Optimise returns management with warehouse automation
Reverse logistics is one of the main challenges for companies, in terms of costs and time. Let’s explore how to reduce this burden with Element Logic’s technology solutions.
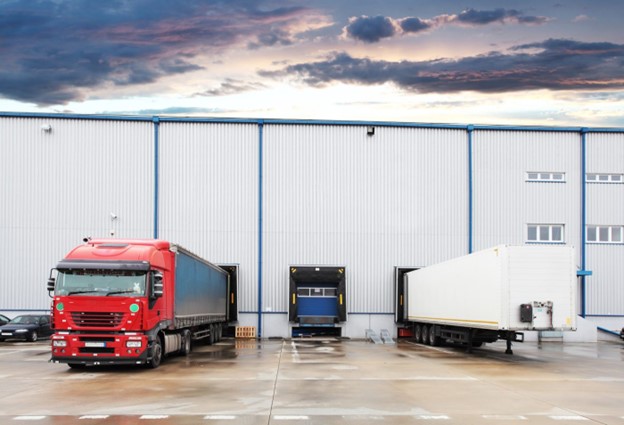
First of all, what is reverse logistics?
Reverse logistics is the process of moving goods from their final destination back through the supply chain. It’s essentially the opposite of traditional logistics, which involves getting products to customers. Reverse logistics covers everything from customer returns and product recalls to the handling of packaging materials and even the disposal of obsolete equipment.
In today’s retail landscape, particularly with the growth of e-commerce, reverse logistics has become increasingly important. It’s not just about handling returns — it’s about doing so efficiently, cost-effectively, and in a way that maintains customer satisfaction. A well-managed reverse logistics process can help companies recover value from returned items, reduce waste, and even gain insights into product quality and customer preferences.
In today’s fast-paced world of commerce, returns management (also known as reverse logistics) has become a critical factor in a company’s success. The e-commerce boom has not only increased transactions but also significantly boosted returns. As consumer expectations grow, the ability to handle returns quickly, transparently, and efficiently is now crucial for customer loyalty.
What’s the real cost of reverse logistics?
Processing returns can be surprisingly expensive. It requires several additional activities beyond standard operations to ensure returned products are handled properly and meet quality standards.
Did you know that returns can require up to 20% more space and manpower than the original order fulfilment process? This extra space is needed to move, assess, and potentially recondition returned products. It’s a particular headache in areas where industrial space is already at a premium. Naturally, this increased workload and need for more staff can put significant pressure on operating costs.
Effective returns management with AutoStore
Our cutting-edge AutoStore system is revolutionising how companies approach reverse logistics. It enables smarter, more profitable returns management while improving the overall customer experience.
At the heart of AutoStore is a three-dimensional aluminium grid and boxes that can hold up to 30 kg. High-performance robots transport these boxes to picking stations, making the most of available space and eliminating order picking errors. All robot movements are coordinated by eManager — software we’ve developed at Element Logic to meet your specific needs.
The result? Both orders and returns are managed in record time and with maximum efficiency.
This kind of warehouse automation isn’t just an answer to today’s reverse logistics challenges — it’s a milestone in shaping the future of intralogistics.
Automated returns management with AutoStore: a step-by-step guide
- Receipt of returned products: The process kicks off when a return enters the warehouse, typically using automatic scanning and identification devices.
- Product status assessment and reconditioning: Operators step in to assess the returned product’s status and proceed with reconditioning, repackaging, and relabelling if necessary.
- Classification and prioritisation: The system classifies returned products based on various criteria, such as category, product status, and handling priority. This smart approach determines which products need priority treatment.
- Insertion into the automated warehouse: Once identified, classified, and reconditioned, returned products are inserted into locations already containing the same items (reverse picking). The operator is guided to deposit products at the station in quick sequences, while AutoStore robots autonomously supply boxes for refill and move them in the warehouse.
- Reintegration into the supply chain: After these processes are complete, the product can be seamlessly reintegrated into the supply chain.
Companies that embrace our AutoStore solution can maintain a high level of competitiveness despite market complexities. They often experience a return on investment (ROI) that quickly covers the initial outlay.
Are you ready to transform your returns management process? Get in touch with us at Element Logic today, and let’s discuss how we can optimise your reverse logistics operations.