouse. One of the primary ways in which this is accomplished is by segmenting orders based on product, which helps prevent orders from getting mixed up at different stages of the fulfilment process. This, in turn, leads to faster and more accurate order fulfilment.
3. Data integration and automation
Any reliable WCS should have automation at its core, seamlessly integrating with the existing infrastructure of the warehouse. This includes incorporating essential equipment such as sortation control systems and automated storage and retrieval systems (ASRS).
ASRS, such as AutoStore powered by Element Logic, can help with increased efficiency and productivity, enhanced accuracy, and far fewer, if any, picking errors.
Additionally, automated data-driven warehouses are also more scalable; as multiple WCS can be added to cope with additional equipment to increase capacity.
4. System visibility
One of the key advantages of using a WCS is the ability to track and monitor the condition of automated warehouse equipment and daily activities. This offers greater control over warehouse operations and a better workload balance for employees.
Having visibility into equipment performance and condition allows operators to ensure compliance with regulatory standards and proactively maintain equipment. Alerts can be set up to flag any issues as they arise, allowing operators to fix them before they become major problems.
At Element Logic, we utilise artificial intelligence (AI) technology in our in-house suite of warehouse technologies, including eLogiq, eController, eManager and eOperator.
- eLogiq —This data platform collects and integrates data from multiple sources to provide valuable insights and predictions on warehouse performance. By combining data, the platform enables warehouse optimization and competitive advantage through avoiding negative trends, benchmarking, and process improvement.
- eManager — Acts as the brain behind warehouse execution, management, and control. It enhances warehouse performance, from goods receipt to outbound processes, enabling customers to optimise their AutoStore warehouse processes, boost productivity, reduce costs, and improve end-customer satisfaction.
- eController — It is a software toolbox designed to simulate automated warehouse workflows and integrate automated equipment, such as conveyor systems, box erectors, and packing machines. It provides extended control over the movement of goods and orders within the warehouse.
- eOperator — Our robotic piece-picking technology, which runs on eOperator software, integrates with AutoStore to handle orders automatically using a robotic arm. Incorporating eOperator into your warehouse operations allows for secure and accurate picking, cost-effective labour, and a streamlined supply chain, resulting in high profitability and fast ROI.
WMS vs WCS vs WES
You may have heard of the terms ‘warehouse control system’, ‘warehouse management system’ and ‘warehouse execution system’. But what are the differences between these three tools?
A warehouse control system (WCS) oversees the assignment and execution of tasks within a warehouse, such as what machine is doing what task and when. Its primary focus is on automating the movement of inventory throughout the warehouse and optimising warehouse processes.
A warehouse management system (WMS) is a centralised software system that tracks inventory, manages labour and order fulfilment, and oversees the overall operations of a warehouse. It is more of a “big picture” system that focuses on coordinating and managing the different functions of the warehouse.
A warehouse execution system (WES) is a newer type of system that combines aspects of both the WCS and the WMS. It is designed to optimise and manage the flow of goods within a warehouse by dynamically allocating resources and managing the execution of tasks across different automated systems. In essence, the WES helps operators to coordinate their automated systems and optimise their warehouse operations.
Automation done right
A warehouse control system is an essential addition to any modern warehouse operation. The ability to automate more mundane floor tasks enables employees to be redeployed into more stimulating roles, such as making the warehouse safer.
The right WCS will be intuitive, offer superior planning solutions and give operators maximum visibility over inventory.
To learn more about Element Logic’s warehouse automation solutions, including AutoStore systems, get in touch today