Four types of warehouse automation explained
Warehouse automation is a complex and diverse field – there isn’t a single solution that will work perfectly for every organisation.
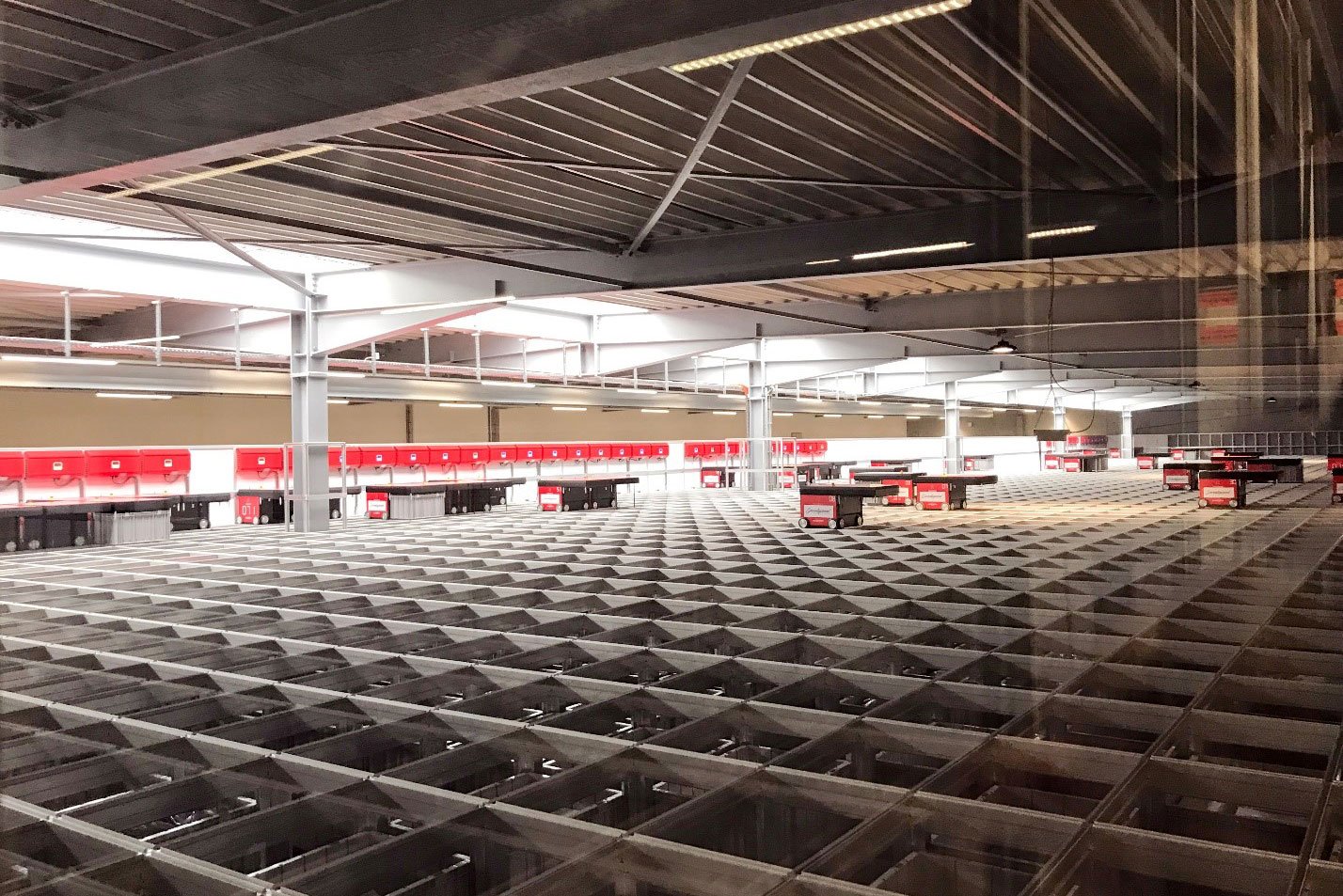
There are different types of warehouse automation – from basic to advanced – involving a variety of different technologies that can be used, and specific processes that can be automated, depending on your warehouse setup and objectives.
Warehouse automation can also refer to more than just the storage and retrieval of goods. A range of “back room” tasks, such as order management, inventory management and reporting, can also be automated.
Generally, there are four main types of warehouse automation which will be discussed in more detail below.
1. Basic automation
This level of warehouse automation is the most rudimentary and can include operations like scanning picked items and a basic conveyer system to bring the items from point A to point B. More traditional inventory transportation vehicles, such as forklifts, can also be included in this group.
A key advantage to this type of automation is its simplicity. Therefore, if a company has no prior experience with automating warehouse operations, this level would be a good place to start. The sparse nature of the solutions means they are also relatively cheap to implement.
However, this option still requires a fair amount of human labour to ensure demands are met. For example, the basic conveyer systems used here may be consistent, but their inflexibility means they are difficult to scale as operations grow and still require many workers on the floor to ensure the operation runs smoothly.
2. System automation
This type of warehouse automation involves software-based automation as well as physical automation. Typically, this variant makes use of a Warehouse Control System (WCS). The WCS is data-driven and makes it easier for operators to coordinate the identification and picking of orders. Furthermore, it allows firms to easily produce high-quality performance reports, and therefore make more informed, intelligent business decisions.
Some warehouses also use voice-assisted technologies. This typically involves equipping floor workers with headsets to receive simple voice commands – a direct line between the command systems (in this case the WCS) and the warehouse floor. Operators also have a line to communicate back and, having arrived to pick an item, must verify a code to ensure that they are in the correct section of the warehouse.
A key advantage to this warehouse automation example is, by virtue of its data-driven approach, the positive impact it can have on decision-making. Having a wealth of easy-to-access data means warehouse processes can be organised more intelligently, with an improved ability to track progress.
However, in order to be truly effective, system automation needs to be paired with physical automation (movement of orders), otherwise warehouses will continue to rely more than is necessary on manual labour.
3. Mechanised automation
When someone hears the word “automation”, this is likely what they think of. Mechanised automation involves the use of robotics to aid humans in the retrieval and transportation of inventory items. At this level of automation, Automated Storage and Retrieval Systems (ASRS) start to become prevalent. These systems are quite varied but, in general, they all have a basic function – delivering the correct items to the correct operator or workstation.
Although an ASRS can involve a rather large upfront investment, it is likely to show swift returns and, in some instances, costs can be recovered in just a couple of years. This is due to their scalability and ability to adapt to whatever space is available. A modular approach, which can only be offered by a system like AutoStore, means different components can be easily added to suit the specific needs (or limitations) of the warehouse.
Two other non-ASRS robotics systems worth mentioning are Automatic Guided Vehicles (AGVs) and Autonomous Mobile Robots (AMRs). The AGVs’ job is to transport items across the warehouse. While they do reduce dependence on human labour, they require a decent amount of space to operate in and can only travel down set paths. This means their usage is mainly confined to large, simple warehouse setups, making them a less dynamic option.
AMRs, on the other hand, are a more intelligent solution. These robots can navigate a warehouse floor independently, allowing for greater flexibility. If a warehouse is smaller and/or has a more complex setup, this is a better option than using AGVs. However, both carry health and safety risks. Being autonomous, AMRs in particular carry an increased risk of causing accidents on the warehouse floor. There is also the issue of both solutions having limited loading capacities.
4. Advanced automation
The final type of warehouse automation to cover is advanced automation. While it is considered a category here, it basically involves the combination of all previous types, resulting in a very sophisticated level of automation. The marriage of system and mechanical automation would create a complete end-to-end automation of the order fulfilment process – something that would ordinarily require a significant amount of human labour.
Automation on this scale would involve a total synergy between data-driven system automation and autonomous units on the warehouse floor. An example of this would be an advanced “wave picking” system. This system delivers items in intervals (waves) that correspond to variables such as order number or delivery destination. The system also allows firms to home in on targets, like hitting a certain number of orders in a week. Combining this system with robotic equipment, such as AMRs, would be considered an advanced level of automation.
Although this setup can yield high levels of both efficiency and investment return, the initial cost is going to be a barrier for many smaller firms. Such a high level of automation comes at a considerable price and, therefore, this kind of “total automation” is rarely seen outside of large, omnichannel retail warehouse operations.
Automation to suit all levels
It should now be clearer that automation as a concept is highly variable – there’s no “one size fits all” approach here. A small warehouse operation does not necessarily need the same level of automation that a highly complex, omnichannel delivery service does.
With all this in mind, all operations could certainly benefit from implementing a certain degree of automation in order to drive greater efficiency and growth. Therefore, the question is not so much whether automation is desirable or not, rather what kind of automation is right for which stage.
To learn more about the right automation for your needs, contact us today.